Save costs through warehouse optimisation
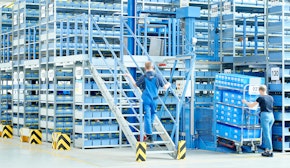
A warehouse can tie up an enormous amount of capital and increase costs - especially if incorrectly planned. Given the low margins and high demands in retail and logistics, no company can afford to not investigate the potential for storage optimization these days. Fortunately, storage technology experts can help optimize storage space, increase storage density and implement appropriate storage technology.
Optimal use of space
The space required for a load should ideally always be optimised. The largest use of storage space is block storage, when goods are stacked on pallets and stored close together on the floor. However, block storage is only suitable for stackable goods on or in load carriers such as pallets, crates or stillages. Furthermore, the full height of the building can often not be used. Block storage is also not at all efficient for picking or general access, which can result in increased handling costs and loss of time.
If fast, efficient item picking is not a priority, a fairly simple option to keep wasted space to a minimum is to install narrow aisle racking or a mobile racking system. Very narrow aisle (VNA) racking provides good use of space in that the racking covers the maximum space due to the aisles being narrow and the racking height being maximised. Full pallet retrieval is possible with man-down, high-lift stackers, or man-up-order-picking stackers. With mobile racking systems, the individual bays can be moved electronically or manually on rails. Possible perceived drawbacks of mobile racikng are the relatively high investment costs, waiting times for the opening of the required bay as well as the necessary safety guidelines. Nevertheless, a clever putaway strategy can overcome these possible drawbacks. High-bay racking enables the full height of a warehouse to be used while the space and area utilisation rate of the warehouse is high. The utilisation rate is the quotient of the net area occupied by storage units (area effectively available for storage) and the total area of a storage facility.
Location utilisation in high-bay warehouses tends to be controlled by a complex material flow managed by computer software.
Further storage systems with good space utilisation
Other storage systems with a high degree of space utilisation are drive-in racking and flow racking. In general, the compact arrangement of the flow channels next to and above each other creates a high storage density and thus leads to the best possible utilisation of the warehouse capacity. Compared to conventional shelving, the degree of space utilization is around 60% higher. Furthermore multi-tier shelving systems (MGA) and compact warehouses with shuttles, such as BITO's ProMotionShuttle, also have a very high degree of space utilisation.
The stacker-operated ProMotion system retains the compact nature of drive-in racking, increases flexibility and reduces the effort involved in storing pallets. The shuttle is moved from one storage channel to the other using a conventional forklift and is controlled via a robust radio remote control so that it transports the stored goods independently through the channel. The system is an alternative to drive-in, push-back or pallet live racking.
Optimised storage through correct container selection
Space saving containers allow an optimal utilisation of a company's valuable storage space. They are matched to the dimensions of the euro pallet and can be nested very well inside each other or folded up when empty. Heavy duty SL containers made from tough polypropylene by BITO are exactly the size of a half euro pallet (800 x 600 mm). Due to the market trend to ever smaller batch sizes, there is a demand for smaller load carriers. The advantage is that more articles can be stored in the same area. They are considerably lighter than stillages and sheet steel containers. Small parts bins and containers with longitudinal and sideways dividers enable each compartment size to be adapted to the pack size of the articles. Another option is the system of cut to length subdividers which are supplied in standard lengths and can be cut to the desired size to personalise the container. Euro stacking containers can be sub-divided with box inserts that are available in 1/2, 1/3 or 1/4 sizes.
Review the product offer
Another option to save valuable warehouse space is to review the throughput of the product range offered and cull non-moving items. An inflated product range leads to inefficient logistics and wasted space. If feasible, the warehouse should therefore be freed from slow moving and discontinued lines or a separate small quantity warehouse should be set up for residual quantities. Ideally, assortment planning should include the ABC and XYZ analysiswhich should, in turn, influence the pick locations of each line.
Of course, the more frequent delivery of smaller quantities of articles can also save space in the warehouse. Thanks to Kanban systems and just-in-time delivery, it is possible to almost completely dispense with a warehouse (with the exception of buffer warehouses) - extreme warehouse optimisation, as it were.