La méthode Kanban dans la logistique de fabrication
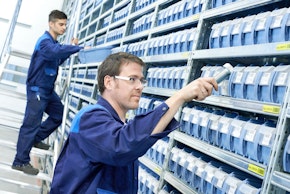
Si vous vous intéressez à la logistique, aux techniques de stockage, à l'industrie automobile ou à la gestion, vous avez probablement déjà entendu parler du Kanban. Mais qu'est-ce que le Kanban exactement ? Quand ce principe est-il utilisé ? Quels sont ses avantages ? Si vous n'êtes pas sûr que le Kanban convient à votre entreprise, cet article devrait vous apporter des réponses.
Contrôle décentralisé de la production avec le système Kanban
Le Kanban est une méthode de contrôle décentralisé de la production dans laquelle des étiquettes, Kanban en japonais, sont utilisées pour déclencher des processus de production et des processus logistiques individuels. La méthode Kanban a été introduite par le directeur de Toyota Taiichi Ohno dans les années 1950 dans les usines Toyota. L'idée provient des industries alimentaire et logistique, plus précisément du secteur de la grande distribution. Les avantages de la méthode Kanban sont le contrôle décentralisé, l'entreposage allégé et la logistique « juste-à-temps » (JAT) des pièces nécessaires à la production. Les étiquettes comportent des données importantes telles que la référence, la quantité, l'emplacement de stockage, etc. La production envoie un signal à l'étape de production en amont que de nouveaux composants sont nécessaires. Par exemple, un conteneur vide avec un bon de commande pour un composant particulier est envoyé à l'entrepôt pour activer le processus de fabrication. L'entrepôt de pièces sait maintenant que cet article doit être commandé dans une certaine quantité et envoie cette commande à la source (le fournisseur). Le fournisseur se charge de traiter la commande et livre la quantité requise du composant correspondant à l'entrepôt optimisé. L'étiquette sert donc à déclencher une commande de fabrication ou une onde de résonance spécifique qui va de la fabrication au fournisseur. Dans la deuxième variante, l'étiquette Kanban sert de carte d'identification pour le nouveau composant à produire ou à commander. Deux étapes de production adjacentes forment un circuit, ce qui facilite la coordination des étapes successives. Par exemple, le niveau de production A récupère un composant de l’entrepôt Lean (stockage tampon) et le niveau de production B recharge l'entrepôt de pièces avec le composant correspondant.
Principe « push » et « pull »
Les avantages décisifs de la méthode sont la commande décentralisée et l'autocontrôle en combinaison avec le principe « pull » (flux tiré). Le niveau des stocks peut être considérablement réduit par rapport au principe « push » classique (principe du « bring »). Le système Kanban est nettement plus robuste et flexible que la méthode classique. Grâce au contrôle centralisé classique de la production, la production s'appuie sur des estimations de la demande. Les données relatives au marché et aux ventes sont utilisées à cette fin et des prévisions sont établies sur cette base. L'entrepôt de pièces contient de nombreux composants en stock et déclenche les commandes selon le stock existant. Les commandes sont passées sur la base de prévisions tout en conservant un stock de sécurité. Le danger des systèmes « push » est l’erreur de calcul. Le risque est d’avoir du surstock, ou au contraire connaître des pénuries, ce qui signifie décevoir le client.
