Siemens rüstet sich für die Zukunft mit neuem Logistikzentrum
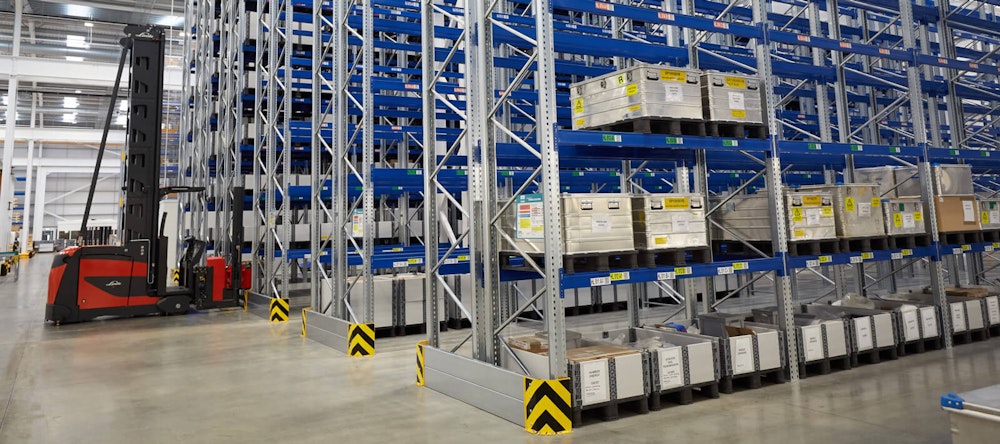
Siemens Industrial Turbomachinery investierte 48 Mio. £ am Standort Teal Park, um seine Lagerlogistik in einem neuen Global Service Operation Centre zu konsolidieren und damit die Arbeitssicherheit zu erhöhen, Durchlaufzeiten zu verkürzen und die Lieferbereitschaft zu verbessern. Das zukunftsweisende Projekt wurde termingerecht und budgetkonform fertiggestellt.
Siemens Industrial Turbomachinery entwickelt, konstruiert und wartet kleine Gasturbinen für die industrielle Nutzung, unterstützt von Mitarbeitern an 3.500 Standorten in 90 Ländern. 1.500 Standorte bleiben für Großkunden aus der Öl- und Gasindustrie, weitere industrielle Abnehmer, Krankenhäuser und Papierfabriken bestehen.
Um mit erstklassigem Kundenservice einen Wettbewerbsvorteil zu erlangen, der für eine nachhaltige Entwicklung unerlässlich ist, investierte Siemens 13 Millionen Pfund in den Bau eines neuen Global Service Operation Centre (GSOC) neben seinem Instandsetzungswerk am Standort Teal Park in Lincoln, um Service und Logistik zu konsolidieren. An diesem Standort wurden insgesamt 48 Millionen Pfund investiert.
Neben dem Hauptziel einer konsolidierten Lagerhaltung für Antriebselemente, Werkzeuge und Ersatzteile hatte man auch die Verbesserung von Gesundheits- und Sicherheitsaspekten, Wachstumsförderung, Erhöhung der Durchlaufgeschwindigkeit, Kapazitätserweiterung und Kostensenkung im Blick.
Die Konsolidierung umfasste die Zusammenlegung des Standorts für die Lagerung von Teilen für kleine Gasturbinen, Antriebselementen und Werkzeugen mit weiteren externen Lägern und dem Betrieb für aeroderivative Gasturbinen von Siemens.
Eine Betriebsfläche von insgesamt 12.000 Quadratmetern sollte nun in das neue 7.000 Quadratmeter große GSOC passen mit dem Ziel, gleichzeitig die betriebliche Effizienz zu maximieren.
In enger Zusammenarbeit mit Anlagenbauern und Herstellern von Lagertechnik stellte sich Siemens dieser Herausforderung. Entstanden ist eine innovative Intralogistiklösung für die Lagerung und Kommissionierung der 15.000 Artikel des Unternehmens - von Schrauben und Bolzen bis hin zu 6 Tonnen schweren Turbinen.
