Spare parts logistics in the automotive industry
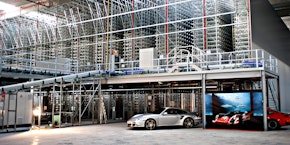
It is not without reason that spare parts logistics in the automotive industry is called the supreme discipline of logistics. After all, spare parts for many different car models - even for classic cars - with several thousand parts each must be available nationwide or even worldwide. The spare parts assortment consists of fast-moving items up to parts that are only very rarely needed (extremely slow-moving items). The task of logistics is therefore time-critical and extremely complex. The objectives of spare parts logistics are to optimize costs, service and inventory while maximizing availability and reliability. There is a conflict of objectives between sufficient stock levels with the lowest possible capital commitment and adequate parts availability. In the meantime, the carbon footprint has also become the focus of distribution planning.
Warehousing in spare parts logistics
In the automotive industry, sophisticated and tailor-made solutions for warehousing and distribution as well as a differentiated and realistic determination of the demand for spare parts are required. The companies' distribution system is structured on several levels and is divided into a central, regional and dealer level. In this way, it is possible to react to customer orders at different speeds. In this logistics network, the slow-moving items are stored centrally and the fast-moving items with continuous demand are stored locally close to the place of demand. The central warehouse stock does not have to be physically located at a central location. Usually, slow-moving items are moved to low-cost external warehouses that supply the central warehouse location when required. Physical separation according to part size and part type in the warehouse is also common (for example, large, medium and small parts). The company's stocks are managed centrally using IT technology and therefore form a virtual central warehouse. In order to achieve stock transparency over the entire logistics chain of spare parts logistics, all stocks from the central and regional warehouse to the dealer's warehouse must be linked and visualized using IT technology. (1) Various electronic components, for example, can only be stored to a limited extent. There is, so to speak, an expiry date that must be taken into account in storage and logistics.
Customer loyalty and efficiency increase
Today, spare parts no longer sell themselves through dependence on the car manufacturer or dealer. Nowadays, the customer tries to get spare parts cheaper from external suppliers via the Internet. In the OEM sector (Original Equipment Manufacturer) of the automotive industry, a relentless competition has developed. Some car manufacturers - such as FIAT - have therefore set up local distribution centres to ensure that dealers are supplied with spare parts more quickly and efficiently. In addition, better transparency is to be established for parts availability. Dealers also want to reduce their stock levels and therefore fast delivery in spare parts logistics - preferably Same Day Delivery - is necessary. In general, the focus of spare parts logistics with a high potential for increasing efficiency is on identifying required spare parts, triggering the ordering process and minimizing the delivery time.
3D printing as a future trend
Instead of sending components from a regional or central warehouse on what can sometimes be a journey of thousands of kilometers, spare parts can be printed out quickly on site using so-called 3D printing. Laser sintering, for example - a technique used in additive manufacturing - is used here. A prerequisite is that the three-dimensional CAD data of the components exist and can be transferred to the corresponding 3D printer. Additive Manufacturing (AM) has gradually evolved from ‘Rapid Prototyping’ over the last decades. In ‘Rapid Prototyping, however, mainly plastics were used, whereas AM uses many different materials (including precious metals, titanium, complex alloys, etc.). The advantage is that spare parts for products at the end of their life cycle can also be produced. AM is particularly suitable for the individual production of components or spare parts. A costly storage of many spare parts could be avoided by the technology. Furthermore the downtimes of affected vehicles would be minimized. A further possibility of laser sintering is the repair of components (Rapid Repair), which therefore would not have to be replaced completely. 3D printing and AM are on the advance and will probably replace costly storage and distribution in spare parts logistics in a few years.
Storage technology for spare parts logistics
Warehouses for spare parts logistics in the automotive industry must offer a wide range of storage options for the most diverse parts. One thinks of
Large parts of engines and car bodies, car windows, tyres, small parts or sensitive electronics. There is appropriate storage technology for these very different stored goods. A car spare parts warehouse must be functional and clearly arranged and guarantee smooth operating processes. Combined solutions are often used here. These include, for example, automated storage and retrieval systems (ASRS) for fast-moving items, multi-storey shelf systems (MGA) for slow-moving items and pallet warehouses for the replenishment of whole pallets (pallets for single articles). Barrel rack storage systems for the storage of oils, brake fluids and other hazardous substances are also usually required for these warehouses. In general, they are subject to high requirements.
Volume reducible reusable plastic containers (180 degree stack & nest containers, nestable containers or collapsible containers) are also frequently worthwhile in spare parts logistics. These are used for transport from the central warehouse to the local distribution centres or directly to the car dealers and then back to the central warehouse. BITO's product range includes the U-Turn, DSL and DST 180 degree stack and nest containers, nestable space saving containers (such as the reusable container MB), folding boxes EQ, reusable folding boxes MFB and pallet folding boxes.