Sustainability
Sustainable production
- Environmentally friendly selection of quality raw materials and auxiliaries
- Energy-efficient machinery
- Resource-saving production processes

Our quality is sustainable – as are our processes
We also make sure to save energy and hence CO₂ emissions during the production of our products. We have been investing in the modernisation of our energy supply systems and manufacturing facilities for many years to reduce our energy consumption and CO₂ emissions.
BITO shelving and racking systems are manufactured in our plant at Meisenheim using energy-efficient state-of-the-art technology. Profile forming and shelf production are carried out with the latest edging, punching and bending machines. This is complemented by the high degree of automation, which ensures dimensional accuracy and consistent quality.
The production plant for plastic bins and containers in Lauterecken is one of the most modern in the industry and was expanded by another production hall in 2018. At this site, our bins and containers are manufactured on high-performance, state-of-the-art, energy-efficient injection molding machines of the latest generation. In addition, we can adapt bins and containers to customer-specific requirements in a large finishing center.
Resource-saving, energy-efficient approach
When selecting our raw materials and auxiliaries, we always opt for materials that are not harmful to health and that allow environmentally friendly processing. In the pursuit of sustainability our products are manufactured using resource-saving, energy-efficient procedures to minimize any negative impact on the environment while conserving raw materials. We give preference to manufacturers and suppliers who comply with ecological standards. In addition, priority is given to transport routes that are as short as possible.
Energy efficiency is not only a top priority in our production plants. Buildings and products also have a carbon footprint. By using modern lighting and plumbing technologies, we are also saving resources in our offices and workshops. Modern manufacturing technologies, thermal insulation building materials and a sustainable energy concept help us reduce our CO₂ footprint.
In 2019, a new, additional production site in Poland went into operation in order to meet the constantly increasing demand in Eastern Europe, to ease the workload in our production plants in Germany and to shorten shipping routes.
Facts at a glance
Improving energy efficiency
- By contracting another energy supplier who operates with a significantly higher share of renewable energies in their electricity portfolio, we were able to reduce CO₂ emissions by 40% in 2020 compared to 2018. Basically, switching to green energy already saves about 2,800 tonnes of CO₂.
- In 2006, we commissioned our first photovoltaic system to generate our own renewable electricity. In the recent past, two additional photovoltaic systems were put in operation, so that we are now generating more than 1 million kWh/a of "green" electricity.
- By exchanging all conventional lighting sources in our offices and plants against modern LED technology, we were able to reduce our energy consumption by 60%, thereby saving approximately 700,000 kWh/a.
- In our plant in Lauterecken we have equipped the latest generation of our injection moulding machines with eco-drives. Their specific energy consumption (SEC) for processing one kilogram of polymer is 12-20% lower compared to conventional machines: 20% for the 1,500 ton machine, 12% for the 2,700 ton machine.
- We are also planning to invest in a new powder coating facility to replace the existing installation we have been using for many years. This new facility works with up to 40% less energy.
Water and heating energy
- By switching to a closed-loop water system and by installing free coolers instead of cooling towers, we were able to reduce our water consumption by 60 %.
- In addition, all pumps in our cold water systems needed for injection moulding and the pumps in our heating circuits have been modernised in order to save energy in this field as well.
Reducing carbon emissions
- Particular attention is given to exhaust-free production processes, in the metal forming as well as in the injection moulding process.
- The (energy-intensive) generation of compressed air has also been optimised. Air compressors shut off automatically after pressure has reached a certain level, which results in a 10% reduction of energy consumption and CO₂ emissions.
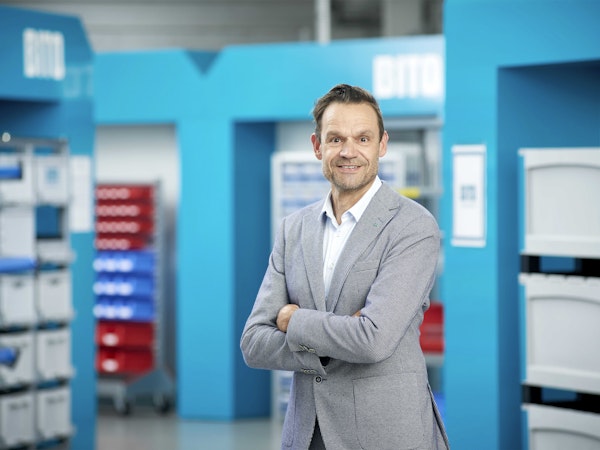
"The ability to change means constantly questioning what you are currently doing and having the courage and verve to permanently improve yourself. This ability is key in order to adapt to the different requirements in the project and solution business.”
Dominik Freyland-Mahling
Director of Production Management at BITO-Lagertechnik