Siemens améliore le service avec un nouvel entrepôt à l'épreuve du temps
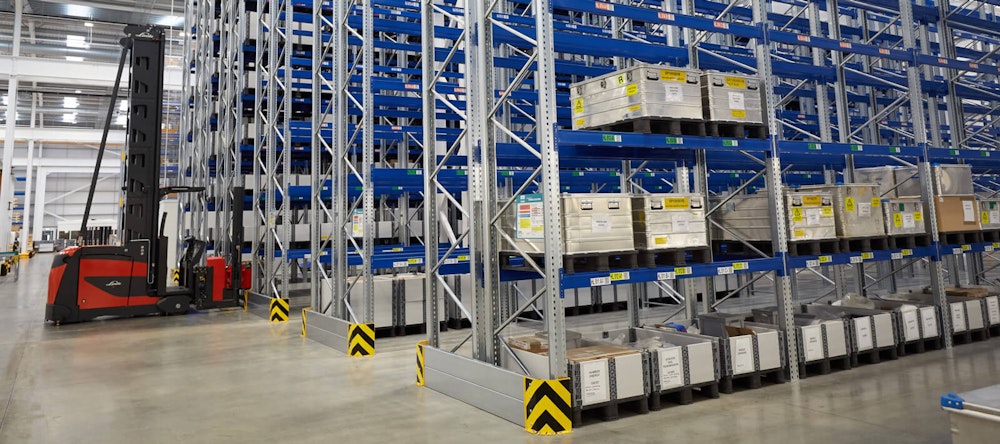
Siemens Industrial Turbomachinery a investi 48 millions de livres sterling sur le site de Teal Park. Les activités de service et de stockage sont regroupées dans ce centre international d'exploitation (GSOC) afin de promouvoir la santé et la sécurité, de réduire les temps de préparation et les coûts tout en augmentant les capacités de service. Ce centre à l'épreuve du temps a été livré dans les délais et le budget prévus.
Siemens Industrial Turbomachinery conçoit, fabrique et entretient de petites turbines à gaz industrielles, avec un parc de plus de 3 500 unités dans 90 pays. 1500 d'entre eux restent opérationnels auprès de clients clés de l'industrie pétrolière et gazière, de clients industriels, d'hôpitaux et de papeteries.
Pour se démarquer de la concurrence et fournir un service à la clientèle de qualité, essentiel à la pérennité de l'entreprise, Siemens a investi 13 millions £ dans le projet de construction d'un nouveau centre mondial d'opération de service (GSOC); juste à côté de son centre de révision sur son Site de Teal Park à Lincoln. Cette stratégie permet de consolider ses services et ses opérations logistiques. L'ensemble du site représente un investissement de £ 48 millions.
Les principaux objectifs de la nouvelle installation multi-fonction d’entreposage, de gestion des moteurs, d’outillage et de pièces de rechange étaient les suivants: promouvoir la santé et la sécurité, faciliter la croissance, augmenter la vitesse de cycle, augmenter les capacités et réduire les coûts dans le cadre d’une opération pérenne.
La consolidation comprend le déplacement des petites pièces de turbines à gaz de Siemens, le stockage des moteurs et des outils, précédemment situés sur un site à proximité, ainsi que la mise en place du stockage hors site et des activités de la société du groupe de turbines à gaz aérodérivatives de Siemens.
Cette empreinte opérationnelle combinée de 12 000 mètres carrés devrait s’inscrire dans le nouveau GSOC de 7 000 mètres carrés, tout en maximisant l’efficacité opérationnelle.
Siemens a relevé ce défi en collaborant étroitement avec les fournisseurs de MHE afin de fournir une solution intralogistique innovante permettant de stocker et de sélectionner les 15 000 unités de gestion des stocks de la société, allant des écrous aux boulons jusqu’à des moteurs de 6 tonnes.
