Case TWIN DISC. Stapelbakken XL in een Lean manufacturing proces
Robuuste magazijnbakken met laag eigengewicht en een betere oplossing voor identificatie
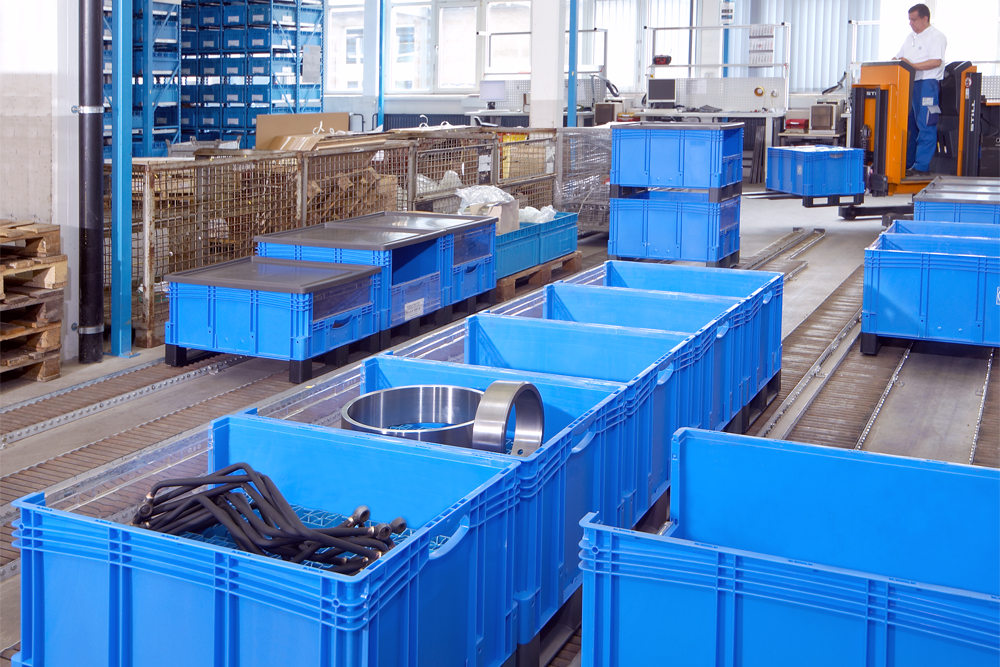
TWIN DISC is een Amerikaanse onderneming, die ruim 60 jaar vanuit Nijvel (B) opereert. Het bedrijf is wereldleider op vlak van ontwikkeling, productie en verkoop van mechanische transmissie onderdelen voor de scheepvaart. Dit ondermeer voor de commerciële en militaire maritieme markt, maar ook voor eigenaars van plezierjachten, de overheid en de industriële sector. TWIN DISC deed beroep op de kennis van BITO Systems nv bij het omschakelen naar lean manufacturing. Een gepersonaliseerd bakkensysteem draagt bij tot een performantere opslag.
Wat had TWIN DISC nodig?
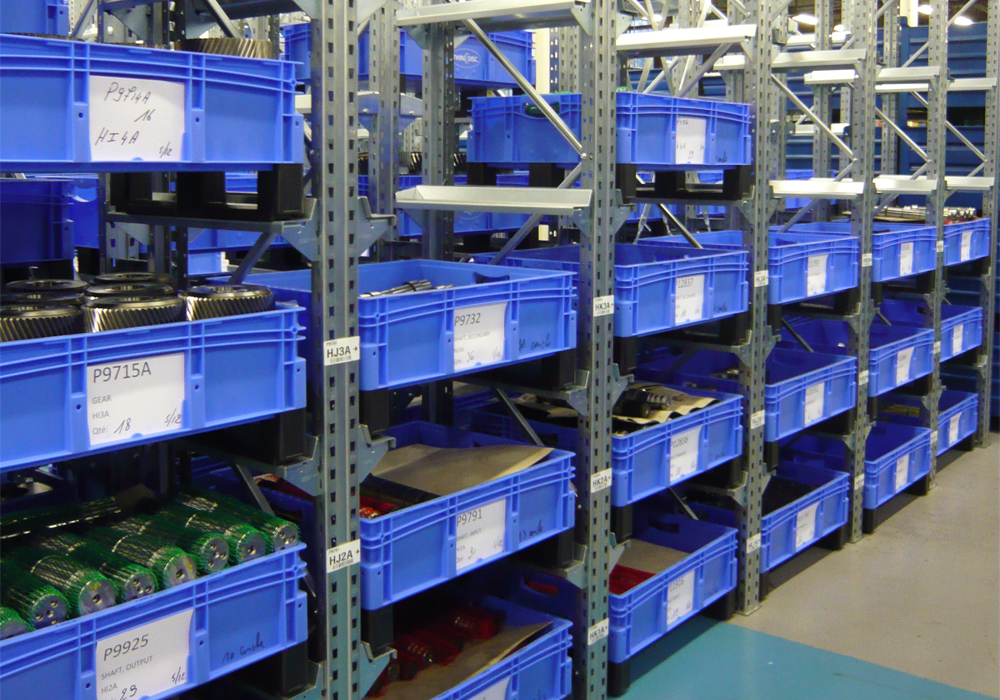
Met de omschakeling naar lean manufacturing, een productiesysteem dat hoogstaande kwaliteit, lage kosten en betrouwbare en korte levertermijnen garandeert met een minimum aan middelen. Deze switch droeg bij tot een efficiëntere aanpak van de productie binnen het bedrijf. Anderzijds werd ook het bestaande bakkensysteem doorgelicht. Thierry Colassin, hoofd van de assemblage bij