Zuverlässigkeit in Stein gemeißelt
J. König setzt im neuen Logistikzentrum auf Regal- und Behältersysteme von Bito
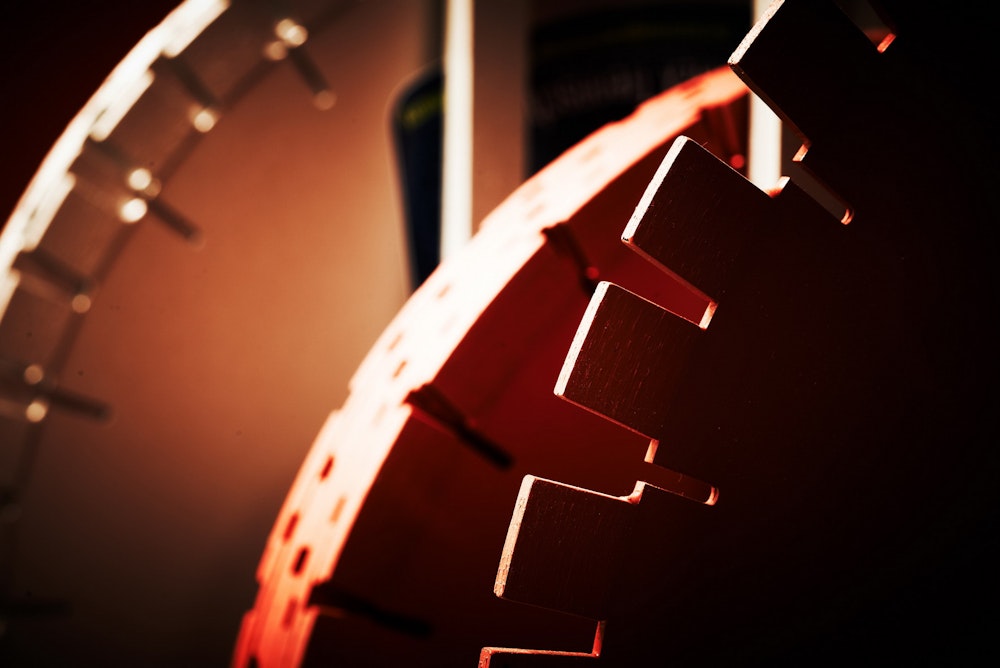
Um das Unternehmen für die weitere Expansion vorzubereiten, hat die Karlsruher J. König GmbH ein neues Logistikzentrum errichtet. Hier lagert und vertreibt der Familienbetrieb seine Werkzeuge für den Steinindustrie- und Handwerkerbedarf. Das Besondere an dem Portfolio ist seine Vielfalt. Diese reicht vom kleinen Steinbohrer über Winkelschleifer bis hin zu großen und sperrigen Transportgestellen. Um das neue Logistikzentrum mit der passenden Lagertechnik auszustatten, setzt J. König auf Kompetenz und Lösungen von Bito aus Meisenheim. Der Komplettanbieter lieferte und installierte aber nicht nur die Regalanlagen und Behälter, sondern brachte auch umfangreiches Know-how mit ein. Entscheidend war insbesondere die zeitkritische Umsetzung. Dabei konnte Bito während des Projektverlaufs flexibel auf Änderungen eingehen.
Schrifteisen, Schleifmittel, Diamanttrennscheiben, Polymerkleber sowie eine breite Palette an Kompressoren und Druckluft-Werkzeugen – bei Natursteinverarbeitern, Steinmetzen, Bildhauern und Restauratoren besitzen die technisch ausgefeilten Lösungen der J. König GmbH in Karlsruhe-Durlach den besten Ruf. Hier im Industriegebiet Killisfeld sitzt die Firmenzentrale des Familienbetriebs, der in den eigenen Werkstätten den Bedarf für Steinindustrie und Handwerker herstellt. Knapp 500 Meter weiter, auf einem etwa 18.000 Quadratmeter großen Grundstück, steht seit Anfang 2014 in moderner Schieferfassade das neue Logistikzentrum. Im Gebäude hat der Betrieb zudem den neuen Profimarkt sowie ein Test- und Schulungszentrum eingerichtet. „Wir wollen auf jeden Fall weiter wachsen“, begründet Daniel Petri, Geschäftsführer der J. König GmbH, die Investition. „Vorher befand sich das Lager in der Firmenzentrale. Doch die Kapazitäten waren erschöpft und improvisieren konnten wir nicht mehr.“ Daher hat das Unternehmen das neue Logistikzentrum mit einer Nutzfläche von 4.400 Quadratmetern errichtet. Am alten Firmensitz bleiben nach Petris Angaben bis auf weiteres die Verwaltung und die Werkzeugproduktion.
Von der Trennscheibe bis zum kleinen Steinbohrer
„Wir lagern hier rund 8.500 Produkte“, sagt Geschäftsführer Petri. Er läuft an den Regalreihen vorbei und zeigt auf die Waren, die auf Paletten oder in Behältern gelagert sind. Auffallend, wie sie sich erheblich voneinander unterscheiden. „Wir haben hier zum Beispiel eine Diamanttrennscheibe, mit einem Durchmesser von 600 Millimeter, die genauso effizient gelagert sein muss wie ein Steinbohrer, der sieben Zentimeter klein sein kann.“ Diese enorme Vielfalt musste sich auch in der Lagerlösung wiederfinden. An diese waren weitere hohe Anforderungen gestellt: Sie sollte den Raum optimal nutzen. Und damit die Waren in kürzester Zeit zu den Händlern, direkt zu den Endkunden oder je nach Produkt zur Weiterverarbeitung zurück in die Fertigung gelangen, muss sie zudem einen schnellen und reibungslosen Materialfluss ermöglichen.