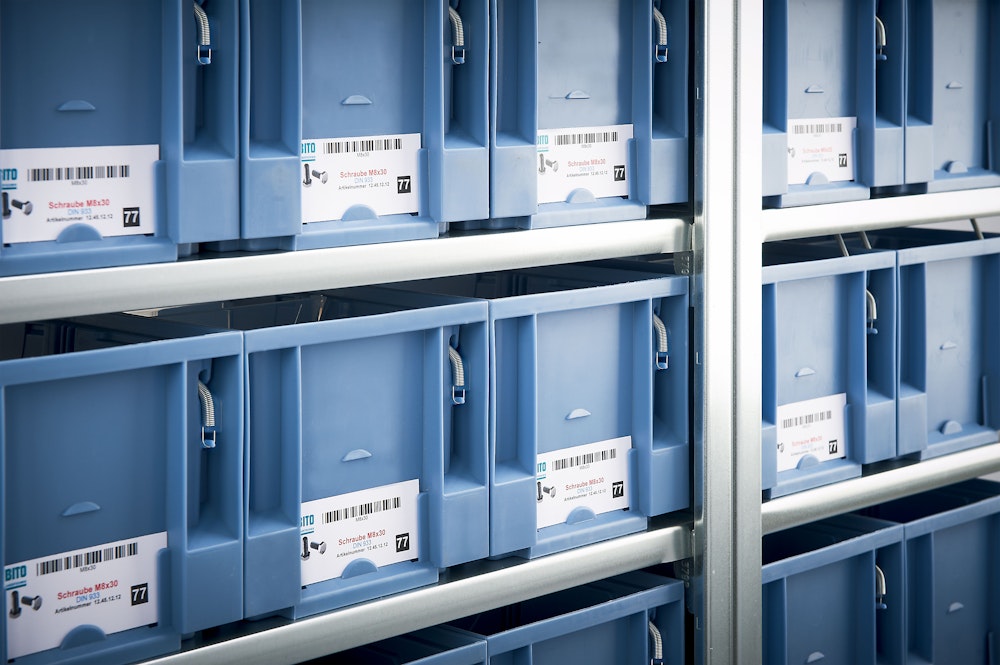
Gestion dans le système Kanban
Avec le système Kanban, personne n'a besoin de connaître l'ensemble de la chaîne de processus. Seul le conteneur « Kanban » ouvert est rempli à l'emplacement local correspondant. Le système s'avère donc auto-régulateur et auto-organisateur et repose sur des connaissances locales et des règles simples. Il ressemble à des systèmes auto-organisés de la nature, systèmes basés sur l'intelligence collective. Considérons, par exemple, les actions des armées dans un état militaire. Il en résulte une nouvelle fonction pour les responsables dans le système Kanban. Il convient d'abord de définir les conditions-cadres pour que la chaîne de processus puisse fonctionner. Mais même la conception d'une telle onde de résonance (voir ci-dessus) fait souvent appel à la sagesse collective, c'est-à-dire l'intelligence collective. Le manager se voit confier le rôle de chef d'équipe, dont la tâche est d'organiser l'auto-organisation de l'équipe. En outre, il joue le rôle de modérateur, de motivateur, de coach, de coordonnateur et de responsable des conflits ou de dépanneur pour harmoniser les processus.
Quand la méthode Kanban est-elle pertinente ?
Le système Kanban n'est pas toujours applicable. Si vous ne fabriquez que peu ou pas de produits, la méthode n'est pas adaptée. Elle convient mieux à une forte proportion de pièces identiques avec un petit nombre de variantes. Le contrôle de la production ou le flux de matières, la logistique et le réapprovisionnement sont basés uniquement sur la consommation de matières réelle au point de fourniture ou de consommation. Comme nous l'avons déjà mentionné, cette méthode offre un degré élevé de flexibilité et de réduction des stocks. Cependant, toute la chaîne logistique ou sa logistique peut être perturbée en cas d'échec d'un travail dans le processus. Si vous souhaitez implémenter le Kanban, votre entreprise doit remplir certaines conditions préalables :
- production en continu
- haut degré de standardisation des produits avec une production strictement synchronisée
- désignations uniques pour une attribution précise des étiquettes et de conteneurs gestion cohérente des conteneurs assurance qualité forte
- les fluctuations importantes de la production doivent être évitées
- les cycles de transport doivent être raccourcis et conçus de manière uniforme
Conteneurs et rayonnages Kanban
Les systèmes de rayonnages et conteneurs spéciaux pour les systèmes Kanban et la logistique sont désormais standard en intralogistique. Il s'agit notamment des conteneurs de pièces C, qui combinent les avantages des bacs de rayonnage et à bec, ou des bacs Euromodule. L'espace dans les rayonnages Kanban est utilisé de manière optimale par les conteneurs des pièces C. Ils permettent d'appliquer le top picking et le front picking, c'est-à-dire l'accès aux pièces C par l'avant et par le haut. Le disque de dosage de la boîte permet d'utiliser le volume de remplissage jusqu'en haut. Par la fenêtre, l'employé peut voir exactement combien de pièces sont encore dans le bac à tout moment. Le principe Kanban à réservoir unique est mis en œuvre dans une caisse. Si la dernière pièce est retirée par l'avant, vous pouvez utiliser la quantité fournie en tirant sur le disque de dosage. Le processus de commande de pièces C neuves est déclenché par le retrait de la carte ou des étiquettes RFID à l'arrière de la boîte. Avec le Kanban à deux bacs, la première caisse est prélevée du rayonnage après que la dernière pièce ait été retirée. La carte est retirée et le processus de commande est déclenché. Ensuite, la deuxième boîte est tirée en position avant. La boîte commandée avec les pièces de réapprovisionnement est poussée (principe FIFO) de derrière. Les bacs Euromodule sont également très adaptés à la méthode Kanban, car ils peuvent être stockés dans des rayonnages à plancher incliné ou des rayonnages dynamiques de marchandises en vrac. Ils mesurent 600 millimètres de long et sont disponibles en différentes hauteurs et largeurs. La série est conçue de manière à ce que les différentes tailles de conteneurs puissent être empilées sur une palette européenne de manière modulaire, mais néanmoins dans un composite solide. Ils sont extrêmement stables et donc empilables en toute sécurité et offrent également un grand volume interne. Les surfaces intérieures lisses permettent un nettoyage facile. Grâce aux poignées ergonomiques intégrées, le bac Euromodule peut être facilement tiré et transporté.
