Smart warehousing becomes the new gold standard
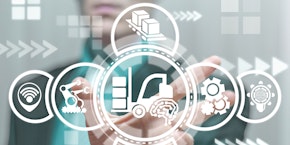
Smart warehouses have been inspired by smart factories. What both of these types of facilities have in common is that they are driven by data, which has become the ‘oil of the 21st century’. Processes in a smart warehouse will be based on data evaluated by Artificial Intelligence (AI). AI finds patterns within data, creates forecasts about the future development of processes and makes decisions automatically. Data used for analysis includes information on customers, measurements, real-time data from sensors forming the Internet of Things (IoT), analysis, monitoring, IT systems and existing warehouse solutions. It may even derive from external sources such as social networks, the Internet or from business partners. Clean data is the foundation for a successful data-driven enterprise. E-commerce operations in particular – with their small order sizes, short delivery times and unpredictability of demand – will reap great benefit from smart logistics.
The Internet of Things enables wide-ranging communication
To obtain data, warehouse technology must be equipped with sensors. In addition, all devices, industrial trucks, conveyors, robots, warehouse management systems (WMS) and other technologies must be connected via the IoT so that they can communicate with each other. The technological infrastructure within a smart warehouse will create an environment where orders and goods can be automatically received, sorted, organised, recognised and prepared for dispatch. This significantly increases productivity, quality and efficiency, while minimising errors and reducing required staff numbers.
Digital twin is the centrepiece
With smart warehousing, the warehouse and all processes taking place within it are mapped to create a ‘digital twin’. The collected data is gathered and processed centrally in the digital representation of the warehouse. Optimised execution commands are forwarded to the work equipment and to employees in the warehouse. The digital twin can be created before the actual physical warehouse to simulate future operational processes. This allows data, experience and ideas to be gathered for the physical warehouse’s construction and design. This means the warehouse to be tested before being put into operation, giving forward visibility of how it functions in relation to movement flows and different demand peaks. Furthermore, it is possible to monitor the status of the equipment operating in the warehouse – such as stacker cranes, conveyors, robots, automated guided vehicles (AGVs) – to prevent failure. The use of a digital twin has many advantages, including: higher productivity, identification of improvement opportunities, error prevention, better inventory control, cost savings and better operational monitoring.
Basis for efficient e-commerce
The continual escalation of customer expectations in e-commerce is driving the move to digitalisation in intralogistics and logistics. However, warehousing is not always intelligent, even in e-commerce companies. Extremely short delivery times, small order sizes, strongly fluctuating demand are all challenges faced by online retailers. The seamless connection of order processes in the online shop to a Merchandise Management System (MMS) is crucial to shorten the processing of orders (1). To enable smart warehousing, all logistics areas from goods receipt, storage and sorting to packaging and shipping must be digitally networked via a Warehouse Management System (WMS).
Investing in a smart warehouse is worthwhile even in times of recession, as it leads to more efficient processes, cost savings and greater customer satisfaction, and will likely result in larger order volumes. The use of AI and predictive analytics allows a forecast of the future ordering behaviour of customers. This allows orders to be picked and prepared for dispatch even before they are received.
Advantages and challenges of smart warehousing
Advantages:
As capacity planning is continuously optimised, it is possible to react more quickly in the event of bottlenecks.
Increased scalability of the warehouse – through the use of software and greater productivity, warehouse capacities can be increased.
Optimisation potential is revealed through increased transparency of the data.
Increased digitalisation and automation through the use of robots, cobots and AGVs to, for example, automate picking and picking processes and general internal logistics.
Replacing barcode scanners with RFID scanners, which only have to be aligned in the direction of RFID transponders on the articles, makes multiple or bulk scans possible.
AI can increase productivity and minimise errors in a wide range of processes including product demand forecasting, inventory management, transport capacity planning, controlling AGVs and robots, and optimising picking processes.
The IoT can be used as a data highway in a company and as a necessary prerequisite for a modern WMS. This might feature RFID scanners automatically recording the receipt of goods in the warehouse and passing the information on to the WMS, which in turn informs the robots of the specified storage location. The IoT is what makes the seamless automatic interaction of hardware and software possible.
Challenges:
Introducing the technologies and building a smart warehouse requires significant effort.
There are often also psychological hurdles among the employees, as they see their jobs threatened. This can create a huge change process in which all employees must be involved. Appropriate change management methods must therefore be applied.
A radical rethink is necessary for all individuals and company departments involved. Processes must be completely rethought and redesigned.
The introduction of mobile devices, scanners, pick-by-light, pick-to-light and smart wearables is just the beginning. Implementing the full range of AI-driven technologies is another big step for the workforce and may need to be broken down into smaller intermediate steps.
A new working world for employees
There is a danger that employee competences, such as self-organisation and knowledge of certain contexts and dependencies, could increasingly fade into the background and may even become a hindrance, since efficient processes and action commands generated by AI algorithms can no longer be comprehended by humans. A completely new working environment needs to be created in which employees and robots work together ‘hand in hand’, deployed according to individual strengths and abilities. This can be a great challenge, especially for long-serving employees. However, at the same time, work continues to become physically less strenuous.
Literature:
Kluckow Marcel, The smart warehouse takes e-commerce to the next level, November 2020, JLL Jones Lang LaSalle Inc, Link
BITO expertise, future of the warehouse + whitepaper
BITO expertise, process mining optimises business processes
BITO expertise, How artificial intelligence is revolutionising logistics, Link