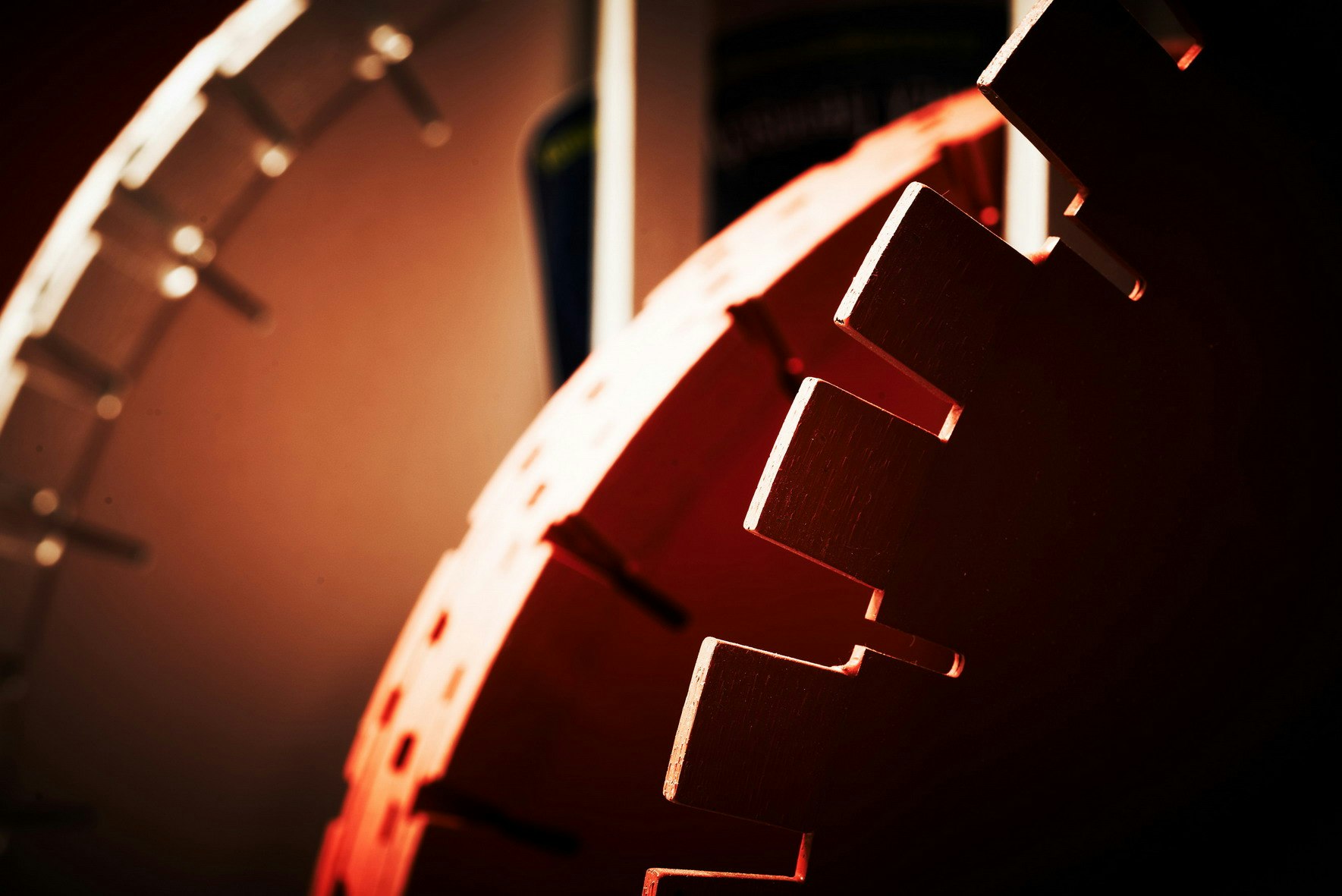
Aus einer Hand: Von der Planung bis zur Umsetzung
Im März 2013 wurde der Grundstein gelegt, Ende des Jahres sollte das Distributionszentrum bezugsfertig sein – ein straffer Zeitplan. „Mehrere Logistikanbieter bewarben sich für das Projekt“, berichtet Elmar Dreikluft, der als Projektleiter bei J. König verantwortlich war. Den Zuschlag bekam schließlich die Bito-Lagertechnik aus dem rheinland-pfälzischen Meisenheim. „Wir hatten vorher schon Regallösungen von Bito im Einsatz und waren damit sehr zufrieden“, resümiert er. Mit dem Komplettanbieter zusammenzuarbeiten heißt für ihn, einen Partner von der Planung bis zur Umsetzung zu haben, der außerdem alles aus einer Hand bietet.
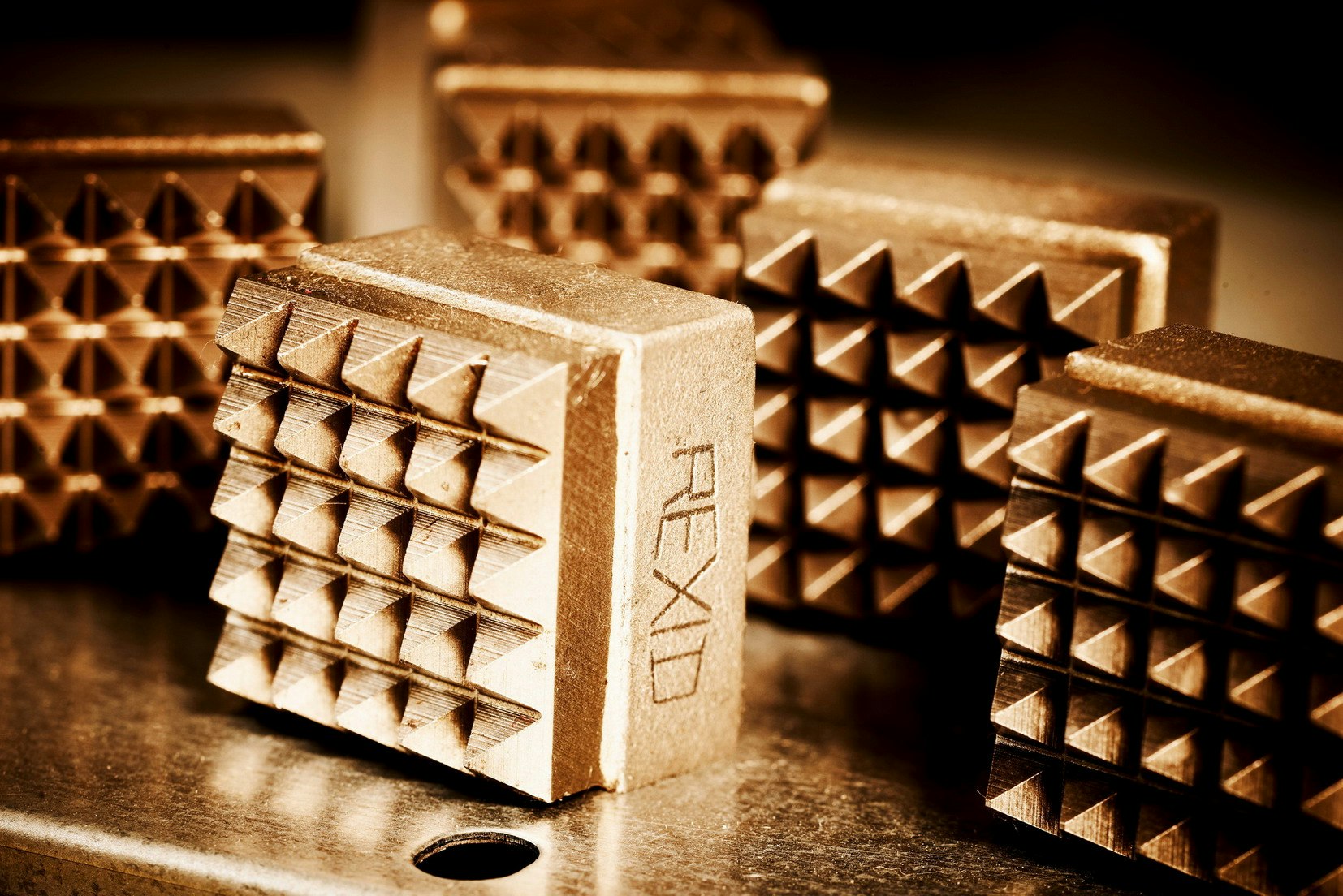
Gemeinsam mit den Verantwortlichen der J. König GmbH entwickelte Bito ein Konzept, das einen optimalen Fluss der Waren sicherstellt und eine effiziente Lagerhaltung ermöglicht. „Bei der Planung haben wir nicht nur den Platz, der uns zur Verfügung stand, optimal genutzt. Wir haben auch Wachstumsprognosen berücksichtigt. Die Anlage könnte in einem nächsten Schritt aufgestockt und die