Our customer
As an international manufacturer of filling and packaging systems for the beverage, food and non-food industries, KHS GmbH occupies a leading position in the industry. Headquartered in Dortmund, KHS GmbH achieved sales of around 1,137 million euros in 2017 with 5,070 employees. KHS GmbH is a wholly owned subsidiary of Salzgitter AG. In addition to international production sites in the USA, Mexico, Brazil, India and China, KHS develops and produces the entire portfolio of filling and packaging machines at five German locations. Especially high-performance systems, but also solutions for smaller operations are in the range. KHS GmbH is valued as a market leader and supplier of innovative, reliable and highly efficient products and services such as complete turnkey systems, stand-alone machines, conversions. Their 24/7 global on-site service is another plus.
Customer requirements
- KHS was looking for a new container series for the German production sites.
- With a new, standardized container concept, Kanban principles are to be implemented in the production, assembly and logistics areas as well as between different sites and workflows are to be streamlined.
- KHS already had a BITO carton live storage system in use, and the new containers are to fully utilize the complete depth of the 1,200 mm deep roller lanes.
- The customer needs containers with a standard length of 600 mm, in with different widths and heights.
- KHS needs a huge selection of parts for the assembly of the machines. There are therefore many different size items to store.
- An efficient, space-saving plastic container is required for storing long components that are frequently used.
- As the height of the new containers must be fully usable for the storage of small parts, the containers were not to have open handholes.
- The parts must be easy to pick during manual handling; though container width had to be limited, it should still be as easy as possible to remove the parts by hand.
- All container sizes must be compatible with each other.
- It must be easy and safe to stack the plastic boxes on the trolleys which KHS has been using as of most late to transport parts to in-plant production areas and between the locations.
- It is important that all containers on the trolleys can be seen at a glance.
- Ergonomics at the assembly site is to be improved.
- Container handling must be particularly convenient, as even heavy parts up to 18 kg must be carried.
- The containers must be particularly sturdy to prevent base deflection when storing heavy components.
- The other plants are also to gradually switch to the new containers.
The BITO Solution
- EMB stacking container series in modular sizes
» BITO had its own tool built for the EMB stacking container series customized for KHS.
- Standard container length 600 mm, different widths
» The modular containers are always 600 mm long and are available in widths of 133 mm, 266 mm and 400 mm. The width of two narrow containers (133 mm) equals one medium-width container (266 mm), whereas three 133 mm-containers are compatible with the largest container width of 400 mm. One medium-width (266 mm) and one narrow-width container (133 mm) are interstackable with the 400 mm wide container. BITO supplied EMB containers in two height options of 142.5 mm and 270 mm. The stacking height of two 142.5 mm containers corresponds to the height of a 270 mm container.
- Stacking compatibility
» EMB formats have been cleverly designed: They perfectly fit on a Euro pallet, in a 1,200mm deep flow rack and a 600mm shelf trolley (many other Kanban bin formats are not that versatile).
- Parts are easy to pick
» At 133 mm wide, the narrow EMBs are still wide enough for convenient manual small parts picking.
- Particularly solid ribbed base
» EMBs have a strong ribbed base in modular European dimensions suited for high load capacities. This means that mixed stacking of containers with different sizes is easy and, above all, safe.
- Ergonomic handles
» The cup handles are perfect for manual handling tasks such as lifting, carrying, pushing and pulling. The smooth inner sides provide a large filling volume.
- Easy to clean
» The inside surfaces without recesses are easy to keep clean.
- Ideal for use in Kanban systems
» The EMB fits perfectly in shelving with inclined shelves or in carton live storage racks which are frequently used in Kanban production and assembly processes.
On-site application
- KHS essentially uses a two-bin Kanban system to supply production and assembly areas – supplemented by conventionally provided material supply.
- As part picking at the workplaces is essentially a manual process, ergonomic shelving heights are used in the replenishment areas.
- At the workstations, the same EMB containers with the same contents are always available so that operators know exactly where to reach without losing time.
- A wide variety of items are stored and transported in the EMB containers, from small parts to heavy loads and long components.
- The containers are filled by a logistics services provider and loaded onto trolleys.
- A trolley shelf is half the size of a Euro pallet (1,200 x 600 mm) and carries all the parts needed to make an assembly. Accordingly, the trolleys supply the required number of containers. A set of trolleys is attached to a tugger train, which supplies the individual assembly stations.
- The tugger train also returns empty containers to the filling stations.
- All containers are barcoded for immediate content identification.
- All reference lines have been assigned a fixed storage position so operators know the correct place of each container.
- Thanks to the modular concept, EMB containers of all sizes can be interstacked.
Customer benefits
- The new containers have significantly improved the material flow process and made work much easier.
- The standard container length of 600 mm is perfect for storing long loads.
- The favourable width-length ratio enables full use of the entire container volume, especially when storing long components.
- At a length of 600 mm, EMBs make best use of space in carton live storage racks. Regardless of the container width and height, the roller tracks of a flow shelf can always accommodate 2 containers in depth. The use of EMB containers has increased volume utilisation in the racking by up to 40%.
- In the past, the existing space for container refilling was often too small. It can now be used efficiently thanks to the new container sizes. The space required for material supply at the assembly stations is now in very good proportion to the number of parts provided.
- Improved ergonomics at the assembly stations, only a few containers are not within easy reach of the operator.
- Quicker access to the parts
- Despite different widths and heights, EMB containers securely interstack and do not tip over during transportation. No additional load securing is required.
- Container stacks are stable even when large containers are stacked on top of smaller ones. No restacking necessary.
- Space on the tugger train trolleys is now being used perfectly.
- Faster overview of the contents thanks to container coding and labeling and the organised presentation of the boxes on the trolleys.
- No handle holes so that small parts do not fall out and the container height can be fully utilised.
- The ergonomic cup handles are very user friendly.
- A particularly rigid base prevents deflection even with heavy point loads.
- The various departments now work much more efficiently, with clearly noticeable positive effects on process costs.
What our customers say
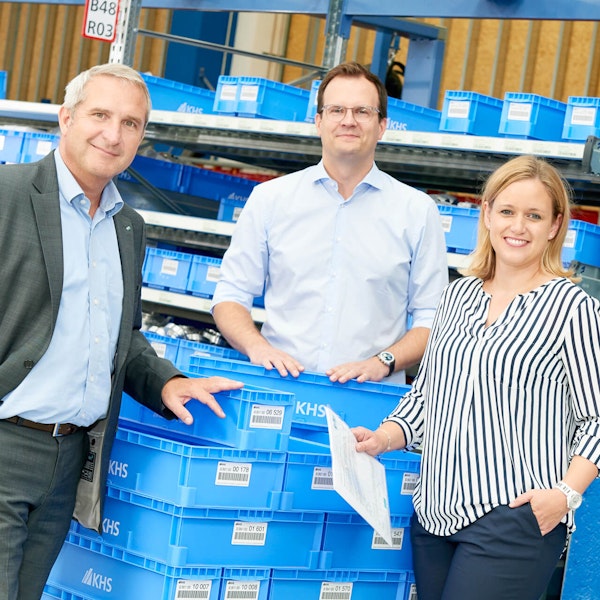
We needed a pool-compatible container suitable for all locations that takes into account all the special features of the KHS range of materials. KHS wanted to optimize their transport and material flow processes with a customised container series and streamline their internal production supply processes in order to reduce process costs. This goal was achieved with the EMB stacking container series from BITO.
Frederic Nitka,Head of Cross-Divisional Management Industrial Engineering, KHS GmbH
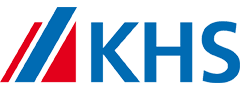