Il metodo Kanban nella logistica di produzione
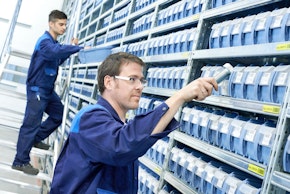
Se sei interessato alla logistica, alla tecnologia di magazzino, all'industria automobilistica o alla gestione, probabilmente hai già sentito parlare di Kanban. Ma cos'è esattamente il Kanban? Quando viene utilizzato? Quali sono i vantaggi? Se non sei sicuro che il Kanban sia adatto anche alla tua azienda, allora questo articolo potrebbe esserti d’aiuto.
Controllo decentralizzato della produzione con il sistema Kanban
Il Kanban è un metodo di controllo decentralizzato della produzione in cui schede dati - chiamate Kanban in giapponese - vengono utilizzate per attivare singoli processi di produzione oppure processi logistici. Il metodo Kanban è stato introdotto dal manager Toyota Taiichi Ohno nel 1950 negli stabilimenti Toyota. L'ispirazione vera e propria è arrivata grazie all'industria alimentare, e più precisamente dal settore dei supermercati. I vantaggi del metodo Kanban sono il controllo decentralizzato, il lean warehousing e la logistica just-in-time (JIT) delle parti necessarie alla produzione. Le principali informazioni riportate sui cartoncini Kanban sono: numero dell'articolo, quantità, ubicazione di stoccaggio, ecc.
La produzione invia un segnale alla fase di produzione a monte indicando che sono necessari nuovi componenti. Ad esempio, un contenitore vuoto con una scheda d'ordine per un componente specifico viene inviato al magazzino “lean” e a questo punto un contenitore pieno con l’articolo richiesto viene riportato al punto di utilizzo. Il magazzino “parti” ora sa che questo articolo deve essere riordinato in una certa quantità e invia questo ordine di acquisto alla fonte (il fornitore). Il fornitore completa l'ordine e consegna la quantità richiesta del componente corrispondente al magazzino lean.
La scheda kanban funge quindi da scheda di ordine per la produzione, che attiva uno specifico ordine di produzione come un’“onda di risonanza” che va dalla produzione al fornitore. Nella seconda variante, la carta kanban funge da carta d'identità per il nuovo componente da produrre o ordinare. Due fasi di produzione adiacenti sono collegate per formare un circuito di controllo, che garantisce un coordinamento senza problemi delle fasi successive. Ad esempio, la fase di produzione A recupera un componente dal magazzino lean (magazzino buffer) e la fase di produzione B reintegra il magazzino “parti” con il componente corrispondente.
I principi Push e Pull
I vantaggi principali del metodo sono il controllo decentralizzato e l'autocontrollo in combinazione con il principio di traino (PULL) (principio di tenuta, hold-principle). I livelli delle scorte possono essere notevolmente ridotti rispetto al classico principio di spinta (PUSH) (principio di portare, bringing principle). Il sistema Kanban è decisamente più robusto e flessibile rispetto al metodo classico. Con il classico controllo centrale della produzione, quest’ultima si basa sulle stime della domanda. A tal fine, i dati di mercato e di vendita vengono analizzati e sulla base di quanto ottenuto, vengono preparate le previsioni. Il magazzino parti gestisce molti componenti e attiva gli ordini in base alle scorte esistenti. Gli ordini vengono effettuati sulla base delle previsioni e allo stesso tempo viene mantenuta una scorta di sicurezza. Il pericolo con i sistemi push è spesso legato ad errori di calcolo. Ciò può portare ad una stima eccessivo, e quindi over stock della merce, oppure ad una stima troppo prudente, con conseguente insoddisfazione dei clienti a causa di carenze della merce (rottura di stock).