eingesetzten Regale modifiziert werden, um eine erhöhte Umschlagsleistung abzufangen“, sagt Bito-Gebietsverkaufsleiter Harald Fessler. Die komplette Intralogistik besteht aus einer Palettenregalanlage sowie Steckregalen mit aufgesetzter Bühne. Teile der Palettenregalanlage wurden zudem mit Durchlaufrahmen ausgestattet. Dazu kamen verschieden Typen von Bitoboxen wie Eurostapelbehälter, Regalkästen und Sichtlagerkästen.
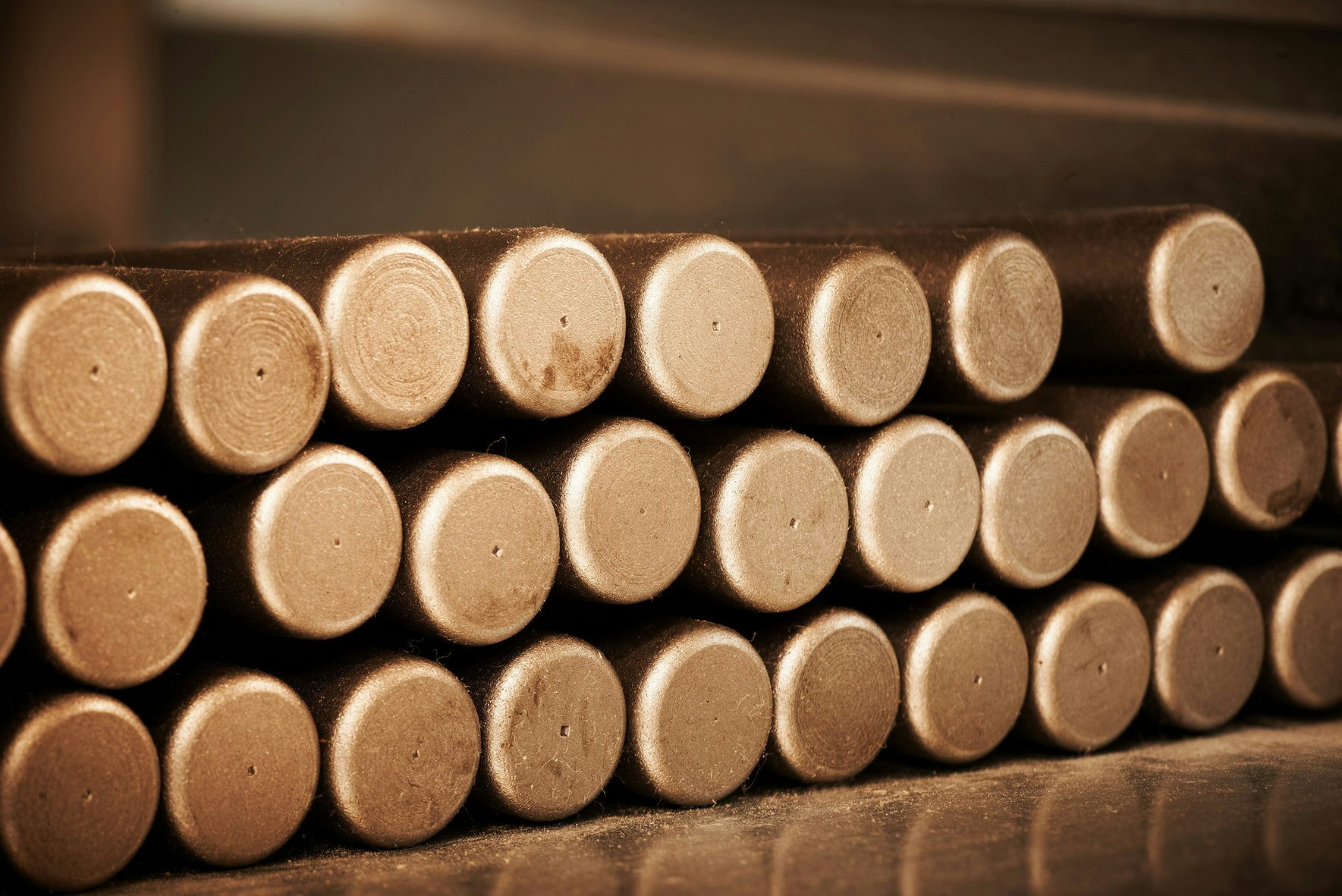
Flexible Regallösung
Weil die meisten Produkte auf Europaletten gelagert werden, installierte Bito eine Palettenregalanlage von Typ PRO. Mit diesem System ist jeder Ladungsträger für die Mitarbeiter leicht zugänglich. Außerdem ist der Anwender damit äußerst flexibel. Er kann jederzeit die Regalaufteilung verändern und bei Bedarf zum Beispiel Fachhöhen anpassen, um neue Einlagerungsebenen einzufügen. „Für jede Belastung können wir mit dem Stützen- und Traversen-System der PRO-Familie die Regalsysteme anforderungsgerecht und wirtschaftlich konfigurieren“, beschreibt Harald Fessler. Die Paletten sind jeweils längs eingelagert, vier bis sechs Paletten übereinander, drei nebeneinander.
