Optimising the value chain with AGVs
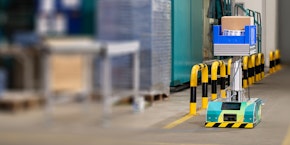
The fourth industrial revolution with industry standard 4.0 sets the framework for the development of industry, companies and the technologies used by them. Machines, plant, devices and cyber-physical systems are to be networked to communicate with each other in order to ultimately optimise the entire value chain (1). A value chain is an ordered sequence of activities in which value is created and resources are consumed to produce products and services (2). So-called smart production leads to an improvement in manufacturing performance through the analysis of huge amounts of data from networked systems and the automation of processes. Through the use of artificial intelligence (AI), (3), processes can be simulated on a digital twin of a plant or an entire factory. Predictive analytics can be used to identify business trends such as the demand behaviour of a company's customers. In this way, a company's marketing and sales actions can also be adapted to them. Predictive maintenance is intended to prevent the imminent failure of components or the failure of entire machines and systems and thus reduce downtimes. Data analysis with AI also allows slow or inefficient production to be detected and corrected accordingly.
Automation to improve the value chain
Potential also exists for optimisation of intralogistic processes in that the material and goods flows of the value chain can be automated and optimised particularly easily, e.g. through automated guided vehicles (AGVs) (4, 5). According to VDI Guideline 2510 "Automated Guided Vehicles", an AGV consists of one or more driverless vehicles for transport, systems for performance control, location determination, position detection and data transmission, a corresponding infrastructure as well as peripheral systems in the company such as charging stations. An AGV is an internal floor-bound conveyor system (industrial truck) that usually consists of several AGVs for pulling or carrying conveyed goods. Different solutions exist in terms of vehicle control which can be based, for example, on optical or inductive processes, magnetic marks, adhesive strips on the floor, GPS or transponders. For the automation of material transport and handling, for example in production or order picking, corridor-bound Automated Guided Vehicles (AGV) with integrated drive and active or passive load handling devices are used. AGVs can be used to automate the flow of goods and materials permanently, flexibly and reliably. Because they are easily expandable and adaptable, an AGV competes with other transport systems such as industrial trucks, conveyors, but also with human labour. Furthermore, lean production systems in companies increasingly require forklift-free operation. Up to now, for example, the automotive industry has mostly used tugger trains with drivers. However, automation is also steadily increasing in this area. In a company's production logistics, tugger trains and AGVs complement each other perfectly and allow material and components to be supplied right to the assembly line. Automated tugger trains and AGVs will make a major contribution to higher value creation and an optimised value chain.
Advantages and disadvantages of AGVs
Automated guided vehicles have an extraordinary number of advantages (6) for the creation of value in the company, such as:
Flexibility - the driverless transport system, usually consisting of several driverless vehicles, can be configured and supplemented with additional vehicles depending on the application. The routes can be easily changed. In addition, AGVs exist with low payloads of a few kilograms up to the heavy load range with, for example, 50 tonnes. The speed ranges of the solutions also vary greatly, whereby these are primarily limited by any passenger traffic, the braking distances and the load changes caused by the goods being transported.
Changes to the warehouse layout, warehouse and goods structure can also be easily made and improved.
The error rate is reduced through the use of driverless vehicles and the productivity of the company processes is increased, as employees can be removed from affected work areas (saving on personnel costs). In addition, it can be used permanently around the clock without a break thus greatly increasing value creation and productivity.
The speed of intralogistics processes is increased.
Due to the smaller number of employees and the absence of forklift trucks, accidents are minimised and employees are physically more relaxed.
The system also adapts autonomously to changing processes during order peaks.
They can be used both outdoors and indoors.
They pay for themselves quite quickly due to the increased productivity, optimised value chain and personnel savings. In addition, the operating and maintenance costs are very low.
Of course, every solution with driverless vehicles also has disadvantages for a company.
The automated guided vehicle system cannot yet react on its own to operational faults such as empty shelves and damage. In these instances human intervention is still required.
The system of driverless vehicles competes with human labour. There is a danger that humans will increasingly be replaced by AI and robots. However, a solution may lie in the harmonious interaction of the long-standing know-how and experience of humans with AI and supporting robots (cobots).
LEO locative
With LEO locative (7), BITO offers companies a driverless transport system to improve processes and optimise the value chain, which does not require WLAN or expensive IT (material flow computers). LEO is controlled via an optical track stuck to the floor and markers also attached to the floor. The driverless transport system is designed as a plug-and-play application: simply stick the coloured track tape on the floor in the desired direction of travel, position the markers for the stop and travel commands and place the LEO stations at the defined stop positions. The marker commands are scanned by the LEO and executed directly. Due to the easy-to-change configuration, it is possible to try out new ideas without long waiting times. Step by step, processes can thus be optimised when using the system and the best solution for the material flow can be found. By optimising company processes, for example in production logistics (8), the entire productivity of the value chain is improved. The investment costs for the system are very low, therefore it pays for itself after a short time.
Literature
1 BITO Expertise, Flexible Manufacturing in the Smart Factory, Link
2 Value chain definition, link
3 BITO Expertise, Possible uses of AI in logistics, Link
4 BITO Expertise, Digitalisation in intralogistics, Link
5 BITO expertise, Automated guided vehicles - how to keep track, Link
6 Raphael Michalek, Driverless transport systems, What are driverless transport systems? Definition & advantages, January 2019, MM Logistik, Link
7 BITO Lagertechnik Bittmann GmbH, LEO Locative, The driverless transport system for containers and cardboard boxes, Link
8 BITO Expertise, Process Optimisation in Production Logistics, Link