Ergonomische Gestaltung von Packarbeitsplätzen
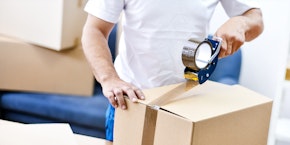
Nur zwei von fünf Mitarbeitern sind einer Umfrage zufolge mit ihren Computer-Arbeitsplätzen zufrieden. Viele leiden unter Einschränkungen und veraltetem Equipment. Eine Befragung der MSG Services AG im Jahr 2017 erbrachte das Ergebnis, dass rund 2200 Büroangestellte und 600 Business-Manager Defizite und veraltete Technik an ihrem Bildschirmarbeitsplatz beklagen. Dabei wurden auch ergonomische Gesichtspunkte wie die einfache Bedienbarkeit von Büro-Geräten beklagt.
Eine schlechte Ergonomie von Arbeitsplätzen kann zu vielfältigen Beeinträchtigungen der Gesundheit und damit zu Ausfällen der Mitarbeiter führen. Folgen können sein: Nacken-, Schulter-, Rücken-, Kreuzschmerzen, Verdauungsbeschwerden, schmerzende Beine, Herz- und Kreislaufstörungen, geringe Hirndurchblutung, Sehstörungen, Ischias, vielfältige Rückenprobleme, u. v. a. m.
Zu den Top 10 der Berufssparten mit den meisten Erkrankungen gehört neben Reinigungsdiensten, Hoch- und Tiefbau sowie Metallbau auch der Logistikbereich. Die Logistikbranche verlangt den Arbeitnehmer viel ab. Hier werden u. a. schwere Lasten getragen, gezogen, gehoben, kommissioniert und verpackt. Langes Stehen ist ebenfalls häufig nötig. Die körperlichen Belastungen sind hoch und zudem ist der Zeitdruck (besonders durch den E-Commerce) extrem. Die Arbeitsschritte müssen immer schneller verrichtet werden, wodurch der Leistungsdruck auf die Arbeitnehmer stetig ansteigt. Da kommen die Arbeitnehmer schnell an ihre Limits. Probleme mit der Wirbelsäule und mit dem Rücken sind sehr häufig in der Produktion und im Lager anzutreffen. Fehlbelastungen fördern Rückenleiden. Konkrete Faktoren sind Überkopfarbeit, regelmäßiges Bücken, Tätigkeiten mit gebeugtem Oberkörper und die dauerhafte Sitzhaltung am Schreibtisch. Typische Folgeerscheinungen sind Gelenk-, Wirbel- und Bandscheibenverschleiß. Auch psychische Faktoren wie Stress können zu Krankheitssymptomen am Rücken beitragen. Daher ist eine ergonomische Gestaltung der Arbeitsplätze in der Logistik bzw. im Lager besonders wichtig.
Was ist eigentlich Ergonomie?
In der Neuzeit (von 1919 an) beschäftigte sich zunächst das Bauhaus mit dem Thema Ergonomie. Konsequent und umfassend wurde sie jedoch erst von dem US-amerikanischen Produktdesigner Henry Dreyfuss und seinem Designbüro entwickelt und angewandt. Die ergonomische Lehre verfolgt das Ziel, Arbeitsplatz und -umgebung optimal an den Einzelnen anzupassen. Der Begriff stammt aus dem Griechischen und setzt sich aus den Worten „ergon“ („Arbeit“) und „nomos“ („Gesetz“) zusammen.
Laut REFA ist "ein ergonomischer Arbeitsplatz ein an die Belange des dort tätigen Menschen optimal angepasster Arbeitsplatz. Bei dieser Verbesserung der Mensch-Maschine-Schnittstelle stehen Arbeitsschutz, Wirtschaftlichkeit und Humanität im Fokus. Ziel ist, die dort Beschäftigten vor körperlichen Schäden auch bei langfristiger Ausübung ihrer Tätigkeit zu schützen, die psychische Gesundheit zu gewährleisten und so eine effiziente und fehlerfreie Arbeitsausführung zu ermöglichen." (1) Die Bundesanstalt für Arbeitsschutz und Arbeitsmedizin (BAUA) definiert Ergonomie als "Theorie, die Prinzipien, Daten und Methoden auf die Gestaltung von Arbeitssystemen anwendet mit dem Ziel, das Wohlbefinden der Menschen und die Leistung des Gesamtsystems zu optimieren.“ Ergonomie kann man generell als eine Teildisziplin des Arbeitsschutzes ansehen.