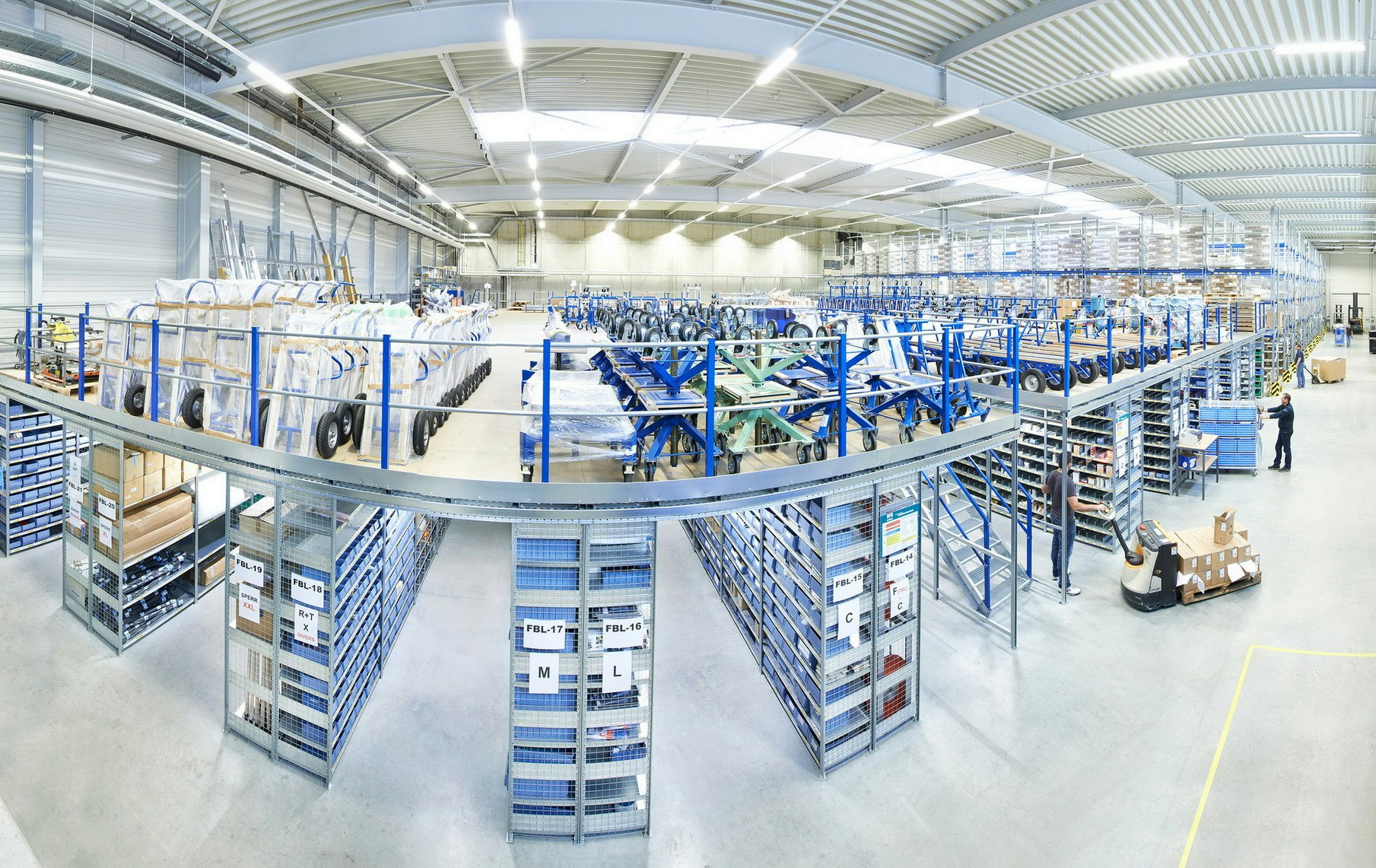
Bito installierte acht Einfachregalreihen mit einer Gesamtbreite von je rund 31 Metern. Jede Reihe besitzt elf Felder mit einer lichten Weite von 2,7 Metern. Dazu kommen fünf weitere Einfachregalreihen mit Längen von rund 22,5, fünf und 15 Metern. Die untersten Paletten stehen jeweils auf dem Boden. Beladen wird eine Palette mit einer maximalen Höhe von 1,1 bis 1,6 Metern und einem Gewicht bis 400 Kilogramm. Die Höhe der Stützrahmen beträgt 7,5 Meter, die Feldlast bis zu 6.000 Kilogramm. Insgesamt stehen J. König mit dieser Anlage 1.656 Stellplätze für Europaletten zur Verfügung. Jeder Stellplatz ist mit einer Nummer versehen. Um die Mitarbeiter in den Gängen vor möglichem herabfallendem Lagergut zu schützen, lieferte Bito für die Palettenregalanlage verzinkte Rückwandgitter.