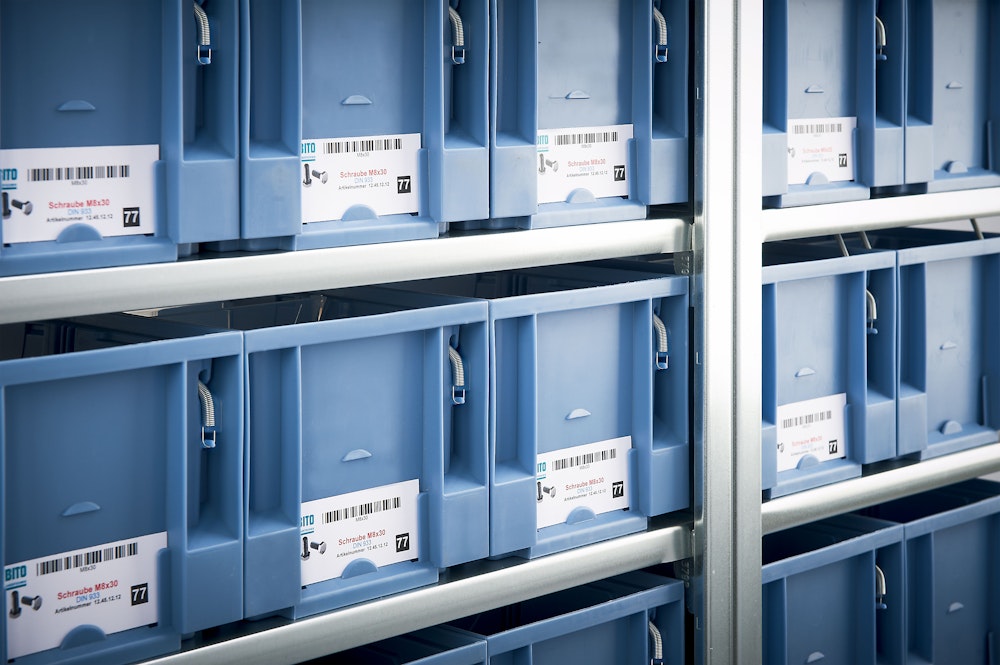
Gestione nel sistema Kanban
Con il sistema Kanban, nessuno ha bisogno di conoscere l'intera catena di processo. Solo il contenitore Kanban aperto viene riempito nella rispettiva ubicazione locale. Il sistema si dimostra quindi autoregolante e auto-organizzato e si basa su conoscenze locali e regole semplici. Assomiglia a sistemi auto-organizzati dalla natura, che si basano sull'intelligenza dello sciame (SI - Swarm intelligence - I sistemi SI sono spesso costituiti da una popolazione di agenti semplici che interagiscono a livello locale tra loro e con il loro ambiente). Ciò si traduce in una nuova funzione per i manager nel sistema kanban. Occorre prima impostare le condizioni di contesto in modo che la catena di processo possa funzionare. Tuttavia anche la concezione dell'”onda di risonanza” (vedi sopra) richiede spesso l'uso dell’esperienza di molte persone, cioè dell'intelligenza dello sciame. Al manager viene assegnato il ruolo del team manager, il cui compito è quello di organizzare l'auto-organizzazione del team. Inoltre, funge da moderatore, motivatore, coach, coordinatore e conflict manager o troubleshooter al fine di armonizzare i processi.
Quando ha senso il metodo Kanban?