Normen, Richtlinien und Gesetze
In Deutschland beschäftigen sich neben Universitäten und Fachhochschulen vor allem die BAUA "Fachgruppe 2.3 Human Factors, Ergonomie", der VDI und der DIN-Normenausschuss Ergonomie (NAErg) mit der ergonomischen Gestaltung von Arbeitsplätzen. Gemeinsame Ausschüsse des DIN und des VDI stimmen ihre Arbeitspläne ab. Laut der Kommission Arbeitsschutz und Normung ist "aus Sicht des Arbeitsschutzes die Überschneidung von DIN-Normen und VDI-Richtlinien mit Skepsis zu betrachten. Zwar werden beide nach festen Regeln erarbeitet, allerdings stellt die mehrteilige Normenreihe DIN 8201 wesentlich detailliertere Anforderungen an das Normungsverfahren, als es die 16-seitige VDI 10002 für das Richtlinienverfahren vermag. Das Arbeitsschutzgesetz (ArbSchG) verpflichtet den Arbeitgeber zur Vermeidung von Arbeitsunfällen und Sicherheit, arbeitsbedingten Erkrankungen sowie zur menschengerechten Gestaltung der Arbeit (§§ 2, 3 ArbSchG). Hierzu gehören sowohl die Gestaltung der Arbeitsstätte, des Arbeitsplatzes und der Arbeitsumgebungsbedingungen als auch die Gestaltung von Arbeitsverfahren, -ablauf und -organisation (Ergonomie). Welche Maßnahmen des Arbeitsschutzes und Sicherheit erforderlich sind, hat der Arbeitgeber durch die Gefährdungsbeurteilung nach § 5 ArbSchG zu ermitteln. In der 2016 umfassend geänderten Arbeitsstättenverordnung (ArbStättV) indes wird der Begriff der Ergonomie nun auch wörtlich berücksichtigt. Zudem sind seit 2016 in der ArbStättV auch die Inhalte der Bildschirmarbeitsverordnung (BildScharbV) zu finden, die dafür zeitgleich aufgehoben wurde. Laut der ArbStättV hat "beim Einrichten und Betreiben der Arbeitsstätten der Arbeitgeber die Maßnahmen nach ArbStättV § 3 Absatz 1 durchzuführen und dabei den Stand der Technik, Arbeitsmedizin und Hygiene, die ergonomischen Anforderungen sowie insbesondere die vom Bundesministerium für Arbeit und Soziales nach ArbStättV § 7 Absatz 4 bekannt gemachten Regeln und Erkenntnisse zu berücksichtigen."
Logistikoptimierungen
Checkliste: Tipps zur Auslegung von Packarbeitsplätzen
In unserer Checkliste: „Tipps zur Auslegung von Packplätzen“ erfahren Sie mehr zum Thema Ergonomie.
Welche Arten von Belastungen existieren an Packarbeitsplätzen?
Man unterscheidet in der Arbeitswissenschaft zwischen Belastung und Beanspruchung. Belastungen sind objektiv bestimmbar und werden in physische, psychische und psychosoziale Belastungen unterteilt. Sie wirken nicht unmittelbar, sondern werden über persönliche Ressourcen und individuelle Voraussetzungen sowie externe Ressourcen (z. B. Tätigkeits-, Handlungs-, Entscheidungsspielraum) der Mitarbeiter in ihren Beanspruchungsfolgen beeinflusst. Rückkopplungen von Beanspruchungsprozessen wirken auf Belastungsfaktoren modifizierend ein. Eine Gesamtbelastung ergibt sich aus einer Vielzahl einzelner Belastungsfaktoren und wirkt somit als Belastungskombination. Daher kann man bei der ergonomischen Gestaltung eines Arbeitsumfeldes nicht nur nach objektiven Kriterien vorgehen, sondern muss immer die subjektiven Auswirkungen auf den jeweiligen Mitarbeiter/in im Blickfeld haben.
An Packarbeitsplätzen treten eine Vielzahl von physischen, psychischen und psychosozialen Belastungen für den Verpacker auf. Beispiele sind:
schwere und sperrige Produkte werden gehandelt
Artikel werden in aufgestellten Faltschachteln oder Behälter über eine Kante hinweg eingepackt
Hebe- und Absenkbewegungen, z. T. auch Körperdrehungen mit angehobenen Lasten werden durchgeführt
es existiert eine Vielzahl von z. T. hohen Belastungsfaktoren
der Puffer an Arbeitsvorrat wird nicht kleiner
komplexe Buchungsvorgänge am Rechner müssen erledigt werden
es besteht eine große Anzahl an Wahlmöglichkeiten für Füllstoffe zur Sicherung der Waren im Karton und das Fertigmachen zum Versand der Packstücke
es entstehen körperlichen Belastungen durch das Ablegen der fertig gepackten Einheiten auf Paletten oder Förderbändern
vorhandener Staub sowie Lärm, etc. erschweren die Arbeit generell
Wie sieht ein optimal gestalteter Packarbeitsplatz aus?