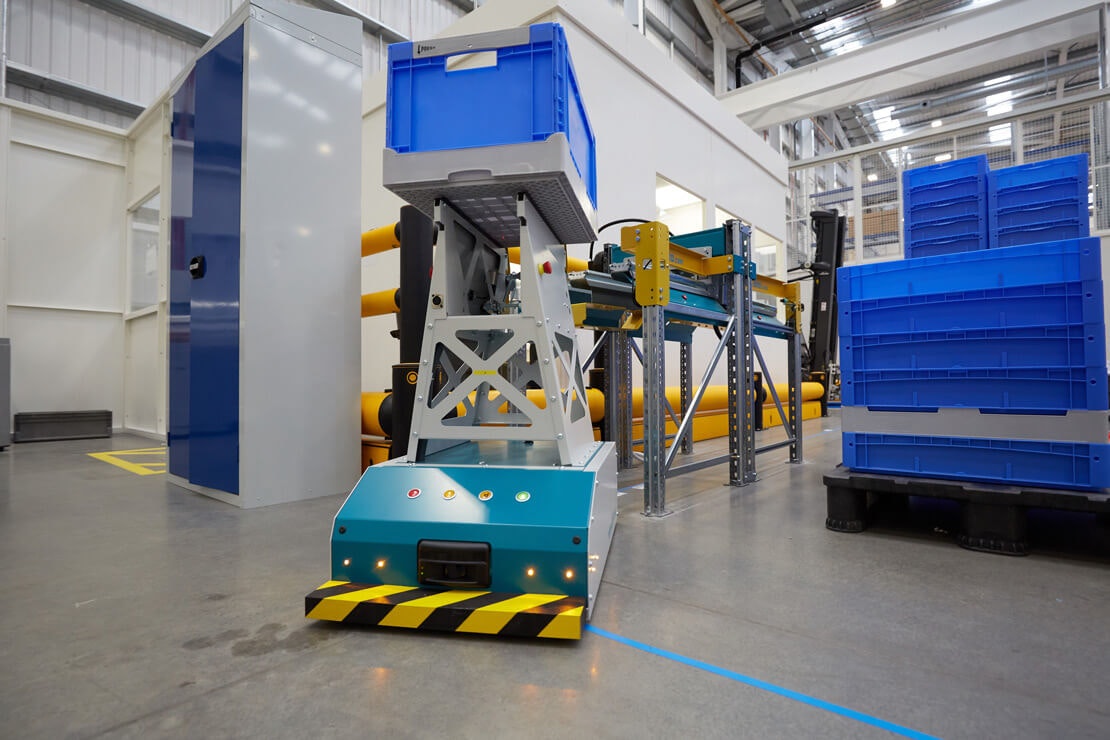
Une installation de rayonnages sur mesure réduit l'encombrement
L'ancienne installation stockait des lourds moteurs directement sur le sol de l'entrepôt. Cette organisation mobilisait une grande surface au sol et n'exploitait pas la surface disponible en hauteur; tout en étant inefficace pour les ingénieurs qui souhaitent localiser un moteur spécifique. Cet "espace aérien" a dû être utilisé pour comprimer les entrepôts sur une surface de 7 000 mètres carrés, tandis qu’une gestion plus efficace des stocks était nécessaire pour que les moteurs aient leur propre « emplacement ».
La réponse était un impressionnant rayonnage à palettes haut sur trois niveaux offrant 72 emplacements, desservis par un chargeur latéral à guidage par fil. La conception sur mesure, conçue par BITO Storage Systems et utilisant des poutres et des montants standard, permet de placer des moteurs pesant jusqu'à 6 tonnes et stockés sur des palettes d'une tonne (spécialement conçues par le fabricant local Rilmac). Le stockage a lieu au rez de chaussée et au premier niveau. Les emplacements de niveau supérieur peuvent supporter jusqu'à 4 tonnes.
Siemens n’avait jamais stocké de moteurs sur palette auparavant et c’était aussi la palette la plus lourde que BITO n'ait jamais stockée. BITO Allemagne a développé un prototype de structure avec des composants produits et testé sur le site existant de Siemens avec le moteur le plus lourd - une turbine à gaz SGT de 6 tonnes - et sur une palette de 1 tonne.
Le GSOC comprend également 700 emplacements dans des rayonnages à palettes standard pour le magasin en vrac et 3 350 emplacements dans un entrepôt de grande hauteur avec des couloirs étroits.
Dix navettes Kardex Remstar XP500 de 11 mètres de haut permettent le stockage économe et la récupération efficace de petites pièces.
