The importance of rack inspections for workplace safety
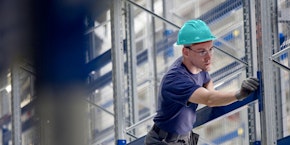
The heart of a warehouse is a well-coordinated storage and picking system. This includes all the technical systems and equipment in a warehouse as well as all the means necessary to organise the warehouse. In addition to the employees, the order-picking system, forklifts and containers, it is primarily the racking systems, conveyors and electrical equipment that make up a well-functioning system. In turn, the racking, being the central component of the overall system, must be continuously checked and maintained in a first-class condition. Regular rack inspections serve this purpose.
Rack inspections are required to comply with health and safety in the workplace
Employers have a moral and a legal duty to ensure that conditions and equipment in the workplace are safe and regularly checked to be safe - rack inspections are integral to that requirement.
The frequency of inspections will depend on the size and complexity of an installation as well as the level of operating activity in the location. However, visual checks should be done weekly and a technically competent person should carry out inspections at intervals of not more than 12 months. Someone needs to be nominated as a PRRS (Person Responsible for Racking Safety) and they will determine the required frequency of inspection. Each inspection then requires a written report to be submitted to them with observations and proposals for any action necessary.
Why rack inspections are so important
Besides the fundamental requirement to ensure the workplace is safe for employees, many other reasons exist for a racking inspection to be carried out. One of the reasons is to maintain the level of service. This is the degree to which a company is ready or able to deliver items. Service level is a metric that indicates the likelihood of having enough stock to meet demand. Functioning and damage-free racking is necessary to ensure a company's continuous ability to deliver. In other words, if racking fails due to damage or accidents, the company's ability to deliver is at stake.
Of course, it is not only the ability to deliver that is at stake, but actually also the lives of the employees. Collision damage can cause racking to collapse and seriously injure or even kill employees.
The Health and Safety Executive (HSE) (1) guidelines are very clear as to why rack inspections are important - „In general, racking is manufactured from relatively lightweight materials and, as a consequence, there is a limit to the amount of abuse that it can withstand. The skill of lift truck operators has a great bearing on the amount of damage likely to be caused. Any damage to racking will reduce its load carrying capacity. The greater the damage the less its strength will be.“
As well as causing health & safety concerns, impact damage to racking can be expensive to repair and cause unnecessary disruption to a company’s operation. There are products and advice to limit the potential problems due to racking damage (2).
What type of racking needs to be inspected?
Racking is considered a fundamental component of a workplace environment and, as such, can cause injury or accidents to employees if not correctly mantained.There is a high risk of damage to static racking caused by unguided forklift trucks when loading or unloading pallets. Therefore, pallet racking, cantilever racking, drive-in and drive-through racking, flow racking and multi-tier racking systems must be regularly subjected to a racking inspection. Shelving systems that are manually loaded and unloaded require a risk assessment to be carried out to identify the likelihood of exposure to potential damage by industrial equipment. The results of that risk assessment will determine whether the shelving could be damaged and thereby determine the level of inspection required to protect employees‘ safety.
What exactly is being tested?
Any inspection is important but there is a distinction between a detailed, rigorous inspection by a qualified technically competent person, which must be carried out at least once every twelve months, and a visual inspection at weekly or a risk-dependent time interval based on a risk analysis. Nevertheless, the weekly visual inspection should be carried out by individuals who have received the relevant training to identify potential problems..
For thoroughness, it is recommended to use a checklist for inspections to ensure nothing is missed. Examples of possible problems to identify are incorrect installation, overloaded locations, missing load notices, dented uprights or beams, cracks in welds or damaged floors.
A written log needs to be kept of each inspection along with any required remedial actions. Observed issues are divided into three colour coded danger levels: green (damage to be observed by the PRRS), amber (action required as soon as possible), red (serious problem requiring the racking to be immediately offloaded and isolated).
What actions should be taken in the event of damage?
Any damage detected during a racking inspection must be reported to the company's safety officer and professionally repaired as soon as possible. The damage must be described in a written report and kept for future reference. Should damage recur over a period of time, an investigation into the cause should be carried out to understand the likely cause and identify remedial action.
The HSE colour coded classification of damages and required actions is shown below:
Risk Level: Green
Requiring surveillance only - Green level indicates the limit that does not require a reduction in rack carrying capacity or an immediate repair of the system. This would indicate racking components that are considered to be safe and serviceable. Such components should be recorded as suitable for further service until the next management inspection but should be clearly identified for specific re-examination and reassessment at future inspections.
Exceeding the green level should be considered damage and causes risk to the racking system.
Risk Level: Amber risk
Hazardous damage requiring action as soon as possible - This would identify an area where the damage was sufficiently severe to warrant remedial work but not so severe as to warrant the immediate offloading of the rack. Once load is removed from a damaged component, the component should not be reloaded until repairs have been carried out. The user should have a method of isolating such racks to ensure that they do not come back into use until the necessary repairs have been carried out and the equipment certified as safe. For example, use dated adhesive labels, which indicate racks that are not to be reloaded until rectified. Any racking with amber risk category damage should be redesignated red risk if remedial work has not been carried out within four weeks of the original designation.
Risk Level: Red risk
Very serious damage requiring immediate action - These are situations where a critical level of damage is identified which warrants an area of racking being immediately offloaded and isolated from future use until repair work is carried out. Such repair work would usually be by replacement of the damaged component. You should have a method of isolating areas to ensure that they do not come back into use before the repair work is carried out. For example, a particular bay could be offloaded in the presence of the inspector and roped off to prevent further use.
In order not to compromise safety, repairs and replacements to racking systems should always be carried out by trained personnel with original components. If this is not possible, a proof of stability must be provided and documented.