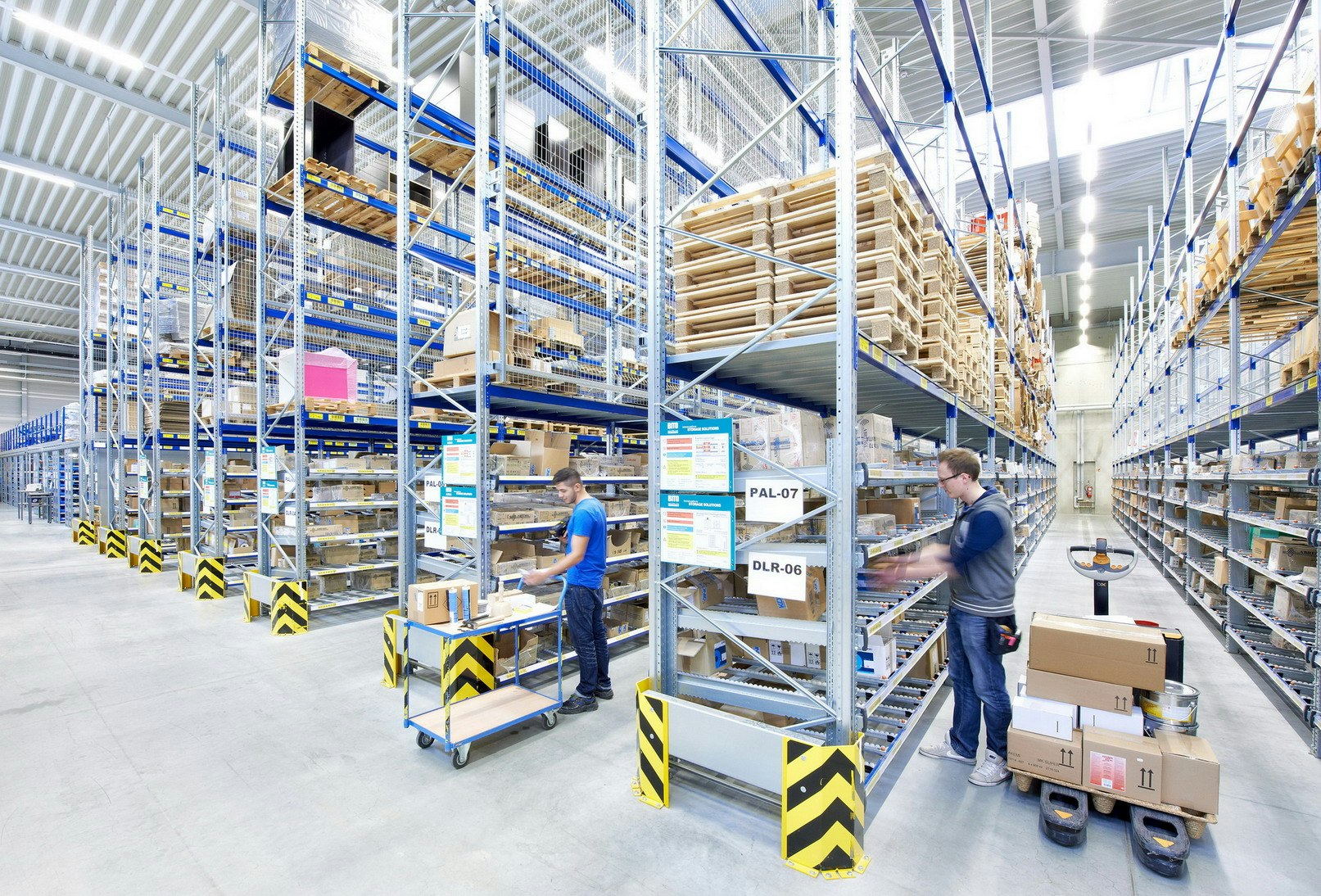
Für einen optimalen Durchlauf gesorgt
Für die sogenannten Schnelldreher-Artikel hat Bito ein Stückgut-Durchlaufregalsystem (SDS) realisiert. „Dazu haben wir Teile der unteren Reihen der Palettenregalanlage mit Durchlaufrahmen ausgestattet“, sagt Harald Fessler. „Mit diesem Durchlaufsystem können wir das Fifo-Prinzip (First In – First Out) einfach umsetzen.“ Eingelagert sind Kartons und Bitoboxen mit rollfähigen Bodenflächen. Jeder Durchlaufrahmen kann eine Last von 360 Kilogramm aufnehmen. Es befinden sich in jedem der betroffenen Palettenregalfelder fünf Ebenen übereinander mit je sechs Kanäle nebeneinander, insgesamt also 30 Kanäle pro Feld. Die Anlage bietet somit Platz für 2.640 Kanäle. „Innerhalb der Kanäle können wir unterschiedliche Gebindegrößen bereitstellen“, beschreibt der Bito-Gebietsverkaufsleiter. „Eine Herausforderung stellten zwei Hallensäulen dar. „Wir haben an diesen Stellen pro Durchlaufrahmen je einen Unterzug und zwei Trennleisten zusätzlich berücksichtigt. Das war Maßarbeit“, ist Fessler von seinen Bito-Kollegen begeistert. Auch mit der SDS-Lösung ist der Betreiber flexibel. Denn er kann die Durchlaufkanäle nach Belieben selbst einrichten und durch die schraubenlose Verstellbarkeit der Rollen- und Trennleisten die Durchlaufrahmen an das Lagergut anpassen.
