What is Route planning?
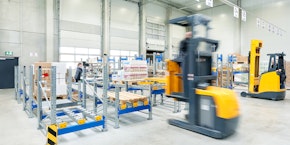
In almost every company, numerous transport processes occur - be it the delivery and delivery of materials and goods, in the production area or in the warehouse. In order to transport them from A to B in a way that saves energy, time and labour as far as possible, efficient route optimisation and route planning is required. In the warehouse area and logistics, for example, the ways in which articles are stored and retrieved are optimised in order to achieve efficiency. When supplying customers or delivering goods, the goal is optimal route planning. This is understood to mean minimising the (total) costs of the vehicle fleet while maintaining a specified performance level or achieving the highest possible performance standard within a specified budget. Daily questions such as "which customers are supplied on which Route?", "which route is selected for this trip?" and "which vehicles are to be used?" have to be answered anew. Especially with many orders and journeys, it is important to group the (transport) orders into Routes and put them in a sequence. The term "clustering" refers to the combination of various orders into a single Route. The order in which different stations within a Route are served is called routing.
Route planning: simple to highly complex
Basically, the problem of route planning is seen as a combination of the classic transport problem and the round trip problem (problem of the commercial traveller). Mathematical solutions exist for both. Route planning can include a relatively simple task of homogeneous transport goods and fixed customer structures with few routes and customers. But it can also become highly complex - especially when it comes to heterogeneous quantities of goods, changing recipients and daily changing restrictions on routes and routes for a large fleet of vehicles. Restrictions include, for example, time windows, several depots or any start and destination points as well as priority relationships between orders. In addition, the slots allocated or booked by time window management must also be adhered to by the customer. In dynamic route planning, the order situation also frequently changes continuously during planning, e.g. due to new or cancelled orders.
Route planning software is the means of choice
Due to their complexity, companies nowadays usually use standard software or specially programmed software for planning journeys. The route planning software uses a digital road network, a customer master file, a vehicle and driver list as well as a current order list as a database. This allows a large number of restrictions in logistics to be taken into account and a large number of optimized trips and routes to be calculated quickly. Optimisation is achieved by combining the transport requirements of a number of customers into one or more Routes in such a way that customer time schedules, vehicle loads and capacities, driver break and working times and vehicle maintenance cycles are adhered to, while transport costs are minimised.
A further improvement can be achieved by including the mobile data acquisition of the transport vehicles. The current environmental situation is also evaluated. In general, the planning of Routes using software increases the quality of service, as all components of the complex transport task are taken into account. In addition, the software allows rapid adaptation to daily changing demand by minimizing disposition errors in logistics, e.g. due to incorrect estimation of vehicle capacities in terms of time and space.
Where do companies need route planning?
Route planning is important for companies both for incoming and outgoing goods. For example, time windows are assigned to external service providers and suppliers at goods receipt. Using software, they can also book time windows via the extranet. The use of time window bookings enables ideal capacity and resource planning. The time window control benefits not only the companies but also the suppliers. For example, traffic jams at incoming goods and demurrage charges are avoided, loading and unloading times are shortened and communication between drivers and gate staff is facilitated.
In the outgoing goods department, the capacity utilization of the means of transport and vehicles as well as the delivery date planned by the customer must be observed. The transport dispatcher optimizes all trips and the routing for the delivery to the customers by means of a route planning software. In addition, the correct implementation of guidelines and specifications regarding transport must be taken into account. This includes, for example, the proper planning and execution of transports requiring refrigeration and those requiring refrigeration chains. The goods issue forms must also be updated.
Advantages of route planning
Optimum route planning leads to lean processes and short delivery routes. The entire fleet is optimally utilized and amortized. The efficiency of all processes is increased. In general, customer satisfaction and employee satisfaction are increased because reliable deliveries are made within the desired time windows. The planning of Routes and associated logistics results in increased process transparency. Route planning becomes a verifiable part of the supply chain. The route planning software can also be linked to GPS tracking. It is therefore possible to carry out the optimisation at any time on the basis of the actual coordinates of the vehicles. In addition, the respective location of the vehicles is clearly displayed at all times.
Which warehouse technology helps with route planning?
Through the use of flow racks (pallet flow racking (PDS) or piece goods flow racking systems (SDS)), the incoming goods or the loading and the outgoing goods, i.e. the removal, can be spatially separated from each other. The goods throughput is based on the First in First out (FiFo) principle, whereby the transport routes are shortened overall. The automatic advancement of the articles during removal saves time. The area of the warehouse is optimally used compared to conventional racking (around 60 percent more). In the dynamic PDS or SDS, the goods are stored homogeneously and usually removed with a high turnover rate. They therefore represent a good and flexible solution for use in incoming and outgoing goods.
Brake support rollers ensure controlled passage of the pallets. In order to enable easy removal of the pallets without "back pressure", a separating device is located on the removal element which separates the front pallet from the remaining pallets in the channel.