How to recognise good quality plastic containers
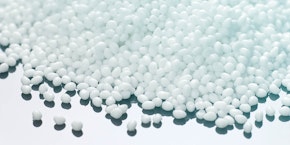
Plastic containers are used for a variety of purposes in intralogistics. Storage and transport of articles, goods, auxiliary materials, hazardous goods and waste are just some of the common applications. (1, 2). They are available in a wide range of sizes – from small parts bins to large containers. Manufactured according to European standards, they can be specially designed for use in automated warehouses, as trays, heavy-duty containers or as nestable, foldable or stackable space-saving containers. Furthermore, they can also be supplied with skids, wheels, feet or lids. Plastic containers can also be designed for specific sectors, such as the pharmaceutical industry, maybe requiring precisely shaped inlays or cold packs, or the food industry where containers have to be food safe.
Given the broad variety of possible applications, plastic containers can contend with very different load conditions – such as being subjected to high loads or the impact of hazardous material. Consequently, containers need to be made of the correct material and meet quality requirements.
The stuff dream containers are made from
Plastic containers for the storage and transport of goods are usually made from polypropylene (PP) or polyethylene (PE). Somewhat more exotic are the more environmentally friendly materials, such as Sunflower Compound (SFC). This is a mixture of plastic and sunflower seed shells, which can sometimes be used for the production of containers. What they all have in common is that they are made from plastic granules. The quality of the plastic granules is therefore extremely important for the long-term quality of the plastic container throughout its life. Key characteristics in the quality of plastic granules and compliance with corresponding standards include impact strength, rigidity and resistance. (3). Granules that have been manufactured and tested in Europe almost always meet these standards.
This is particularly relevant to the logistics industry, where plastic, and other, containers are often exposed to high loads. For this sector, features such as high-quality granules, the right plastic for an application and suitable container design are important because they will contribute to a plastic container having a long life as well as generating a good price/performance ratio that will add to a company’s profitability. They will also offer maximum product safety while minimising the material used in production. Other quality characteristics include the origin of the granules, the composition of the plastic and the ecological footprint (recyclability). The plastic composition has a significant effect on its ecological characteristics.
Despite the many advances in production and processing, not all plastics are suitable for recycling. Therefore, companies should focus on particularly robust plastic containers with a long product life cycle. These will be more efficient for a company in the long term and will also help to attain the goal of sustainability.
Possible quality issues with plastic material
It is essential to dry plastic granules before processing them (4). The moisture of the raw material has a significant influence on process reliability and quality of the product. Many plastic materials are hygroscopic meaning they absorb water into the pellets i.e, into their molecular structure. When it comes to injection moulding, too much moisture can cause a variety of problems during processing, and, in turn, for the end product – such as reduced mechanical strength - a defect that will not be visible. Other effects during processing are vapour bubbles or foam formation, filling and demoulding problems, viscosity fluctuations, scattering process parameters or fluctuating throughputs.
Further into processing, problems can occur during electroplating or painting. Impairments to the material can only be detected using suitable analytical methods. In most cases, this involves destructive testing. In overall terms, excessively moist material can impair the entire range of the properties of moulded parts – not only the mechanical properties but also the optical, chemical and physical properties. Obvious defects are streaks, cavities and holes as well as bubbles on the surface. However, over-drying the granules is also not advisable, because over-dried plastics also cause problems in the processes and will result in the material not meeting requirements.
In addition, design flaws in product or tooling and processing parameters – such as process temperatures and pressures – can translate into inferior product quality that is not detectable or measurable by the naked eye or standard quality control methods. Here, suitable tomographic, microscopic, spectroscopic and thermal analysis methods help further to determine the extent and magnitude of the impairments (5).
Consider quality features when buying a container
First of all, you should only buy storage and transport containers from a recognised storage technology company. These companies guarantee quality (BITO offers a 5-year quality guarantee) and will be happy to advise on specific applications. Furthermore, the quality management of these companies will be certified according to ISO 9001.
High quality plastic containers will offer guarantees relating to their quality, type of plastic used, their recyclability, load capacity, whether they are food-safe or are able to reduce static electricity due to their ESD (electrostatic discharge) characteristics. Containers for the food industry must be certified for food-safety (declaration of conformity). Pharmaceutical transport or vaccine containers must also comply with certification guidelines (6). Containers used to carry dangerous goods must be tested to demonstrate that they meet minimum UN performance standards set by the regulations. (7)
Storage containers must, of course, not have any damage or even have visible flaws (streaks, holes, bubbles, etc., see above) to the plastic when purchased. BITO plastic containers are tested under the toughest conditions during development.
How does BITO ensure these quality features?
BITO ensures the quality of its containers, as well as its shelving for holding containers, by producing them in the company’s own facilities using the latest technology. This places the quality management and control of the processes and products in BITO’s own hands, ensuring that all requirements for the quality characteristics of BITO containers, shelving and other products are met. BITO's goal is always to develop, manufacture and market the best products for its customers. Development and production are subject to the strictest quality criteria and follow the ISO 9001 quality standard. BITO uses only the best starting products, semi-finished products, materials and granules. Of course, the company applies all the necessary testing procedures (see above) to ensure the quality of its products. If you would like to know more, please contact BITO via contact form, e-mail or telephone.
Literature:
1 BITO Expertise, Which storage container suits you?, Link
2 Container systems, BITO storage technology, Link
3 BITO expertise, Quality standards for plastic granulate - because plastic is not just plastic, Link
4 Why should plastic granulate be dried? Mo's Corner, Link
5 Dahlmann Prof. Dr. rer. nat. R., Evaluation of product quality, We evaluate the quality of plastic products, Institute for Plastics Processing, RWTH Achen, Link
6 Vaccine transport on the last mile, BITO supplies reusable containers, Packreport, dfv Mediengruppe, Link
7 UK Government Guidance ‘Packaging of dangerous goods for carriage' Link