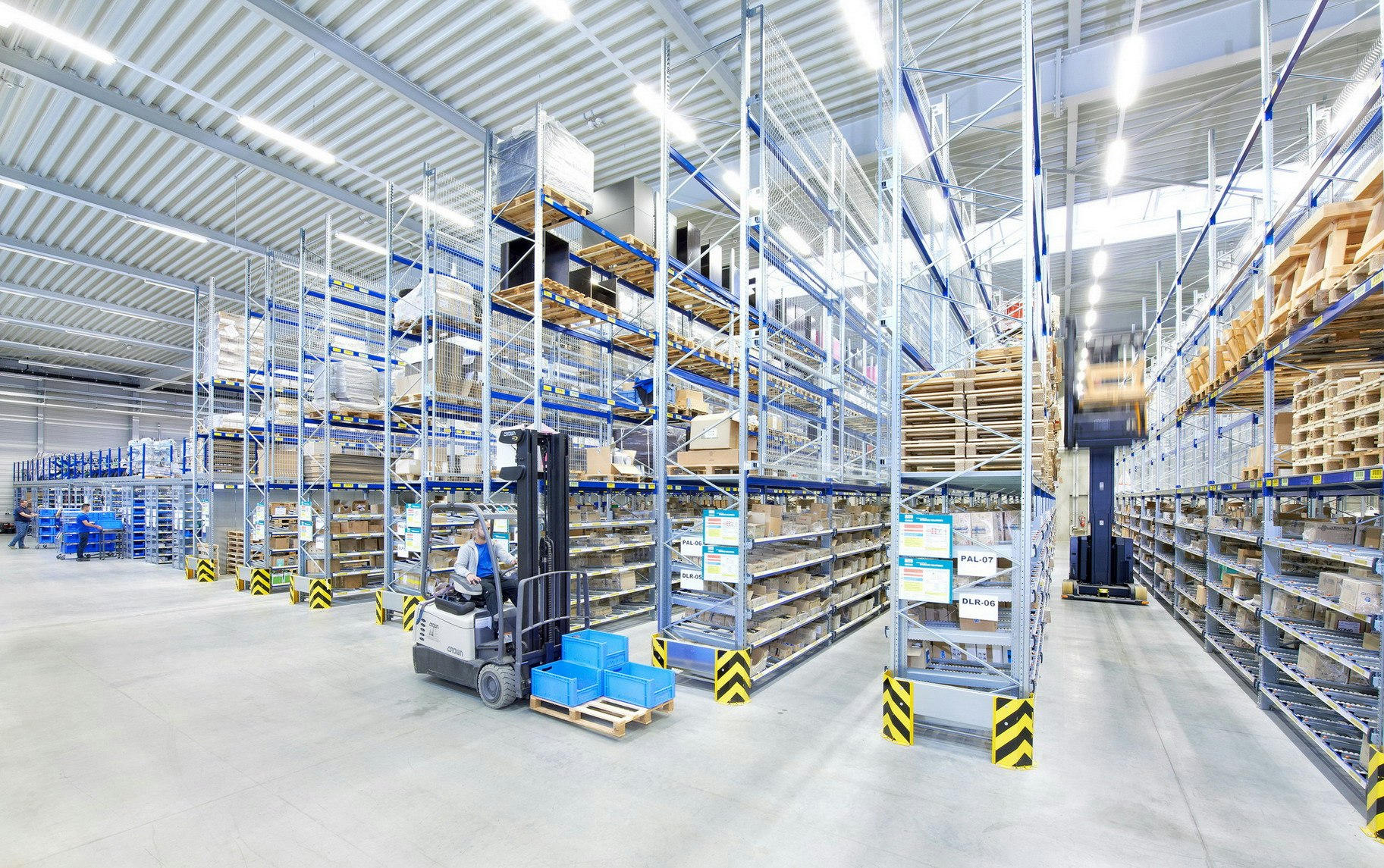
Der große Vorteil des SDS ist Trennung von Kommissionierung und Bestückung. Auf diese Weise kann ein kontinuierlicher Nachschub der Artikel über einen separaten Gang mit einem Schmalgangstapler erfolgen. Davon ungestört kommissionieren die Mitarbeiter an der Entnahmeseite die Aufträge. „Die strikte Trennung der Bediengänge erhöht die Effizienz“, hat Geschäftsführer Petri die Erfahrung gemacht. „Zudem wird durch die kompakte Bauweise der vorhandene Raum optimal ausgenutzt“, wirft Harald Fessler ein.
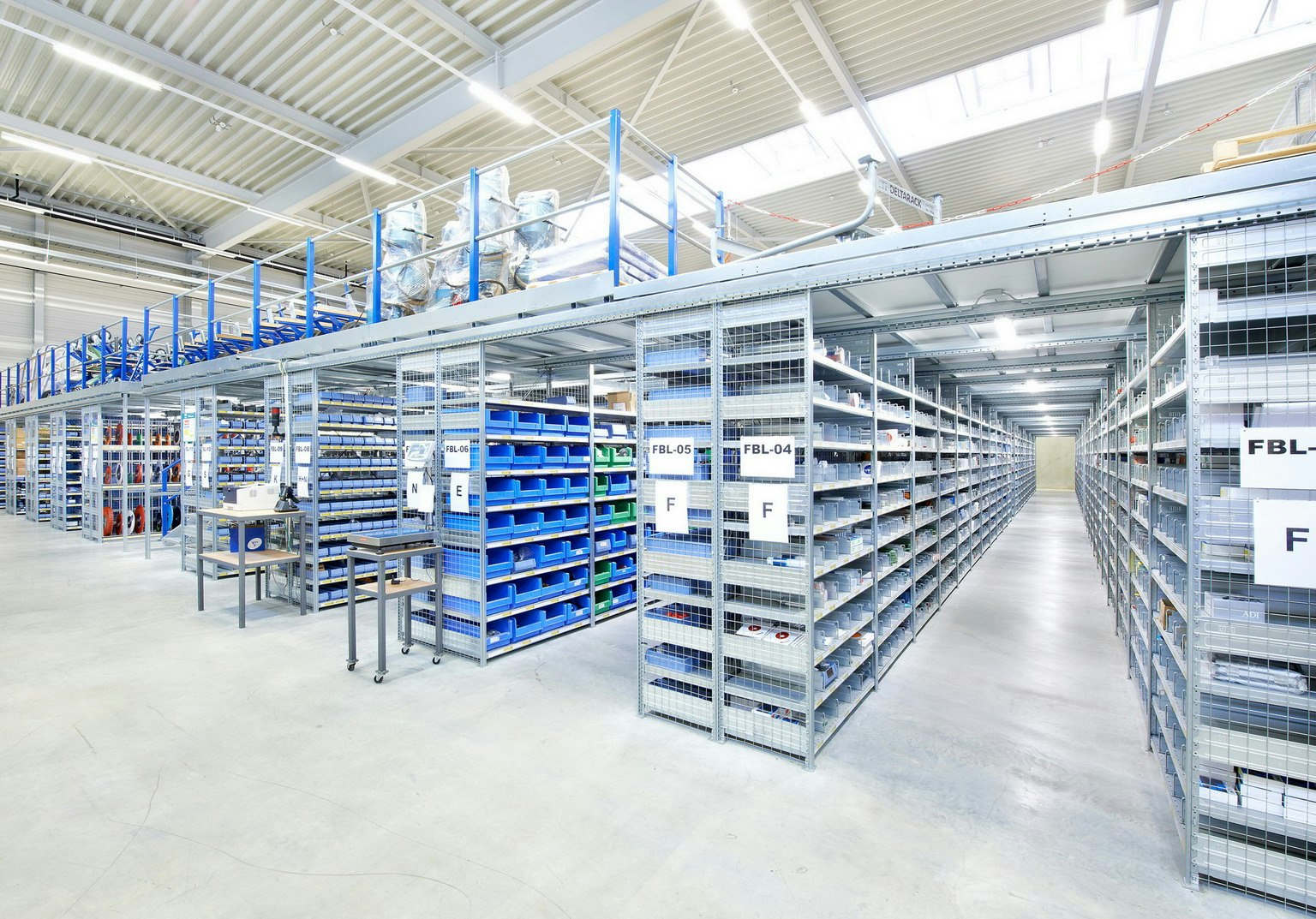
Lagern auf zwei Etagen
Bito hat im neuen Distributionszentrum zudem eine Regallösung mit aufgesetzter Bühne realisiert. Im Erdgeschoss befinden sich insgesamt 478 Fachbodenregalfelder mit je zwei bis zehn Stahlfachböden in unterschiedlichen Tiefen. Bei gleichmäßig verteilter Last kann jeder Boden eine Fachlast von 200 Kilogramm aufnehmen. Die maximale Feldlast beträgt 1.600 Kilogramm. Bito setzte Aussteifungstraversen und Diagonalverbände ein. Dadurch lässt sich die hohe Tragfähigkeit und Standsicherheit aller Regalfelder erreichen. Die Höhe der Stützenrahmen beträgt 2,5 Meter, die Stützlast maximal 15,6 Kilonewton. Die aufgesetzte Bühne hat eine Grundfläche von 800 Quadratmetern und die Bühnenbelastung beträgt 350 Kilogramm pro Quadratmeter. Hier lagert J. König Sperrgut wie Transportgestelle. Für das Handling der Paletten sowie für die Beschickung und Kommissionierung ist auf der Bühne ein Palettenübergabeplatz installiert.
