Our customer
The Hammer Group is a merger of logistics companies based in Aachen. The group has a fleet of 300 vehicles, employs 700 people and generates an annual turnover of EUR 135 million. The company is a forwarding company in the classic sense providing custom solutions in the field of freight forwarding as well as a range of logistics services ranging from individual aspects of the supply chain to offering full end-to-end solutions to businesses to optimise their supply chain operations. Based on traditional values and cutting-edge technologies, the company has scaled up their service portfolio throughout the supply chain and is now a global player.
Logistics Services Provider Hammer GmbH & Co. KG, which belongs to the Hammer Group, set up a new logistics centre in Bedburg near Cologne in 2015. The 103,000 sqm distribution centre houses a shuttle-serviced automated storage and retrieval system (ASRS) providing small parts primarily a large DIY chain.
Customer requirements
- The logistics services provider needed approximately 60,000 boxes for an automated small parts warehouse.
- The boxes had to be very sturdy and suitable for automated systems.
- Noise development in the automated warehouse was to be minimised in order to create a more pleasant, less stressful work environment. Accordingly, the new bins were to run as quietly as possible on the powered conveyor system.
- The company needs to store small parts.
- A large number of different reference items must be picked efficiently.
- The boxes must have the largest possible internal volume in order to store a maximum of small parts.
- The space in the existing racking installation was to be used as efficiently as possible with the new containers fitting in perfectly.
The BITO Solution
Low-noise BITO XLmotion containers
» BITO supplied 60,000 XLmotion plastic containers suited for use in automated warehouses.
Especially quiet operation
» The new base design of XLmotion containers keeps travelling noise to an absolute minimum. The smooth framework and an absolutely even container base minimise friction when passing over conveyor belts, which significantly reduces conveying noise.
Sturdy sandwich base
» The base is bonded to the container with diagonal support ribbing. The sandwich construction prevents the base from deflecting under high loads.
Large internal volume
» The box measures 600 x 400 x 320 mm and has an internal volume of 53 litres.
Wide container base
» The XLmotion base is 25 mm wider than the base of conventional European size stacking containers.
High load capacity
» XLmotion containers can load up to 50 kg and have a stacking load of 250 kg.
Side-to-side and front-to-back dividers for small parts storage
» The boxes can be subdivided with sturdy yet thin-walled dividers.
Ergonomic handling
» There are grip holes on the short side for ergonomic handling.
Barcode application
» The containers can labelled with barcodes that can be recorded and stored by the WMS.
XLmotion containers are eco-friendly
» BITO low-noise XLmotion containers are made from 100% recycled plastics.
On-site application
- BITO XLmotion containers are used in the small parts warehouse. The warehouse operates with a double AS/RS shuttle system.
- The small parts are stored in high-bay racking. As soon as stocks in the AS/RS system fall below the system's minimum stock level, the system generates a replenishment order from the high-bay racking. Staff then pick the small parts orders from cardboard boxes into the XLmotion containers which are transported on conveyors to the AS/RS facility.
- The facility consists of five aisles of 20 levels each served by a shuttle carrier. The XLmotion containers are loaded from both sides in randomised storage mode at any empty storage position.
- The containers almost always remain in the system circuit.
- To store different reference items in one container, the containers are subdivided with side-to-side dividers into ¼ sections.
Customer benefits
- XLmotion containers are extremely quiet on conveyors. Significantly lower noise levels reduce stress levels for employees.
- Quieter operations create a more pleasant work atmosphere, resulting in greater job satisfaction and fewer stress-related absences.
- Fewer mistakes are made as a result of a noise- and stress-reduced work environment.
- Thanks to their excellent stability, XLmotion containers can cope with rough handling and high loads.
- The particularly large net volume of XLmotion containers means that more goods can be stored.
- Keeping more reference items in the same container reduces the number of replenishment operations.
- The higher filling degree of each XLmotion container ensures that fewer containers are needed to handle the same quantity of goods. As a result, fewer containers have to be moved, which in turn makes the entire system more efficient.
- Due to the wider container base, automated storage installations can be built with narrower seat profiles. This saves a lot of construction material, thereby minimising plant construction costs.
What our customers say
Thanks to the quiet operation of XLmotion containers, working in a small parts warehouse is much less stressful. We get very good feedback from our staff and everyone likes their job. The pleasant environment even encourages employees from other departments to apply for jobs in the automated storage area. The quiet operation of the containers also helps improve concentration and reduces the error rate.
Lutz Harde,
Managing director of the Hammer GmbH logistics centre
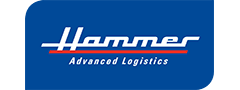