Twin Disc in Nijvel, licht toe: “De stalen bakken waarover we destijds beschikten, waren qua formaat niet afgestemd op de onderdelen die we produceren. Kleine onderdelen lagen er wat ‘verloren’ in, grotere pasten er daarentegen niet in. Tandwielen liepen soms beschadiging op. Bovendien waren de draadwandcontainers niet manueel verplaatsbaar, niet stapelbaar en konden we geen identificatievignet toevoegen om achteraf na te gaan welke bak welke inhoud bevatte.” In die optiek ging het bedrijf actief op zoek naar een betrouwbare partner om dit probleem aan te pakken. Na een testfase van ongeveer 6 maanden, waarbij we een tiental bakken uitprobeerden in verschillende fases, opteerden we voor de BITO XL stapelbakken”, zegt Thierry Colassin.
Hoe losten we het op?
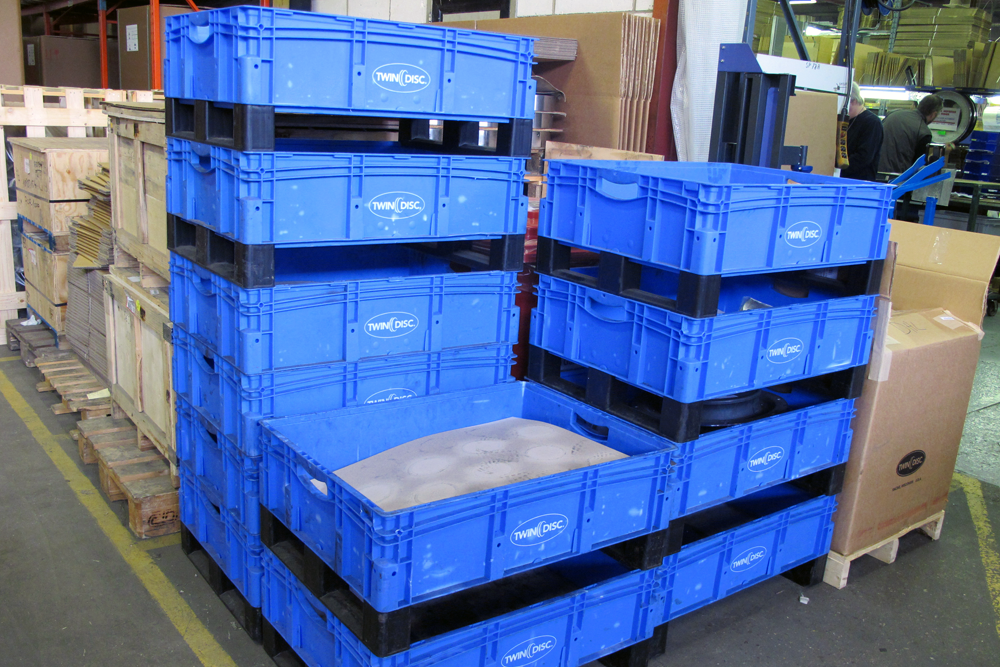
De zware draadwandcontainers werden vervangen door XL stapelbakken in kunststof met licht eigengewicht maar robuust met lange levensduur. Het is een Eurobak met de afmetingen 800L x 600B x 220H mm en een inhoud van 91 liter. Een dubbele bodem voor het draagvermogen en uitvoering met palletvoeten voor het makkelijk verplaatsen met een handpallettruck in geladen toestand.