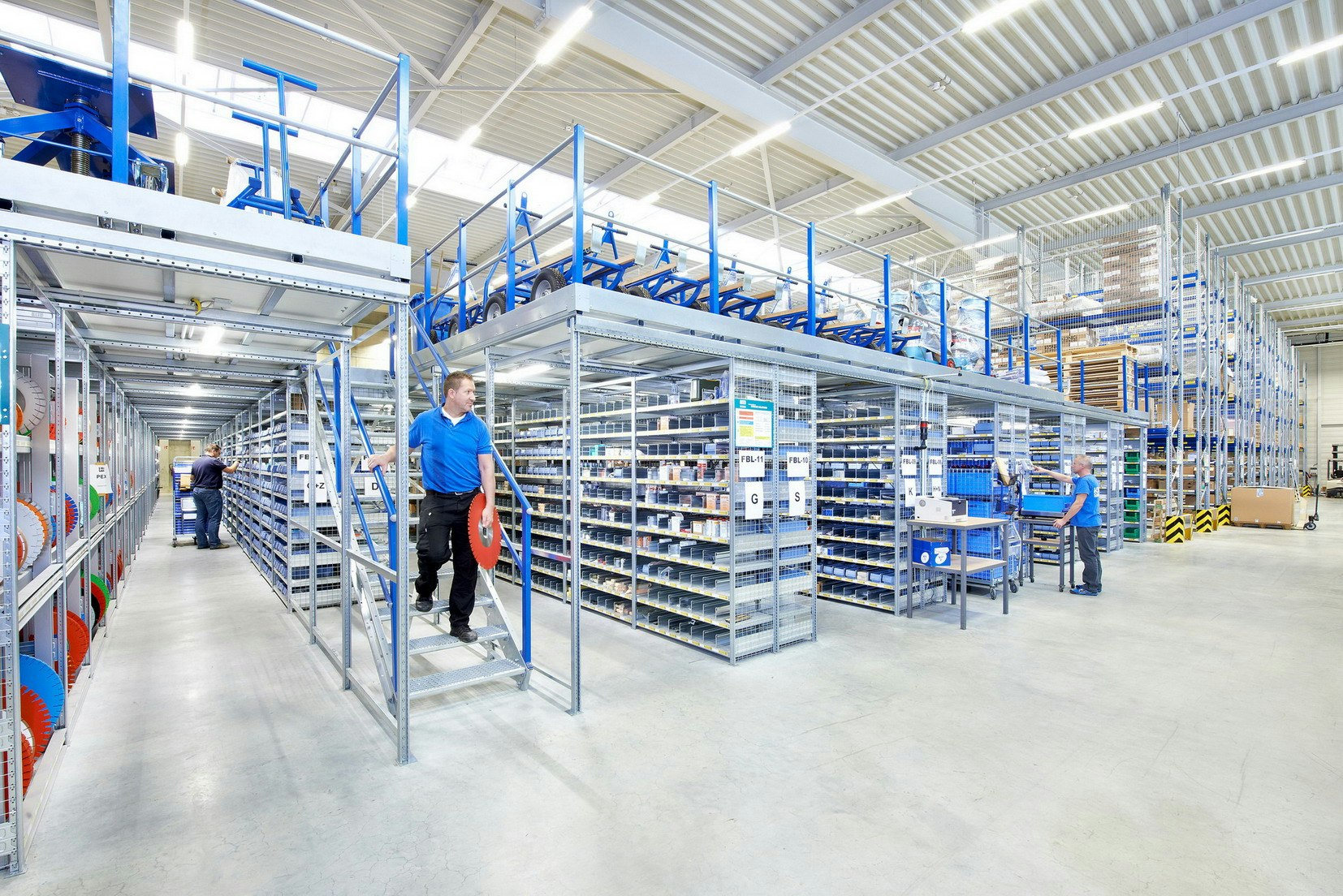
„Am Anfang des Projekts spielten wir den Gedanken durch, automatische Regalsysteme einzusetzen, zum Beispiel ein Automatisches Kleinteilelager“, erinnert sich Elmar Dreikluft. „Doch die Aufträge sind bei uns so inhomogen, dass wir in der jetzigen Lösung deutliche Vorteile sehen. Außerdem sind wir mit diesem Regalsystem wesentlich flexibler. Wir können uns auf Änderungen jederzeit einstellen.“ Voll automatisch erfolgt dagegen die Lagerverwaltung. Dazu hat J. König eine moderne Logistik-Software eingeführt. Mit dieser stellen wir die meisten Aufträge im Multi-Order-Picking-Verfahren zusammen“, beschreibt Elmar Dreikluft. Das heißt, Mitarbeiter kommissionieren mehrere Aufträge gleichzeitig. „Damit laufen sie wegoptimiert durch das Lager“, beschreibt Dreikluft dieses Vorgehen. Sind die Produkte auftragsbezogen auf Paletten zusammengestellt, verlassen sie über Paketdienste oder Speditionsunternehmen von Montag bis Freitag bis 16.30 Uhr das Logistikzentrum.
