Über den Kunden
Die Hammer-Gruppe ist eine Symbiose aus Logistikunternehmen und funktionsbezogenen Bereichen mit Hauptsitz in Aachen. Der Gruppe stehen 300 Fahrzeuge zur Verfügung, sie beschäftigt 700 Mitarbeiter und erwirtschaftet einen jährlichen Umsatz von 135 Millionen Euro. Das Unternehmen versteht sich als Speditionsmanufaktur im klassischen Sinne und unterstützt seine Kunden ganzheitlich, wirtschaftlich und schnell mit präzisen Prozessen im Bereich klassische Spedition, flexible Logistiklösungen bis hin zur Kontralogisitk und richtet sich dabei exakt nach den Wünschen der Kunden. Mit traditionellen Werten und dabei technologisch immer auf der Höhe des Marktes bietet der Logistikdienstleister Transportlösungen bis hin zu komplexen Logistik-Strategien entlang der kompletten Supply Chain und ist dabei auch weltweit sehr stark vernetzt.
Der zur Gruppe gehörende Logistikdienstleister Hammer GmbH & Co. KG hat 2015 im rheinischen Bedburg bei Köln ein neues Multi-User-Logistikzentrum errichtet. Mit dem Zentrum in einer Größe von 103.000 qm, das u.a. ein Shuttle-Lager für Kleinteile beherbergt, unterstützt das Logistikunternehmen vor allem eine große Baumarkt-Kette.
Kundenanforderung
- Für das automatisierte Shuttle-Lager (Kleinteilelager) benötigt der Logistikdienstleiser ca. 60.000 Behälter.
- Die Behälter müssen sehr stabil und für automatisierte Anlagen geeignet sein.
- Die Lärmbelastung im automatisierten Lager soll so gering wie möglich sein, um eine angenehmere, weniger stressbelastete Arbeitsumgebung und Arbeitsatmosphäre zu schaffen. Entsprechend ist gewünscht, dass die neuen Behälter möglichst leise auf der automatisierten Anlage laufen.
- Es sind ausschließlich Kleinteile in den Behältern zu lagern
- Eine hohe Anzahl an unterschiedlichen Kleinteilen soll effizient kommissioniert werden.
- Die Boxen müssen über ein möglichst großes Innenvolumen verfügen, um möglichst viele Kleinteile darin aufzubewahren und zu lagern.
- Der Platz in den vorhandenen Regalanlagen soll durch den Einsatz von Behältern so effizient wie möglich genutzt werden, für einen hohen Nutzungsrad.
Die BITO-Lösung
Leisebehälter XL-Motion
» BITO lieferte 60.000 Kunststoff Behälter vom Typ XL-Motion, geeignet für die automatisierte Anwendung.
Besonders leise
» Der XL-Motion verfügt über einen neuartigen Umlaufboden. Die glatte Rahmenkonstruktion und ein ebener, glatter Behälterboden sorgen für einen geringen Reibewert beim Lauf über die Transportbänder, was die Geräusche beim Behältertransport auf der Anlage deutlich reduziert.
Besonders stabiler Sandwichboden
» Der Umlaufboden ist mit diagonalen Stützrippen an den Behälter angebunden. Diese Sandwichkonstruktion verhindert, dass sich der Boden bei hoher Last durchbiegt.
Hohes Innenvolumen
» Der Behälter mit dem Maß 600 x 400 x 320 mm verfügt über ein Innenvolumen von 53 Litern
Breiter Boden
» Der XL-Motion hat einen 25 mm breiteren Boden als herkömmliche Eurostapelbehälter.
Hohe Belastbarkeit
» Der XL Motion-Behälter kann mit bis zu 50 kg beladen werden. Sind mehrere Behälter voll beladen und werden übereinander gestapelt, kann die unterste Box mit bis zu 250 kg belastet werden.
Quer- und Längsteiler für Kleinteileaufbewahrung
» Die Box lässt sich mit schmalen und dabei sehr stabilen Querteilern und Längsteilern unterteilen.