Gebruik in de praktijk
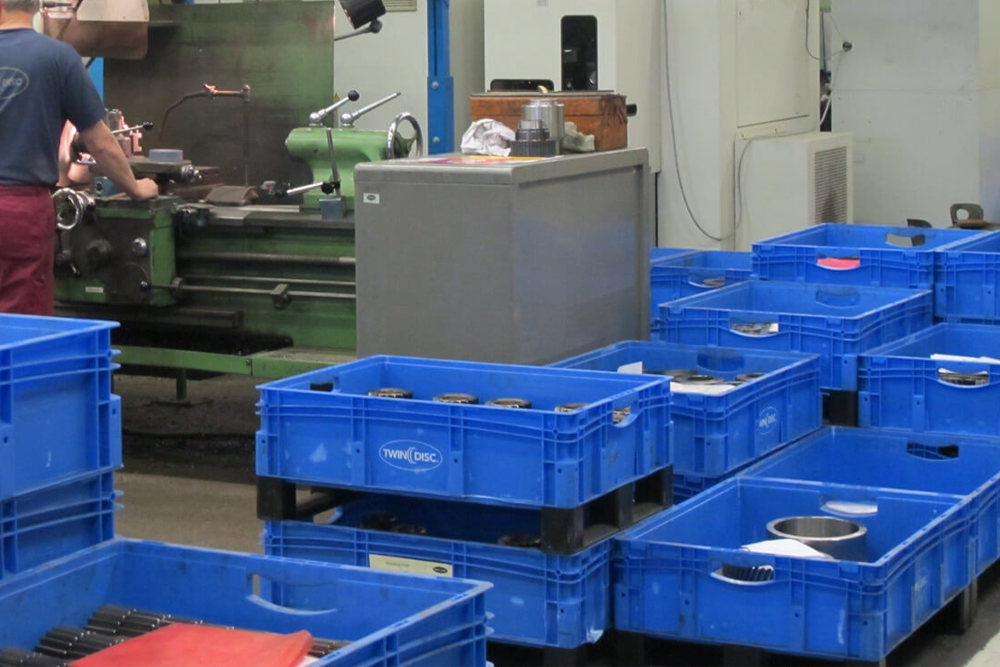
De opslagruimte werd geoptimaliseerd, omdat BITO stapelbakken XL een gewicht kunnen dragen tot 200 kg en stapelbaar zijn tot 800 kg, is er 100 m² opslagruimte gewonnen. De blauwe stapelbakken XL uit polipropyleen kregen een opdruk van het logo van Twin Disc, zodat het voor de assemblage afdeling steeds duidelijk is welke bakken van leveranciers zijn en welke eigen bakken zijn. De bakken hebben eveneens een ergonomisch gevormde, open handgreep waardoor ze gemakkelijk te verplaatsen zijn. BITO voorzag aan alle zijden etikethouders, een belangrijke voorwaarde waaraan voldaan moest worden. Bovendien zijn alle bakken voorzien van een dubbele bodem, waaraan gemakkelijk palletvoeten kunnen worden bevestigd door middel van een eenvoudige schroefmontage. Om ook kleinere producten goed te kunnen stockeren en beter te beschermen tegen beschadigingen, leverde BITO inlegbare scheidingen.
De voordelen voor KHS
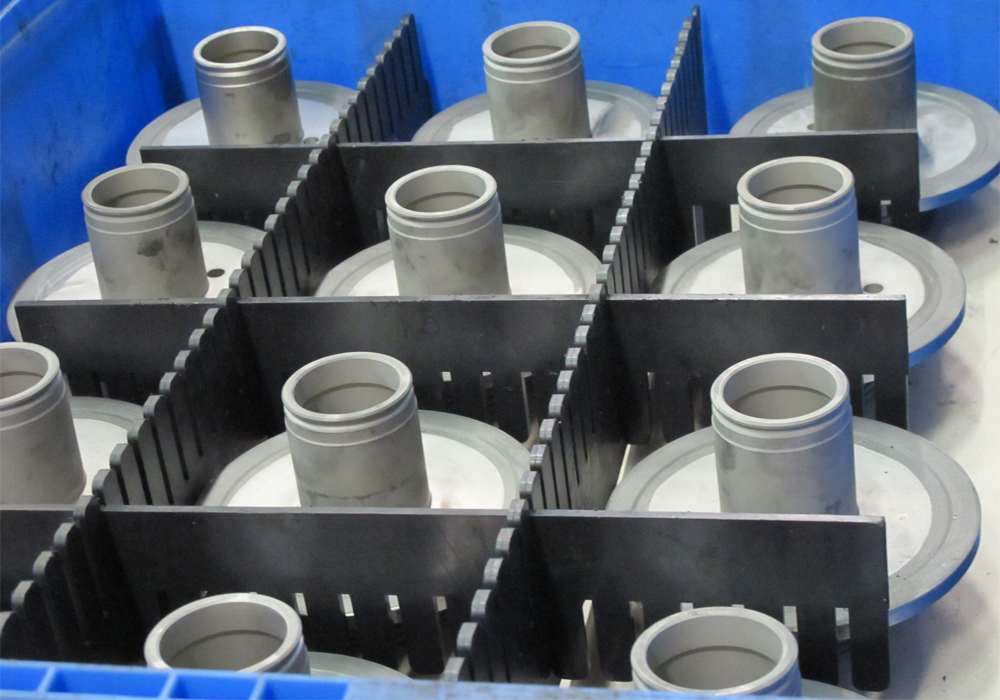
- Dankzij de stapelbaarheid 100 m² opslagruimte gewonnen
- Reductie van beschadigde onderdelen door de kunststofbakken en hun inlegbare scheidingen.