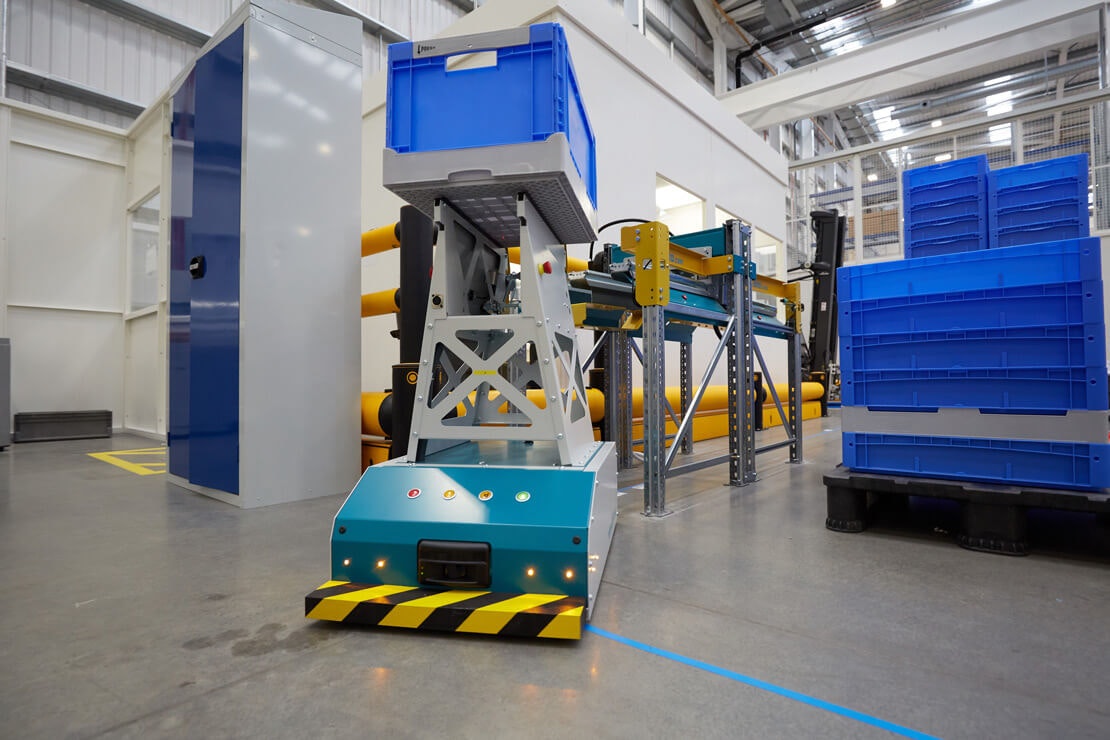
Maßgeschneiderte Regale für die Lagerung von Turbinen reduzieren den Platzbedarf
Am bisherigen Standort lagerten diese schweren Turbinen auf dem Hallenboden und beanspruchten eine große Lagerfläche, wobei der Platzverlust durch den ungenutzten Raum darüber beträchtlich war. Darüber hinaus war diese Art der Lagerung nicht übersichtlich. Dieser „Luftraum“ musste genutzt werden, um die Lagerhaltung auf eine Grundfläche von 7.000 Quadratmetern zu komprimieren, während eine effizientere Bestandsführung erforderlich war, um den Turbinen einen festen Stellplatz zu zuweisen.
Die Antwort war eine beeindruckende Palettenregalanlage mit 3 Ebenen und 72 Stellplätzen, die von einem induktionsgeführten Seitenstapler bedient wird. In der von BITO Storage Systems maßgeschneiderten Anlage mit Standardtraversen und -stützen werden bis zu 6 t schwere Turbinen auf Paletten mit einem Gewicht von 1 Tonne gelagert, einer Spezialanfertigung des lokalen Herstellers Rilmac. Die Lagerung erfolgt auf der Bodenebene und auf der ersten Fachebene. Die Ebenen darüber sind für ein Gewicht von bis zu 4 Tonnen ausgelegt.
Bisher hatte Siemens seine Turbinen noch nie in Regalen gelagert. Und BITO musste eine Lösung für ein derart hohes Palettengewicht ausarbeiten. BITO Deutschland entwickelte einen Regal-Prototyp, dessen Bauteile am bestehenden Standort von Siemens getestet wurden, und zwar mit der schwersten Turbine, einer Gasturbine SGT mit einem Gewicht von 6 t, gelagert auf einer 1-Tonnen-Palette.
Das GSOC umfasst zudem 700 Stellplätze für Standardpaletten für Massenware und 3.650 Stellplätze in einem Schmalgang-Hochregallager.
Zehn 11 Meter hohe Kardex Remstar XP500 Shuttles sorgen für eine platzsparende Lagerung und Entnahme von Kleinteilen.
Sicherer und effizienter innerbetrieblicher Transport
Unter Beachtung aller Sicherheitsaspekte und in enger Zusammenarbeit mit BITO und Kardex installierte Siemens ein innovatives, fahrerloses internes Transportsystem zur Entkoppelung von fahrzeugbedienten und mitarbeiterbedienten Bereichen, das einen schnellen und sicheren Warenumschlag zwischen dem Wareneingang, den Kardex Shuttles und den Packstationen sicherstellt.
