Combining manual and automated storage & picking systems
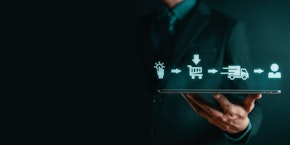
The introduction of industry 4.0, competitive pressures and the accelerating pace of ecommerce make automation, or at least partial automation, of warehouse processes increasingly necessary. Many companies are faced with the question of which processes they can or want to automate. Do certain manual processes in the warehouse even make sense? Which interfaces need to be specifically considered when combining automated and manual solutions? Processes that are particularly suitable for automation include the movement of goods between warehouse areas, order picking and the allocation of orders or efficient route planning, usually through a warehouse management system (WMS). To be successful, automation solutions need to be flexible and scalable so that they can be adapted to changing market conditions and business growth.
Different levels of warehouse automation
In manual warehouses, because most tasks and decisions are made by people, the error rate can unfortunately be relatively high. Despite this, manual warehouses also have advantages - they can be easily scaled, temporary workers can be hired and the processes are usually manageable. The knowledge and potential of (experienced) employees in the company can also be put to good use. However, purely manual warehouses are only suitable for a relatively small product range and a small number of SKUs. The first stage of automation is the introduction of a warehouse management system (WMS), without which automated systems cannot be controlled. The WMS takes over the decision-making and allocates orders and routes according to certain criteria. It manages product quantities and storage locations and controls the individual transport systems. From the host system stored above it, an ERP or merchandise management system, the WMS receives orders, manages them in a database and, after appropriate optimisation, passes them on to the connected conveyor system for control. It thus takes over the control, monitoring and optimisation of complex warehouse and distribution systems. The introduction of a WMS also usually leads to an improvement in order picking and the use of picking systems such as voice picking or pick-to-light. The next level of automation is the introduction of further automated warehouse systems and solutions up to full automation of the warehouse (BITO Briefings 1 below).
Requirements for automation in the warehouse
When evaluating the automation of processes in the warehouse, a number of factors need to be considered. Ideally, the warehouse operates continuously (24/7), the target processes must be clear and "validated" and there should be no, or very small seasonal fluctuations. In addition, there needs to be long-term planning certainty with regards to warehouse requirements such as container types, batch sizes, throughput, etc. The more these requirements deviate from the "ideal automated warehouse", the more manual processes should be incorporated. Of course, automated warehouses have advantages and disadvantages, which can be read about in detail in BITO Briefings (1). The decisive advantages are cost and personnel savings, error reduction, an increase in safety, higher throughput and improved customer satisfaction. As skilled personnel are becoming harder to find, automated warehouses are becoming more and more interesting. However, automation can also be started without a WMS and even without Wifi. The BITO LEO automated guided vehicle (AGV) automates the transport of totes, cardboard boxes and trays without any IT connection via floor tracks, smart box and marker (2).
Interfaces in the combination of the different processes
The advantages of an efficient and well-designed warehouse include shorter transport and walking distances, faster access times, higher throughput, good delivery quality and flexibility. Material flows are optimised and the fluctuations between supply and demand are balanced thanks to a high level of transparency and visibility of inventory levels. A warehouse system not only includes manual or automated racking systems, but also a control system, warehouse management, warehouse and conveyor technology and warehouse personnel (3). The main interface in combining different manual and automated storage systems is the WMS. The task of the WMS is to manage and optimise internal warehouse systems (4, 5). The different turnover rates and access times of the manual and automated warehouse systems must be taken into account not only in warehouse planning, but also in the storage and retrieval of goods as well as order allocation to the order pickers. The WMS assigns storage positions to all goods (slow, medium and fast-moving) based on criteria and rules previously defined by the appropriate manager. Fast-moving items are stored, for example, in flow racks and automated racking systems (miniload, automatic small parts stores, autostore, etc.) (6). A higher-level WMS synchronises the movements of all automated solutions, such as the pallet shuttles, up to more complex machines such as sorting and conveyor systems, AGVs or stacker cranes, by means of a warehouse control system (WCS). The WCS enables the efficiency of processes in the automated warehouse. In times of Industry 4.0, the importance of communication between machines or automated and manual solutions via the Internet of Things (IdD) is increasing more and more. Through IdD or the use of artificial intelligence (AI), all manual and automated processes can be optimised, as the data is easily accessible in the network. This leads to the minimisation of throughput times and an optimisation of the entire logistics.
Automation of order picking
In the course of automating processes, the picking of customer orders of course, cannot be ignored. The use of WMS, WCS and Industry 4.0 technologies naturally also enables the integration of automated systems in order picking. These include robotic systems such as automated picking systems, storage and picking robots, stacker cranes, shuttles, automatic conveyor systems, but also packaging and labelling machines. Automated picking can improve the accuracy, speed and safety of order picking. Of course, it can also mean a reduction in order pickers and the processes thus become more cost-effective. According to the robot manufacturer Magazino, autonomous picking robots are particularly suitable for small batch sizes - a wide range but small quantities in e-commerce (7).
Literature
1 BITO Briefings, When does automation make sense in the warehouse?, Link
2 LEO Locative - the solution for automated container and carton transport, Link
3 BITO Briefings, What are storage systems?, Link
4 Definition WMS/ WMS, Warehouse Logistics, Link
5 Technical rule, VDI 3601:2015-09, Warehouse management systems, Association of German Engineers (VDI), Link
6 BITO Briefings, Influence of turnover rate and rotation of goods on warehouse planning and management, Link
7 BITO Briefings, Robots and automation in the warehouse 4.0, Link