Transport interne sécurisé et efficace
La santé et la sécurité étant une priorité de la conception, Siemens a collaboré étroitement avec BITO et Kardex pour mettre au point un système de transport interne innovant sans conducteur, afin de séparer les zones de travail des véhicules et des personnes, tout en assurant un transfert rapide et sûr des articles entre la réception des marchandises, les navettes Kardex et les stations de conditionnement.
Six AGV BITO LEO Locative circule en permanence, en suivant le marquage au sol. Les codes à barres posés au sol donnent des instructions à chaque LEO et le guident de manière fiable vers une station de transfert où il dépose son sac et collecte tout le matériel en attente.
Les conteneurs pliables sont utilisés pour le transport interne. Le système assure le stockage de bacs vides au-dessus des stations LEO utilisant des rayonnages dynamiques colis comme stock-tampon. Lorsqu'un article arrive à l'entrepôt, il est retiré de son conteneur et placé dans le bac approprié d'une unité Kardex. Les bacs vides et pliables sont ensuite repliés et introduits à l'arrière d'un couloir SDS pour rouler vers l'avant, garantissant ainsi la disponibilité d'un bac lors du passage d'un AGV LEO.
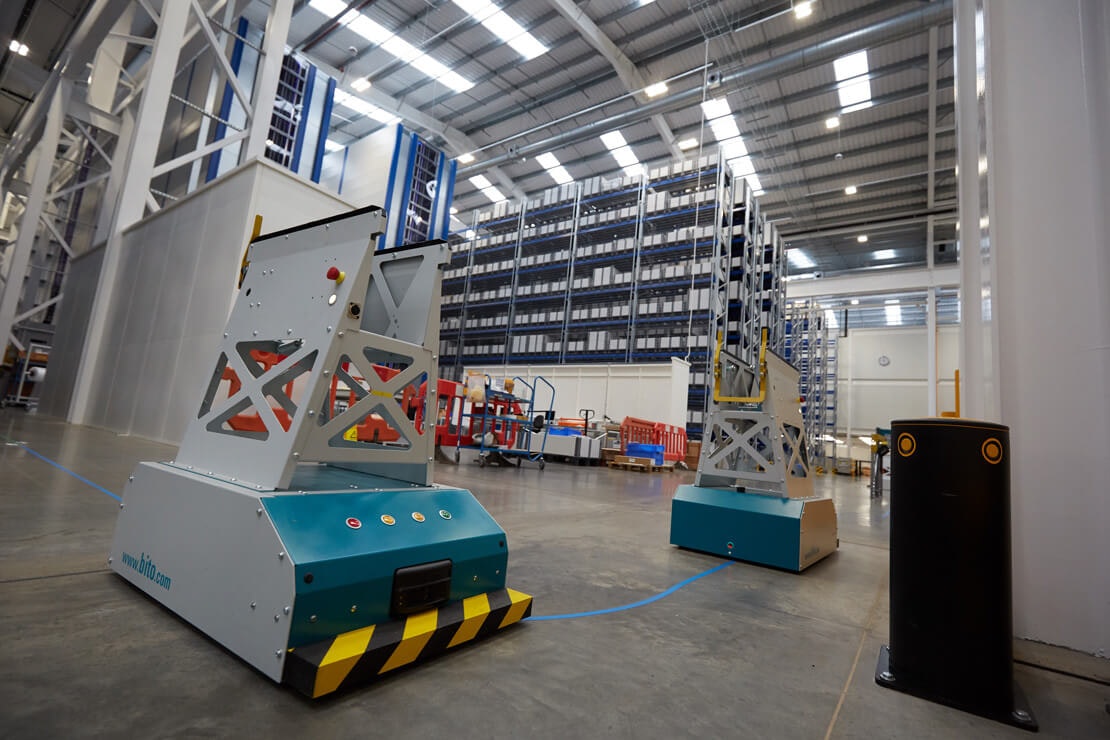
Préparation des petites pièces
Les dix navettes Kardex offrent un total de 76 800 emplacements et une flexibilité optimale pour l’emplacement des petites pièces. Chaque niveau contient dix conteneurs de 600 x 400 mm, lesquels peuvent être séparés en nombre et en taille requis d'emplacements de bacs à l'aide de séparateurs en plastique. Par conséquent, il est possible de créer un maximum de 80 emplacements de stockage par niveau d’entreposage, dont la taille peut également varier en fonction des besoins.