Il sistema kanban non può essere utilizzato ovunque. Se si producono solo pochi pezzi o pochi prodotti, il metodo non è adatto. Si adatta meglio a produzioni con un'alta percentuale di parti identiche e con un piccolo numero di varianti. Il controllo della produzione e il flusso di materiali, la logistica e il rifornimento si basano esclusivamente sul consumo effettivo di materiale nel punto di fornitura o di consumo. Come già accennato, questo metodo offre un alto grado di flessibilità e scorte snelle. Tuttavia, l'intera catena di approvvigionamento può essere interrotta se un punto del processo non è disponibile. Se vuoi implementare il KANBAN, la tua azienda dovrebbe soddisfare alcuni prerequisiti:
Produzione continua
elevato grado di standardizzazione del prodotto con produzione rigorosamente sincronizzata
ubicazioni uniche per l'esatta assegnazione di carte e contenitori
gestione coerente dei contenitori
grandi fluttuazioni nella produzione devono essere evitate
i cicli di trasporto devono essere accorciati e progettati in modo uniforme
Contenitori e scaffalature Kanban
I sistemi speciali di scaffalature e container per i sistemi Kanban e la logistica sono diventati componenti standard nell'intralogistica. Questi includono i contenitori C-parts, che combinano i vantaggi dei contenitori di stoccaggio a scaffale e i contenitori “a fronte aperta”, o i contenitori Euromodule. Lo spazio nei ripiani Kanban viene utilizzato in modo ottimale dai contenitori C-parts. Consentono il picking superiore e frontale, cioè l'accesso alle parti C dalla parte anteriore (la finestra viene spinta verso il basso) e dall'alto (la scatola viene estratta e il dispositivo di ritenuta la tiene nello scaffale). Il disco di dosaggio della scatola consente di utilizzare il volume di riempimento fino all'alto. Attraverso la finestra, l’addetto può vedere esattamente quante parti sono ancora nella scatola in qualsiasi momento. Con il kanban a contenitore singolo, il principio viene implementato all'interno di una scatola. Se l'ultima parte viene rimossa nella parte anteriore, la quantità di alimentazione può essere utilizzata tirando su il disco di dosaggio.
Il processo di ordinazione di nuove parti C viene attivato rimuovendo la carta o i tag RFID dal retro della scatola. Con il kanban a due contenitori, la prima cassa viene estratta dallo scaffale dopo che l'ultima parte è stata rimossa. La carta viene rimossa e viene attivato il processo di ordinazione. Quindi la seconda scatola viene tirata nella posizione anteriore. La scatola ordinata con le parti di alimentazione, quando arriva presso lo scaffale kanban, viene spinta da dietro (principio FIFO). Un contenitore Euromodule è anche molto adatto per il metodo Kanban, in quanto può essere gestito bene in scaffalature a ripiani inclinati o in scaffalature dinamiche a gravità (flow rack). È profondo 600 millimetri e disponibile in varie altezze e larghezze. La serie è progettata in modo tale che le diverse dimensioni del contenitore possano essere impilate in modo modulare, e possono essere alloggiate in maniera molto stabile su un Europallet. È estremamente stabile e quindi impilabile in modo sicuro e ha anche un grande volume interno. Le superfici interne lisce consentono una facile pulizia. Con le maniglie ergonomiche integrate, il contenitore Euromodule può essere facilmente tirato e trasportato.
Sistema Kanban con codice a barre o RFID
Attualmente sono utilizzati supporti di memorizzazione come codici a barre o chip RFID al posto della scheda Kanban. I dati o l'ordine di produzione vengono trasferiti tramite WIFI al sistema di gestione del magazzino, al sistema ERP o al fornitore di componenti corrispondente. Con un sistema che utilizza i codici a barre, il codice dei contenitori dei componenti vuoti sono scansionati manualmente da un dipendente e trasmessi al rispettivo fornitore, che quindi può attivarsi per la consegna di questi articoli. In un sistema RFID, questo processo è automatizzato. I dati dell'articolo e del contenitore sono trasmessi automaticamente dallo stabilimento di produzione del cliente al magazzino centrale tramite l'identificazione a radiofrequenza (RFID). Ciò significa che gli ordini ripetuti automatici vengono effettuati senza scansione e senza registrazione manuale. Il tag RFID o transponder RFID ha un'antenna ed è attaccato al rispettivo oggetto o contenitore Kanban. Ogni giorno può essere identificato da un numero di sicurezza univoco. Inoltre, un sistema RFID è costituito da un lettore per la lettura del transponder e da un'unità trasmettitore per la trasmissione dei dati o il riordino automatizzato dei componenti per la produzione.