Grifflöcher für gute Ergonomie
» Für die ergonomische Handhabung sind auf der Stirnseite Grifflöcher angebracht.
Barcodierung
» Die Behälter werden mit Bardcodes versehen, die sich vom Anlagensystem erfassen und einspeichern lassen.
Behälter aus 100% Recyclingmaterial
» Der Leisebehälter XL-Motion wird aus 100% Recyclingmaterial hergestellt.
Kundenanwendung
- Der Logistikdienstleister setzt den BITO Behälter XL-Motion in seinem Shuttlle-Lager für Kleinteile ein. Das Lager funktioniert nach dem Shuttle-Doppel-fit-Konzept.
- Die Kleinteil-Artikel lagern in einem Hochregallager. Sobald der Meldebestand des AKL unterschritten wird, erkennt dies das System und generiert Nachschub aus dem Hochregallager. Die Kleinteile werden dann von den Mitarbeitern aus Kartons in die XL-Motion-Boxen kommissioniert und anschließend über die Fördertechnik zum Kleinteilelager transportiert.
- Das Lager besteht aus fünf Gasen mit je 20 Ebenen, jede Ebene wird mit einem Shuttle bedient. Die Shuttles lagern die Boxen auf jeder Seite in jeder Gasse im chaotischen Lagerprinzip ein.
- Die Behälter bleiben dabei fast immer im Kreislauf des Systems.
- Um unterschiedliche Kleinteile in einer Box zu lagern, werden die Behälter mit ¼-Querteilen unterteilt.
Kundennutzen
- Der XL-Motion läuft extrem leise auf der Fördertechnik. Die dadurch erheblich geringere Lärmbelastung in der Halle sorgt für eine enorme Stressreduzierung bei den Mitarbeitern.
- Die durch den Leiselauf bedingte, angenehmere Arbeitsatmosphäre sorgt für eine größere Arbeitszufriedenheit, es sind weniger krankheitsbedingte- und stressbedingte Ausfälle zur verzeichnen.
- Durch das lärm- und stressreduzierte Arbeitsumfeld passieren weniger Fehler.
- Die hohe Behälterstabilität hält den extrem hohen Belastungen im Lagerbetrieb stand.
- Durch das besonders hohe Nettovolumen, bedingt durch das hohe Innenvolumen des XL-Motion, kann der Behälter mehr Ware fassen und es kann mehr Ware gelagert werden.
- Je mehr Ware jeder einzelne Behälter fassen kann, desto weniger Nachschübe sind erforderlich.
- Der hohe Ausnutzungsgrad jedes einzelnen Behälters sorgt dafür, dass bei gleicher Warenbeförderung weniger Behälter benötigt werden – dadurch werden weniger Behälter bewegt, was wiederum die gesamte Anlage deutlich effizienter macht.
- Kostenreduzierung beim Anlagenbau: Durch den breitere Boden des Behälters werden für das AKL deutlich schmalere Auflagewinkel benötigt. Das spart viel Material und somit Kosten für den Bau der Anlage.
Das sagt unser Kunde
Das Leiselaufverhalten des XL-Motion macht die Arbeit im AKL deutlich stressärmer. Wir bekommen von den Mitabeitern ein sehr gutes Feedback und jeder arbeitet gerne an den Plätzen. Das angenehme Umfeld veranlasst selbst Mitarbeiter aus anderen Bereichen, sich für die Aufgabenbereiche im AKL zu interessieren. Das leise Laufverhalten der Behälter fördert zudem die Konzentration und senkt die Fehlerquote.
Lutz Harde, Geschäftsführer Logistikzentrums Hammer GmbH & Co. KG
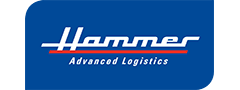
Czy udało nam się Państwa przekonać?
Będzie nam miło otrzymać zapytanie od Państwa pod nr tel.:
22 666 22 20