Kaizen, ou la quête de l'amélioration continue
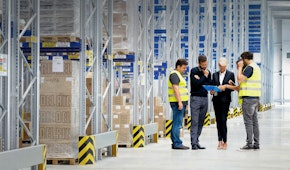
Derrière le terme japonais « Kaizen » se cache une philosophie qui peut s'appliquer dans de nombreux domaines de la vie mais aussi dans les processus industriels. Kaizen signifie « amélioration continue » ; il s'agit d'un état d'esprit, d'une philosophie de la vie orientée vers une optimisation ou un changement continu et infini. Les modifications et améliorations des processus et des produits dans la logistique de production s'effectuent étape par étape et de manière ponctuelle. Les origines du Kaizen remontent aux années 50, le Japon étant encore dévasté par la guerre. A l'époque, Toyota devait trouver une solution à un conflit syndical qui a entraîné l'implication de tous les employés restants dans un processus d'optimisation continu. La garantie d'un emploi tout au long de la vie implique que le capital humain doit être extrêmement rentable. Il était logique d'améliorer continuellement les compétences des travailleurs et d'utiliser efficacement leurs connaissances, leur expérience et leur rendement au travail. Toyota a introduit le Kaizen parmi de nombreux autres principes comme le Kanban, la livraison juste à temps des composants, le Kenbutsu (implication des fournisseurs), etc. au système de production Toyota dans la fabrication automobile. Selon le célèbre ingénieur et directeur de production de Toyota Taiichi Ohno, le point de départ du concept du système de production Toyota est l'élimination des gaspillages. Il a défini les sept types de gaspillage. Bien que le livre de Taiichi Ohno Toyota Production System: Beyond Large-Scale Production ait été traduit en anglais dans les années 1980, Kaizen s'est d'abord fait connaître en Occident grâce au consultant en management japonais Masaaki Imai et son livre Kaizen: Japanese spirit of improvement. En principe, le Lean Production et le Lean Management étaient déjà appliqués à cette époque. Par la suite, le concept a été adopté dans l'économie occidentale et développé en un système de gestion connu dans la pratique sous le nom de Processus d'amélioration continue (PAC).
Les bases de la méthode Kaizen
Le Kaizen est une façon de penser qui est internalisée par tous les employés et appliquée dans tous les processus d'une entreprise. Les cinq fondements centraux du Kaizen sont les suivants : Orientation processus, orientation client, orientation qualité, orientation critique et normalisation.
En passant d'une orientation purement axée sur les résultats à une orientation processus et à l'optimisation des bénéfices grâce à l'optimisation constante des processus, l'orientation client est inévitable. Parce que l'optimisation des bénéfices n'est possible qu'avec une satisfaction client élevée, car l'acquisition de clients est plus coûteuse que la fidélisation de clients. Cependant, il existe des clients externes et internes (branche, organisation ou unités de production). Des problèmes surgissent souvent à l'interface entre ces unités organisationnelles, c'est pourquoi l'accent est mis sur la mise en œuvre des optimisations et des objectifs de Kaizen (assurance et augmentation de la qualité, satisfaction du client et réduction des coûts par les employés). Dans le cadre de la gestion de la qualité totale, un contrôle permanent de la qualité totale est effectué : la qualité est contrôlée en permanence pendant la production par une procédure de mesure élaborée. Ce n'est pas facile à accepter pour beaucoup de gens, mais dans le Kaizen, la critique est perçue comme une opportunité d'amélioration continue. Cependant, non seulement des critiques, mais aussi des suggestions d'amélioration doivent être soumises à la direction. Les propositions seront examinées et évaluées pour en vérifier la convivialité et, si possible, mises en œuvre. Il en résulte un cycle continu de planification, d'exploitation, de contrôle et d'amélioration : le cycle PDCA (Plan → Do → Check → Act). Une amélioration appropriée doit être fixée comme norme. Toutefois, cette norme doit encore faire l'objet d'un examen en vue d'y apporter des améliorations.
Outils et méthodes
Il existe de nombreux outils et méthodes dans le Kaizen qui peuvent rendre visibles les causes de toutes sortes d'erreurs et de gaspillages dans l'entreprise. Il montre où et comment des améliorations peuvent être apportées. Son application est relativement simple, mais néanmoins, grâce à l'utilisation continue de tous les employés, des changements majeurs peuvent être réalisés. En voici quelques exemples : 5S/5A, ateliers Kaizen pour discuter des suggestions d'amélioration, checklist des 3 Mu, liste de contrôle 6-W, diagramme Ishikawa pour l'analyse des causes, les 5 Pourquoi, Gemba-Walks, Kanban, Poka Yoke, etc.
Les 5 Pourquoi
Il s'agit d'une technique de questionnement pour explorer la racine du défi. Selon la philosophie Kaizen, il faut d'abord l'appliquer pour déterminer le défi. On se demande, par exemple, « Pourquoi cela s'est-il produit », et la réponse correspondante sert de base à la question suivante. Tous les défis n'ont pas une cause sous-jacente unique. Par conséquent, il peut être nécessaire de poser une séquence différente de 5 Pourquoi pour chaque cause. Le résultat dépend toujours de la connaissance et de la persévérance des personnes interrogées.