Sechs BITO LEO Locative Transporter zirkulieren kontinuierlich auf der auf dem Boden verlegten Spur. Ebenfalls auf dem Hallenboden angebrachte Barcodes geben jedem LEO Anweisungen und führen ihn zuverlässig zu einer Übergabestation, wo der mitgeführte Behälter abgesetzt und ein neuer Behälter aufgenommen wird.
Für den internen Transport werden Faltbehälter eingesetzt. Leere Behälter sollen in einem Stückgut-Durchlaufregal über den LEO-Stationen bevorratet werden. Wenn ein Artikel zur Einlagerung aus dem Wareneingang kommt, wird er aus dem Behälter entnommen und in den entsprechenden Behälter einer Kardex-Einheit gelegt. Die leeren Behälter werden dann zusammengeklappt in einen Kanal auf der Beschickungsseite des Stückgut-Durchlaufregals gelegt, von wo sie zur Entnahmeseite vorlaufen. Somit stehen den LEO-Transportern für Warenausgänge immer genügend leere Behälter zu Verfügung.
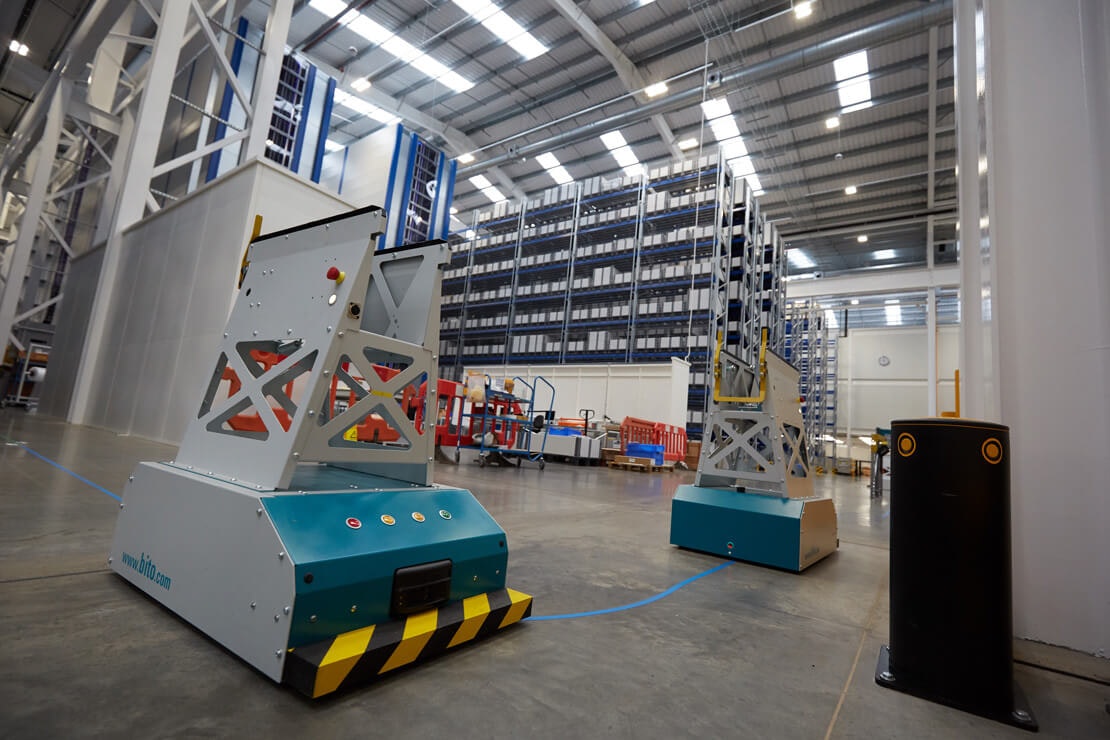
Kleinteilekommissionierung
Die zehn Kardex Shuttles bieten insgesamt bis zu 76.800 Stellplätze und somit optimale Flexibilität bei der Kleinteileplatzierung. Auf jeder Fachebene befinden sich zehn 600 x 400 mm große Behälter, die mit Hilfe von Fachteilern aus Kunststoff in die gewünschte Anzahl von Stellplätzen unterteilt werden können. Dadurch können maximal 80 Lagerplätze pro Fachebene entstehen, die je nach Bedarf auch unterschiedlich groß sein können.
