More efficiency through paperless picking
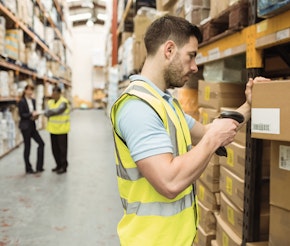
The printed picking list, the pickers‘ "shopping list" in the order processing team, is still very often a fundamental element rquired for warehouse item picking. The order picker holds the picking list in one hand, with the other hand they check off order items with a biro or note down missing stock. That works - but is it efficient? As soon as the number of orders exceeds a certain level, companies should consider the more efficient processes of paperless picking - processes that are completely paperless and make work much easier.
Paperless picking methods
Paperless picking methods include:
· Pick-by-scan
· Pick-by-light
· Pick-by-voice
· Pick-by-vision (picking via data glasses)
· Pick-by-terminal
· Pick-by-point
Pick-by-Scan/ Pick-by-MDE
Pick-by-scan is the most common type of paperless picking, using mobile handheld computers with integrated 1D or 2D barcode scanners. The device displays the storage location and the picking quantity and guides the picker step by step through the order. The employee must either confirm each item picked via barcode or the total quantity at the end of the picking process. Target/actual differences are displayed to prevent the order from being inadvertently completed. The data of the processed items are transmitted to a warehouse management system (WMS) and packing lists and shipping documents are printed afterwards. Even with chaotic storage, each item can be found quickly. A low-cost entry-level version with smartphones can be used. For more user flexibiity, using a data glove scanner enables picking with both hands.
Advantages
· Efficient working due to simple and fast capture of barcodes and complete elimination of cumbersome paper handling compared to document based picking
· Error prevention, goods are scanned unequivocally and unambiguously, hardly any returns due to picking errors
· Work without physical picking lists
· Transparency, as the picks are tracked on computers for future reference
· Cost-effective: Barcodes are extremely reliable identification systems with an unbeatable price/performance ratio.
· Low-cost entry level version when using smartphones
Disadvantages
· Hands are only free when using a data glove
· Misreading possible due to dirty or illegible labels/barcodes
· Investment costs up to £2000 per unit (plus additional system and training costs). However, smartphones can also be used with the entry-level version.
Pick-by-Light
In this paperless process, operators are guided to the pick location or order bin by means of optical signals. There is a signal lamp and display, which shows the employee the article to be picked, the required quantity and other relevant information. The employee then confirms the completion of the picking process by pressing the acknowledgement button, which is also attached to the display. This information is then transmitted in real time to the ERP or WMS. Correction keys (+/-) can be provided for correcting the pick quantity (e.g. in the case of stock shortages) or for inventory functions - additional function keys can also be provided for calling up special functions. Pick-by-light is particularly suitable when a high picking speed is required. The system is often used in combination with automated warehouse solutions in which the articles are provided according to the goods-to-person principle.
Advantages
· Fast picking
· Reduced error rate
· High picking frequency per storage location
· No long training period
· Employees have their hands free
Disadvantages
· Comparatively high costs for acquisition, maintenance and repair
· Inflexible, as adjustments to storage location, article or number have to be made to the displays in a time-consuming process
· Pick error in case of undetected failure of the machine
Pick-by-Voice
The paperless picking method pick-by-voice has become very popular as it gives the picker maximum freedom of movement and flexibility in their work. The warehouse worker wears only one headset, through which they receive picking orders by computer voice. Pick by voice requires hardly any training and thus enables the quick training of temporary and seasonal workers. The orders are sent by the WMS via wireless and then reported directly back to the system in the same way. Once an order has been completed, the employee acknowledges this via a confirming voice entry. The pick-by-voice system tells the user what to do, detects errors in real time and gives users the opportunity to ask questions and receive immediate assistance.
Advantages
· Short search times
· Precise picking
· Employees have hands and eyes free
· Freedom of movement and flexibility
Disadvantages
· High initial investment
· Limited use with high noise levels in the bearing
· Multilingual versions may be required
· More complicated incorporation
Pick-by-Vision
The process combines the advantages of pick-by-voice and pick by light in one system. The order picker wears data glasses into which relevant data on the current order is fed in real time. They are then guided step by step through the order. Using the navigation function, the operator is guided directly to the pick location, where they are shown the corresponding storage location including the required pick quantity via an optical display. In addition, the data glasses can be extended by a camera for the acquisition of barcodes. The advantages are that the user can clearly perceive their surroundings and have both hands free to process the order. In addition, the order picker can interact with the control system thmselve and make changes using voice control.
Advantages
· Unobstructed view and free hands
· With built-in camera for barcodes a scanner is not required
· Additional feedback via voice function
· Short search times
· Precise picking
· Freedom of movement and flexibility
· High picking frequency per storage location
Disadvantages
· Still new and immature
· Relatively expensive
Pick-by-Terminal
In this example of paperless picking, data is wirelessly transmitted to a fixed terminal, often atached to a forklift truck. Scanners are used to record the article, serial or batch numbers and labels printed to be attached to the picked goods for identification. Companies handling large and bulky goods often like to use this picking method. Since the operation of the terminal is quite intuitive, the time-consuming training of pickers is no longer necessary. The error rate is very low, but language barriers of the employees can become a source of errors.
Advantages
· Low error rate due to the use of scanners
· Perpetual inventory possible
Disadvantages
· Picking performance is lower when compared with pick by voice and pick by light.
Pick-by-Point®
Pick-by-Point® is a form of paperless picking whereby the picker receives information about the shelf from where they have to pick the goods via a light beam in the shelf aisle. In addition, an illuminated display shows the number of articles to be picked. The monitoring of the shelf fronts can be realised by a laser sensor, for example. If the order picker reaches into the wrong shelf compartment, a warning signal sounds. The picking is typically confirmed by barcode scanning.
Advantages
· system offers high picking performance with low error rate
Disadvantages
· high installation and maintenance costs, as each storage compartment must be equipped with electronics
Barcodes and WMS as prerequisites
The individual requirements of the company (and its budget) determine the choice of picking method. The basic advantages of the individual methods are always similar:
· Cost savings primarily through reduced item search times
· Clean documentation of all goods and material movements - increased transparency
· Increase in performance.
· Improvement of delivery quality, reduction of the error rate
The main requirement for all procedures is that the storage locations and also the articles must be equipped with barcodes. A Warehouse Management System (WMS) is also required for control. The picker can be guided through the picking zone by the WMS in a route-optimised way.
"Pick-by-light" is typically used in BITO's general cargo flow rack systems. We create the conditions for paperless picking and equip the picking systems accordingly. We offer a wide range of accessories for the labelling of storage locations. For the technical equipment BITO cooperates with well-known system partners.