Les commandes prises dans des bacs sont placées sur une station en attente de la collecte par un LEO qui les emmènera à la station d’emballage, ce qui permet aux agents de s’acquitter de leur tâche suivante. Ce « tampon » donne également à Siemens une visibilité claire des travaux en cours dans chacun des domaines.
Le logiciel SAP Warehouse Management fonctionne de manière transparente avec la solution pour maintenir les stocks à jour en temps réel via des codes à barres.
Dans les temps impartis et dans le budget
La construction du GSOC a commencé en mai 2017, avec le premier chantier en octobre 2017 et l'aménagement de l'entrepôt à partir de la fin novembre. Avant Noël, tous les rayonnages BITO et les navettes Kardex étaient installées. La remise des nouvelles installations a eu lieu le 21 mars et a commencé le 2 avril.
Grâce à une excellente gestion de projet et aux communications avec les fournisseurs impliqués, le GSOC a été achevé avec succès, dans les délais impartis et dans les limites du budget imparti, afin de fournir un service de pointe aux clients de Siemens.
Les clients ont été informés des avantages de la nouvelle installation et une transition sans heurt a permis d'intégrer la gamme complète de 15 000 articles dans la nouvelle installation en l'espace de 6 semaines, tout en maintenant les niveaux de service à la clientèle.
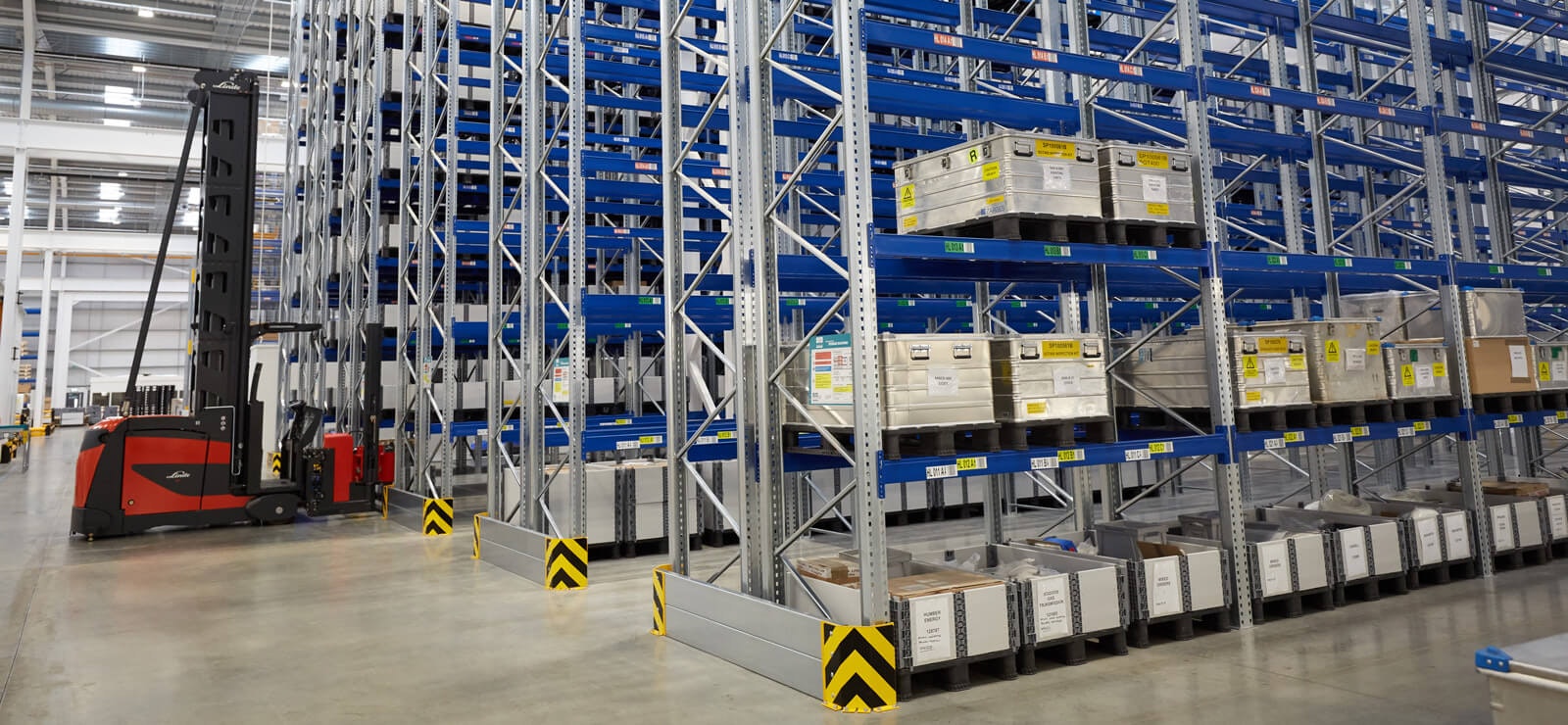
Résultats clés
Le GSOC sépare les zones de chariots élévateurs et des opérateurs en utilisant des LEO pour transporter des marchandises. Les dispositifs d'arrêt sur les chariots élévateurs à fourche et les LEO empêchent les collisions. Les LEOs diminuent également la manutention manuelle.
En termes d'avantages financiers, l'investissement de 400 000 £ représente une économie considérable sur les 3 millions de £ supplémentaires nécessaires sur le plan initial de construction d'une installation de 10 000 mètres carrés sur un site contraint. Les rayonnages permettent d'économiser 1 500 m², tandis que les navettes Kardex permettent d'économiser 1 200 m². Par rapport à l'espace de stockage précédemment requis, le nouveau système de racks réduit de deux tiers l'espace de stockage pour les turbines.