Aufträge, die in Behälter kommissioniert werden, werden an einer Station platziert, bis sie von einem LEO-Transporter abgeholt und zur Packstation gebracht werden. Unterdessen können die Mitarbeiter die nächste Anforderung bearbeiten. Dieses Pufferlager erlaubt außerdem einen genauen Überblick über die in Arbeit befindlichen Anforderungen in jedem Bereich.
Die SAP Warehouse Management Software arbeitet nahtlos mit der Lösung zusammen und aktualisiert Bestände in Echtzeit über Barcodes.
Termingerecht und im Rahmen des Kostenplans
Der Bau des GSOC begann im Mai 2017, wobei die erste Baustelle im Oktober 2017 und die Lagerausstattung Ende November stattfand. Vor Weihnachten wurden alle BITO-Regale und die Kardex Shuttles installiert. Die Übergabe der neuen Anlage erfolgte am 21. März, die Inbetriebnahme am 2. April.
Durch exzellentes Projektmanagement und die Kommunikation mit den beteiligten Lieferanten konnte das GSOC budgetkonform und innerhalb der vorgegebenen Zeit erfolgreich abgeschlossen werden. Siemens kann seinen Kunden somit das Serviceniveau eines Branchenführers bieten.
Die Kunden wurden über die Vorteile der neuen Anlage informiert, und nach einem nahtlosen Übergang wurde das gesamte Produktportfolio von ca. 15.000 Artikeln innerhalb von 6 Wochen in die neue Anlage eingelagert, wobei ein durchgängiger Kundenservice gewährleistet war.
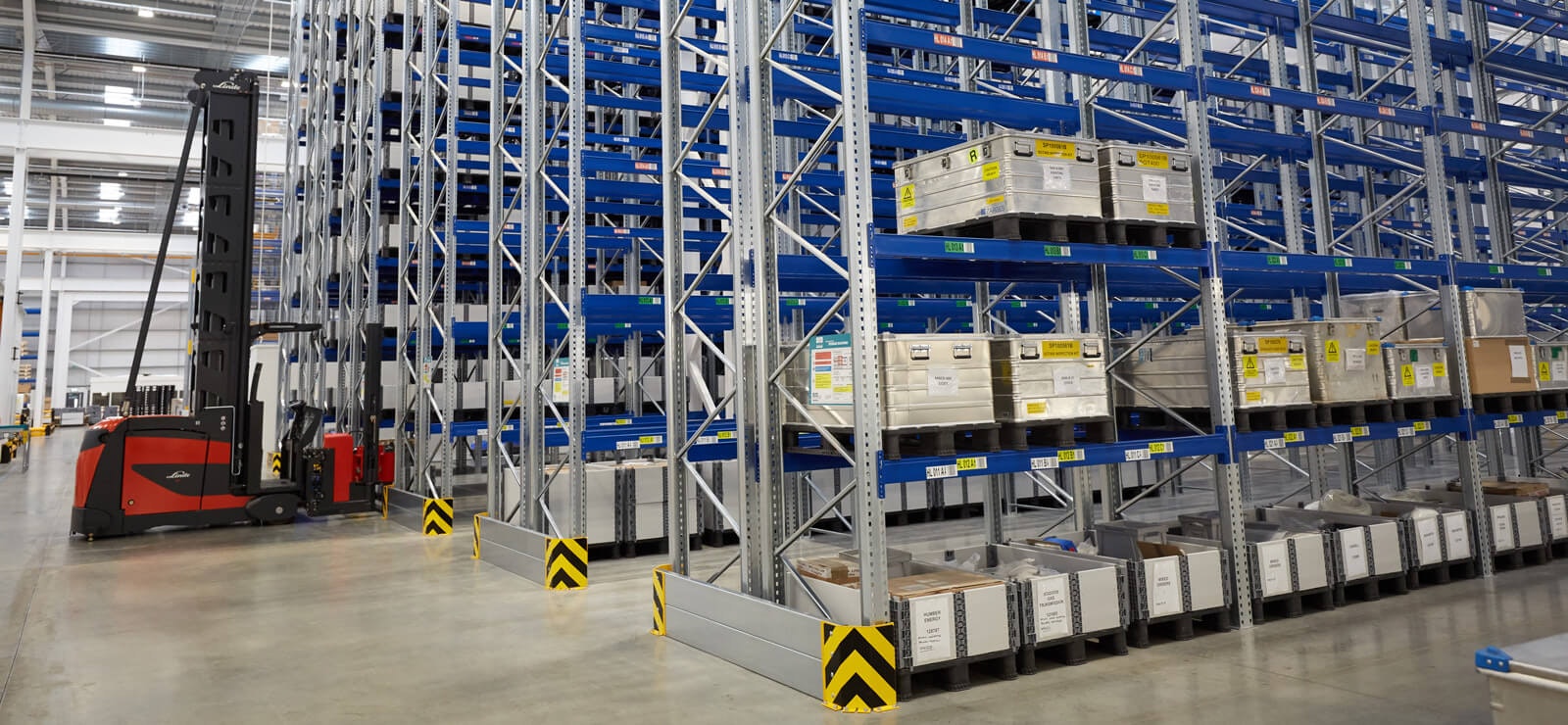
Die wichtigsten Ergebnisse im Überblick
Durch den Einsatz von LEO-Transportern werden im GSOC die von Mitarbeitern bedienten Bereiche von den Gabelstaplerbereichen getrennt. Sensoren zur Hinderniserkennung an Gabelstaplern und den LEO-Transportern verhindern Kollisionen. LEO-Transporter minimieren das manuelle Handling.