Exemple :
Défi : Le chariot élévateur ne démarre pas.
- Pourquoi ? : La batterie est à plat.
- Pourquoi ? : L'alternateur ne fonctionne pas.
- Pourquoi ? : La courroie du ventilateur est déchirée.
- Pourquoi ? : La courroie du ventilateur était déjà vieille et n'a pas été changée.
- Pourquoi ? : Le chariot élévateur n'a pas été correctement entretenu. (Cause profonde)
5S/ 5A
Dans la méthode 5S/5A, l'employé analyse son environnement de travail pour détecter tout gaspillage et toute activité inutiles et prend les mesures appropriées pour les éliminer. Tout cela commence par la lettre S en japonais.
- Seiri : supprimez les éléments inutiles de votre espace de travail.
- Seiton : classez ce qui restait après l'étape « Seiri ».
- Seiso : gardez votre lieu de travail propre.
- Seiketsu : triez vos préoccupations personnelles.
- Shitsuke : établissez des normes.
Ateliers Kaizen
Tous les employés d'un lieu de travail rencontrent régulièrement leurs supérieurs pour discuter des problèmes qui sont survenus et des mesures à prendre pour les améliorer. Les postes de travail, les zones de travail et la situation « sur place » sont examinés, les choses sont vues et analysées en direct. Dans la mesure du possible, les améliorations sont mises en œuvre et testées directement. Les thèmes abordés peuvent être les suivants :
- les processus opérationnels, le dédoublement du travail, les activités inutiles
- les problèmes de qualité et défauts de produits, d'outils ou de machines
- la mauvaise organisation des postes de travail
- le retard dans les activités et les processus individuels
- les rationalisations qui simplifient ou accélèrent les processus
- etc.
Afin de pouvoir mettre en œuvre et tester directement les améliorations des ateliers Kaizen, il est utile de travailler avec des technologies et des outils que les employés eux-mêmes peuvent optimiser pour leurs besoins. Un exemple BITO : avec le système de transport sans chauffeur « LEO Locative », les employés peuvent eux-mêmes régler ou « programmer » des voies ou des commandes jusqu'à ce qu'elles soient adaptées de manière optimale à leurs besoins. Les collaborateurs n'ont pas besoin de support informatique externe, n'ont pas besoin d'obtenir des devis ou de demander un budget, ce qui leur permet de s'adapter de manière flexible à toutes les circonstances.
Checklist des 3 Mu
Cette liste de contrôle permet de découvrir les sources de gaspillage et les causes des problèmes.
- Muda : gaspillage
- Muri : surabondance
- Mura : dérogation aux normes ou aux règles
Les éléments suivants sont toujours vérifiés : employés, technologie, méthodes, temps, espace créatif, dispositifs et outils, matériel, volume de production, transports, circulation, espace, séquences de mouvements (ergonomie), mode de pensée (état d'esprit).
Sept types de déchets (mudas)
- surproduction
- temps d'attente
- transport inutile
- fabrication de pièces défectueuses
- surstockage
- déplacement inutile
- processus de fabrication défavorable
Objectifs et avantages pour la logistique interne et de production
En principe, le Kaizen peut être appliqué à n'importe quel domaine et processus. Dans les processus industriels, l’objectif principal est d’optimiser les profits en évitant le gaspillage (voir sept types de gaspillages), qui est obtenu par le biais du processus, de la clientèle, de la qualité, de la critique et de la normalisation, tout en optimisant constamment ces domaines. Comme l'a montré l'exemple de l'atelier Kaizen de LEO Locative, les employés ont davantage de possibilités d'optimiser leurs processus en fonction de leurs propres besoins, au sens du kaizen, de manière constante et par petites étapes. Cela crée un plus grand sens des responsabilités et une plus grande satisfaction parmi les employés, ce qui augmente la motivation et l'efficacité. Les propositions de solutions émanant du personnel peuvent et doivent également être récompensées afin d'accroître encore la motivation. L'application continue de règles simples pour améliorer les processus dans tous les secteurs crée des changements tangibles. Cela signifie également que l'on n'attend pas la solution parfaite, mais que l'on préfère des solutions simples mais efficaces. Tous les employés et départements sont toujours impliqués dans le Kaizen. Les problèmes sont alors des opportunités voire des défis et sont considérés comme le moteur du processus d'amélioration. Un exemple concret de Kaizen en intralogistique est par exemple l'optimisation continue des itinéraires de transport dans l'entrepôt. La réponse à de nombreuses questions se trouve dans l'environnement de travail direct. Kaizen utilise explicitement la créativité et l'intelligence de tous les employés ; souvent, même un investissement important en capital n'est pas nécessaire pour la mise en œuvre. Cette philosophie montre également qu'aucun processus n'est jamais entièrement optimisé. Les petites étapes d'optimisation s'enchaînent sans cesse.