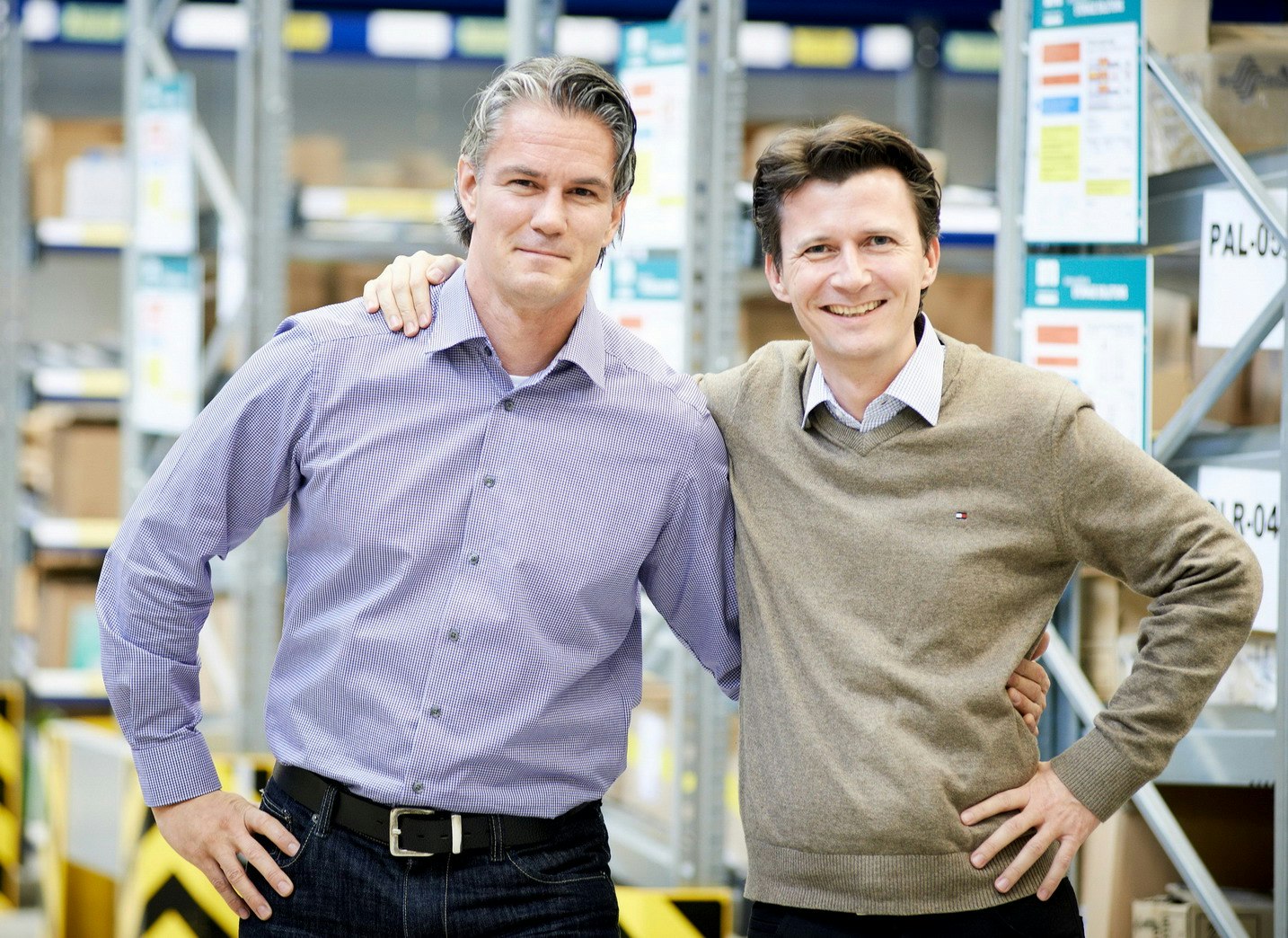
Partnerschaftliche Zusammenarbeit
„Dieses Projekt war außergewöhnlich“, ist Daniel Petri überzeugt. „Ohne einen Partner wie Bito hätte das Projekt sehr wahrscheinlich nicht funktioniert und das hätte existenzbedrohlich werden können.“ Bis zum Schluss gab es immer wieder Änderungen und Anpassungen. Doch der Meisenheimer Komplettanbieter hat auf jede Abweichung enorm flexibel und schnell reagiert. Der Umzug von der Firmenzentrale in das neue Lager erfolgte zwischen Weihnachten und Silvester. „Stichtag war der 7. Januar 2014, da musste der Betrieb laufen“, erinnert sich der Geschäftsführer. In wenigen Minuten wurden die Mitarbeiter am ersten Arbeitstag in das neue Lager und die Vorgänge eingeführt. „Selbst die älteren Kollegen in unserer Truppe haben das neue Lagerkonzept sofort akzeptiert“, bemerkt Dreikluft. Als schließlich das erste Paket kommissioniert wurde und fertig am Warenausgang stand, fiel dem ganzen Projekt-Team ein Stein vom Herzen. „Mit der neuen Intralogistik sind wir nun erheblich schneller und effizienter. Wir können deutlich Kosten einsparen und unsere Mitarbeiter müssen keine Überstunden mehr leisten “, ist Geschäftsführer Petri begeistert.
Downloads
160321_Bito_AB_Koenig.doc(437 KB)160321_Bito_AB_Koenig_Bild_1.jpg(235 KB)160321_Bito_AB_Koenig_Bild_2k.jpg(496 KB)160321_Bito_AB_Koenig_Bild_3.jpg(521 KB)160321_Bito_AB_Koenig_Bild_4k.jpg(809 KB)160321_Bito_AB_Koenig_Bild_5k.jpg(783 KB)160321_Bito_AB_Koenig_Bild_6k.jpg(845 KB)160321_Bito_AB_Koenig_Bild_7k.jpg(598 KB)160321_Bito_AB_Koenig_Bild_8k.jpg(698 KB)160321_Bito_AB_Koenig_Bild_9k.jpg(484 KB)BITO Pressekontakt:
Tanja Schmitt
BITO-Lagertechnik Bittmann GmbH
Unternehmenskommunikation
Obertor 29
D-55590 Meisenheim