Was die finanziellen Vorteile betrifft, so stellt die Investition in Höhe von 400.000 £ in die Regalanlage eine enorme Einsparung gegenüber den zusätzlichen 3 Millionen £ dar, die für den ursprünglichen Plan zum Bau einer 10.000 qm großen Anlage auf dem räumlich begrenzten Gelände erforderlich gewesen wären. Durch die Regalanlage werden 1.500 qm Stellfläche eingespart, während die Kardex Shuttles insgesamt 1.200 qm einsparen. Im Vergleich zur bisher benötigten Lagerfläche reduziert die neue Regalanlage die nun benötigte Lagerfläche für Turbinen um zwei Drittel.
Die kostengünstigen LEO-Transporter ermöglicht eine Anlagenrendite (ROI) innerhalb eines Jahres, verglichen mit dem für konventionelle FTS typischen Zeitraum von 5 Jahren. Im Gegensatz zu anderen FTS können LEO-Transporter einfach und schnell in Betrieb genommen werden, da die LEOs dem auf dem Boden liegenden Band folgen und somit völlige Flexibilität ermöglichen, falls die Streckenführung geändert werden soll. Das Band kann einfach hochgezogen werden, um eine neue Route zu verlegen. Siemens kann bei Bedarf zusätzliche LEOs direkt ab Lager bestellen oder anmieten.
Die Produktivität der Kommissionierer wird maximiert, da einfache Transportaufgaben nun von LEO-Transportern übernommen werden und sich Wegzeiten um 30% verringern. Eine solche Produktivitätssteigerung ließe sich nur durch zwei zusätzliche Vollzeitkräfte bei der Inbetriebnahme und weitere drei bei Betriebserweiterung erzielen. Mit den Kardex Shuttles können doppelt so viele Positionen wie bisher bearbeitet werden.
Dank der neuen Lagerausstattung kann Siemens nun flexibel auf die zukünftige Bedarfsentwicklung reagieren. Durch den Einsatz von Standardbauteilen kann das Regal für die Lagerung von Turbinen jederzeit neu konfiguriert werden. Außerdem wurde das Distributionszentrum so konzipiert, dass bei Bedarf Platz für vier weitere Kardex Shuttles vorhanden ist.
Zudem ermöglicht das neue Logistikzentrum Wachstum, ohne dass die Mitarbeiterzahl erhöht werden muss. Sowohl die Lagerverfügbarkeit als auch die Lieferfähigkeit am selben oder nächsten Tag ist sichergestellt, um Kunden bei der Minimierung von Ausfallzeiten zu unterstützen, was im Fall einer benötigten Turbine Kosten von mehr 100.000 £ pro Stunde verursachen können. Die normalen Betriebszeiten von 7.30 bis 16.00 Uhr können ausgedehnt werden, um Bedarfsspitzen abzufangen. Alle Lageraufträge werden noch am selben Tag kommissioniert und verpackt, und, falls dies bis 16.00 Uhr erledigt ist, noch am selben Tag verschickt.
In seiner Stellungnahme zur Projektabwicklung sagte Clive Cox, Projektleiter bei Siemens Industrial Turbomachinery: "Das BITO-Team vor Ort war sehr effizient und eine wertvolle Ergänzung unserer Montagegruppe. Aus unserer Sicht hat alles sehr gut funktioniert. Wir sind mit der Qualität der BITO-Produkte sehr zufrieden. BITO hat uns hervorragend unterstützt, hat auf Anforderungen sehr schnell reagiert, eng mit uns zusammengearbeitet und das komplexe Projekt umfassend betreut.“