Le système LEO à faible coût offre un retour sur investissement (ROI) dans l’année, comparé à la période habituelle de 5 ans pour les AGV conventionnels. Contrairement aux autres AGV, l’installation LEO est simple et rapide: les unités suivent les marquages au sol, ce qui leur donnent toute la souplesse nécessaire pour reconfigurer et maximiser leur efficacité en retirant simplement la bande et en traçant de nouveaux itinéraires. Si nécessaire, Siemens peut commander ou louer des LEO supplémentaires directement à partir de l'entrepôt.
La productivité du personnel au sol est optimisée par la prise en charge par LEO de tâches de transport simples et par une réduction de 30% du temps de déplacement. Pour faire face à cette productivité accrue, il faudrait pour commencer deux agents supplémentaires à plein temps et trois autres par la suite lors du pic de l'activité. Les cycles de prélèvement impliquant les navettes Kardex sont deux fois plus rapides que ceux de l'ancienne installation.
Siemens reçoit également un entrepôt à l'épreuve des temps. Construit à l'aide de composants standard, le bâtiment principal peut être reconfiguré à tout moment et le GSOC a été conçu pour accueillir quatre navettes Kardex supplémentaires si nécessaire.
En fin de compte, le nouveau GSOC facilite la croissance sans avoir à augmenter les effectifs. Il garantit la disponibilité des stocks et une réponse le jour même ou le lendemain afin d'aider les clients à réduire les temps d'arrêt, qui, pour une turbine, peuvent coûter plus de 100 000 £ par heure. Les horaires habituels de fonctionnement de 07h30 à 16h00 sont prolongés pour couvrir les heures de pointe. Toute demande concernant l'entrepôt sera choisie et emballée le même jour. S'ils sont terminés avant 16h00, ils seront expédiés ce jour-là.
Clive Cox, chef de projet pour les turbomachines industrielles Siemens, donne son opinion sur la contribution importante de BITO Storage Systems au projet : « L’équipe de BITO a été très efficace lors de l'installation. Elle a été un atout précieux pour l'équipe de montage ; c’est pourquoi, selon nous, tout a très bien fonctionné. Nous sommes extrêmement satisfaits de la qualité des produits BITO. La compagnie nous a apporté son soutien et sa réactivité. Nous avons travaillé en étroite collaboration pour obtenir le service dont nous avions besoin tout au long de ce projet complexe".