- Tijdwinst door het gebruik van etiketten op de bakken dat zorgt voor minder zoeken achter producten.
- Kunststofbakken met waterafvoergaatjes waardoor ze gemakkelijker kunnen worden afgewassen en de productiemedewerkers netter kunnen werken.
- Handige magazijnbakken met laag eigengewicht, makkelijk verplaatsbaar, maar met een hoge draagkracht voor zware onderdelen.
De klant getuigt
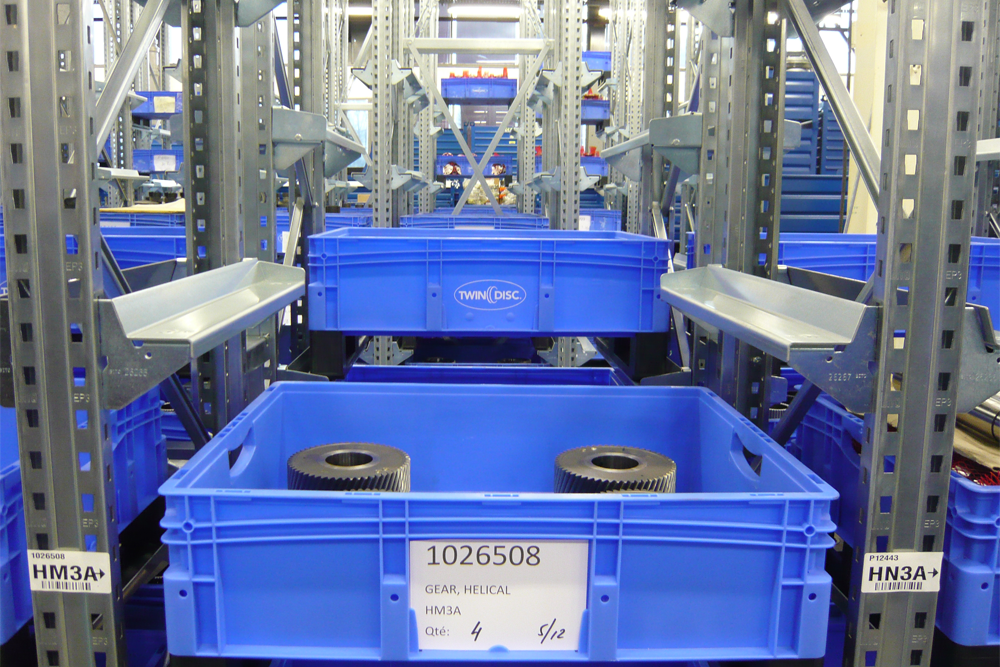
“De stalen bakken waarover we destijds beschikten, waren qua formaat niet afgestemd op de onderdelen die we produceren. Kleine onderdelen lagen er wat ‘verloren’ in, grotere pasten er daarentegen niet in. Tandwielen liepen soms beschadiging op. Bovendien waren de bakken log, niet stapelbaar en konden we geen identificatievignet toevoegen om achteraf na te gaan welke bak welke inhoud bevatte. In die optiek ging het bedrijf actief op zoek naar een betrouwbare partner om dit probleem aan te pakken. BITO is de enige leverancier van bakken die een draagkracht hebben die aangepast is aan de onderdelen die we produceren. Na een testfase van ongeveer 6 maanden, waarbij we een tiental bakken uitprobeerden in verschillende fases, opteerden we voor de BITO XL-bakken”. Thierry Colassin, Hoofd Assemblage