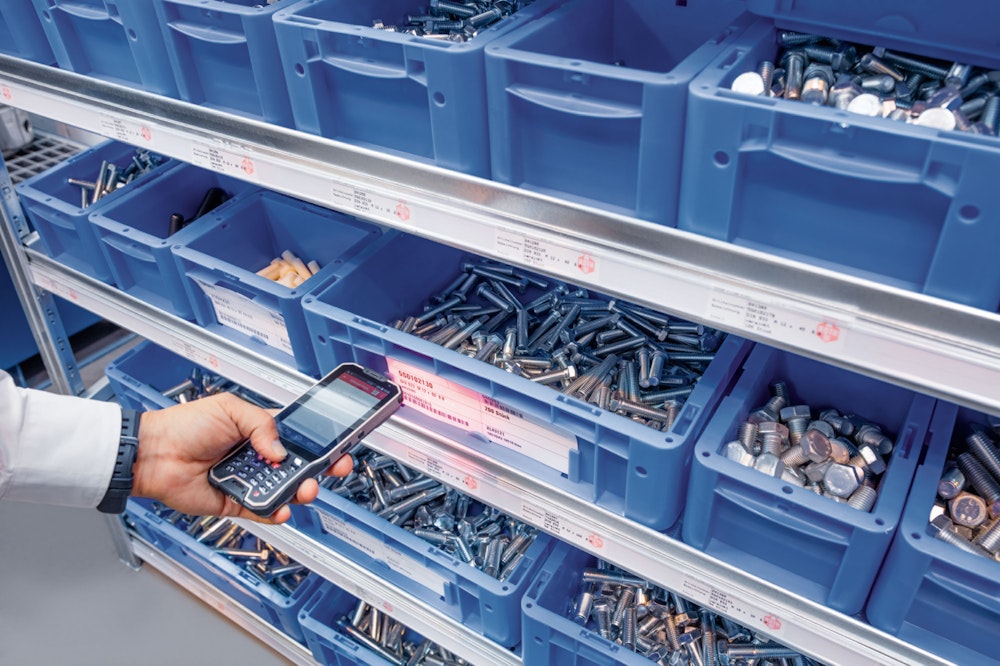
De nos jours, les supports de stockage tels que les codes à barres ou les puces RFID sont préférés aux étiquettes Kanban. Les données, ou l'ordre de fabrication, sont transmises par WIFI au système de pliage de l'entrepôt, au système ERP ou au fournisseur de composants correspondant. Dans le système de codes à barres, les codes à barres des conteneurs vides des composants correspondants sont scannés manuellement par un employé et transmis au fournisseur de composants correspondant, qui livre ensuite ces pièces. Dans un système RFID, ce processus est automatisé. Les données relatives aux articles et aux conteneurs sont automatiquement transmises du site de production du client à l'entrepôt central par identification par radiofréquence (RFID). Cela signifie que les commandes répétitives automatisées sont passées ici sans numérisation et sans enregistrement manuel. L'étiquette RFID, ou le transpondeur RFID, possède une antenne et est fixé à l'objet ou au bac Kanban correspondant. Chaque jour peut être identifié par un numéro unique de sécurité des données. En outre, un système RFID se compose d'un lecteur pour la lecture du transpondeur et d'une unité émettrice pour la transmission de données ou la commande automatique de composants pour la production.