Ein ergonomisch günstig gestalteter Packtisch ist elektrisch höhenverstellbar, sodass er durch den Verpacker auf die eigene Körpergröße optimal angepasst werden kann. Die Höhe kann abhängig vom zu verpackenden Gut variabel eingestellt werden. In die Arbeitsfläche des Packtisches ist eine Waage, die mit der Lagerverwaltungssoftware verbunden ist, eingelassen. Über der Waage, auf der der eigentliche Packvorgang stattfindet, befindet sich ein Spender für Verpackungshilfs- und -füllmittel. Bei Bedarf fallen diese direkt in die Verpackung. Leicht versetzt neben der Waage wurde ein Bildschirm in Sichthöhe angebracht. Auf einem stabilen Schwenkbrett darunter befindet sich die Tastatur. Daneben steht ein Drucker für die Versandpapiere, der aufgrund der Druckerhöhe auf einem tiefersitzenden Anbau abgestellt ist. Die Verpackungsmaterialien und Kartons befinden sich senkrecht stehend über der Arbeitsfläche und können ohne Körperdrehung gegriffen werden. Direkt neben der Tischplatte mit der Waage erfolgt die Übergabe des Packstücks auf einen Stetigförderer mittels eines flexiblen Blechs. Dadurch werden Hebe- und Schiebebewegungen für den Verpacker vermieden. Ebenso wird durch einen je nach Verpackungsvorgang vorhandenen Hubtisch sichergestellt, dass sich der Verpacker beim Verladen des Packstücks auf eine Palette oder einen Rollcontainer nicht bücken oder übermäßig strecken muss. Für das Heben und Senken größerer Lasten können Manipulatoren zur Verfügung gestellt werden. Wenn möglich sind Steh- bzw. Sitzarbeitsplätze anzubieten. Durch eine derartige Gestaltung vermeidet man unnötiges Heben und Absenken der Lasten. Weiterhin wird das Bücken, Strecken und auch Körperdrehungen mit Gewichten verhindert.
Packtische sind immer individuell zu gestalten. Es müssen ausreichend Lagerflächen für einen Tagesbedarf an Hilfsmitteln (Klebeband, Papier, etc.) sowie strukturierte Ablageflächen und Müllentsorgungsmöglichkeiten vorhanden sein. Die Arbeitsumgebung sollte hell, sauber und staubfrei sein. Die Hilfsmittel für die Durchführung der Arbeitsaufgabe sollten griffgünstig und immer an den gleichen Stellen im Arbeitsbereich greifbar sein. Durch eine klare Struktur und Ordnung werden Suchaufwände und Fehler vermieden sowie die Arbeit generell erleichtert. Der Computerbildschirm am Packtisch muss scharf und kontrastreich anzeigen und die Eingabe-Masken sollten einfach und ansprechend gestaltet sein.
Steigerung der Arbeitseffektivität
Die zuvor beschriebene ergonomische Auslegung des Packarbeitsplatzes führt dazu, dass der Verpacker intensiver und mit geringerer Beanspruchung arbeiten kann. Er ist konzentrierter, ermüdet weniger und die Fehleranfälligkeit sinkt. Selbst für ältere Mitarbeiter sind solche Packplätze geeignet.
Ein Packplatz muss immer im Einzelfall untersucht und konfiguriert werden. Die Lösung stellt einen Kompromiss aus den vorliegenden Anforderungen aufgrund der Aufträge, der zu verpackenden Produkte, der Einbindung in die Prozesse und der beteiligten Mitarbeiter dar. Um die Komplexität der Gestaltungsaufgabe besser zu verstehen, denke man daran, dass ein Packarbeitsplatz beispielsweise für Rechts- und Linkshänder spiegelverkehrt ausgelegt werden muss.
Logistikoptimierungen
Checkliste: Tipps zur Auslegung von Packarbeitsplätzen
In unserer Checkliste: „Tipps zur Auslegung von Packplätzen“ erfahren Sie mehr zum Thema Ergonomie.
Literatur:
1 Ergonomischer Arbeitsplatz, Definition, REFA AG, Link
Ergonomie und Arbeitssicherheit im Lager, Bito Fachwissen, Link
Download Arbeitsschutzgesetz (ArbSchG)